Plastics (Resins) expand and contract in volume with changes in temperature and pressure. This article discusses the molding shrinkage rate related to the design of injection molds and molding conditions, and the shrinkage rates of major crystalline and amorphous plastics.
Injection Molding Shrinkage Overview – Plastic Mold Shrinkage Chart, Formula, Calculation
In the injection molding of thermoplastic plastics, the desired dimensions of molded products can be obtained by utilizing the molding shrinkage phenomenon. Molding shrinkage refers to the phenomenon where the volume of molten resin filled inside the mold cavity shrinks as it cools and solidifies. This degree of shrinkage is called the “molding shrinkage rate.” If the molding shrinkage rate is scientifically and empirically known, the mold cavity can be made slightly larger to accommodate this shrinkage, allowing molded products of the intended dimensions to be manufactured. So if you want to make the perfect mold for product manufacturing, keep reading to learn how the plastic shrinkage rate work in molding.
What is Molding Shrinkage?
When plastics are heated, the molecular motion increases, causing volume expansion, and conversely, volume contracts when cooled. In injection molding, the volume-expanded molten resin is filled into the mold, and as it cools, it contracts. When the gate solidifies (gate seal), no more resin can be introduced into the cavity, resulting in volume shrinkage, and the dimensions of the molded product become smaller than the cavity dimensions. This is referred to as molding shrinkage. The extent of this shrinkage is quantified by the molding shrinkage rate.
Injection Molding Shrinkage Rate Calculation
The volume of a resin (plastic) expands more at higher temperatures and contracts more at lower temperatures. The ratio of this change is known as the molding shrinkage rate, which can be calculated from the difference in dimensions between the molded product and the mold cavity.
How to Calculate Molding Shrinkage Rate:
When cooled, the volume shrinks
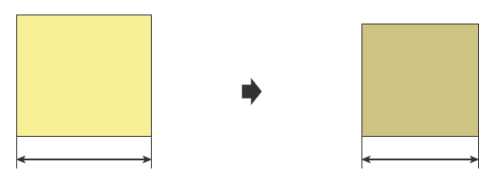
Molding Shrinkage Rate (S) = ((Length before shrinkage) – (Length after shrinkage)) / (Length before shrinkage)
Formula for Calculating Molding Shrinkage Rate (S): S = (L0-L1)/L0
Where:
- Length before shrinkage (L0) = Mold dimensions
- Length after shrinkage (L) = Dimensions of the molded product at room temperature
For example, the shrinkage rate of ABS resin is 4/1000 to 9/1000. This means that something with a total length of 1000mm will shrink by 4mm to 9mm. Therefore, the mold must be made larger than the actual target dimensions.
For example, if you are aiming for a size of 100mm using a resin with a shrinkage rate of 4/1000, you would calculate the mold size as follows:
100mm x 1.004 = 100.4mm
Thus, the mold dimensions should be set to 100.4 mm.
The shrinkage rate varies depending on the type of resin. It also changes with the pressure during molding; generally, the higher the pressure, the smaller the shrinkage rate. This relationship between pressure, volume, and temperature is known as “PVT characteristics.”
For Example:
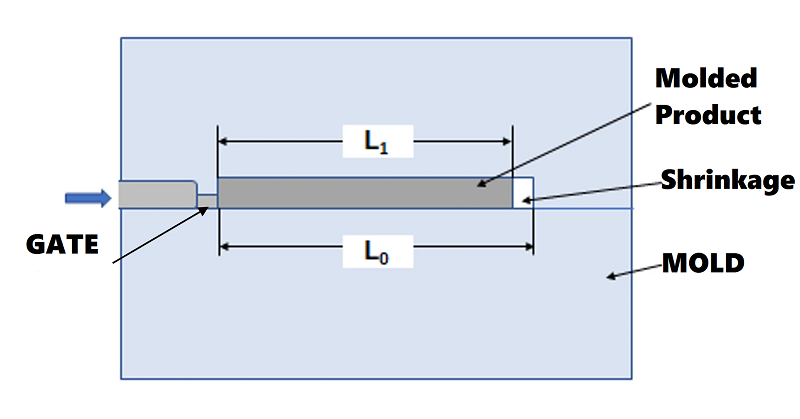
In Figure 1, if the cavity dimension of the test mold is L0 and the dimension of the molded product is L1, the molding shrinkage rate S is expressed by the following equation:
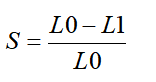
Based on the molding shrinkage rate S, to calculate the machining dimension Lm of the product mold from the specified dimension of the product Lp, the following formula derived from equation (1) is used:
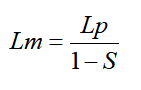
From formula (2), it is clear that errors in estimating the molding shrinkage rate S will cause errors in the machining dimension Lm. As a result, the error relative to the specified dimension Lp of the product becomes significant, and dimensional accuracy deteriorates. Therefore, it is important to accurately estimate the molding shrinkage rate to produce products with good dimensional accuracy.
Meanwhile, factors such as the melt viscosity of the material and molding conditions (molding temperature, mold temperature, holding pressure) also affect the molding shrinkage rate. The impact of each factor is shown in the table. This table distinguishes between amorphous and crystalline plastics. Crystalline plastics show different tendencies due to the volume shrinkage effect of crystallization compared to amorphous plastics.
Calculating of Molding Shrinkage Rate
Typically, the values range from 0.2% to 2%. The molding shrinkage rate is denoted by α and is defined by the following equation:
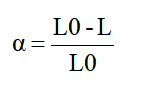
Where:
α: Molding shrinkage rate (unitless)
L0: Cavity dimension (mm)
L: Dimension of the molded product at room temperature (usually 20°C) (mm)
Additionally, considering volume shrinkage, the following expression becomes possible:
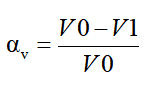
Where:
α_v: Volume shrinkage rate (unitless)
V0: Volume of the mold cavity (mm³)
V1: Volume of the molded product (mm³)
If we consider the volumes V0 and V1 as cubes, the side length L of the cube is expressed by the following equation:
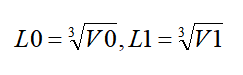
Therefore:
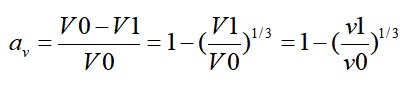
Where:
v1: Specific volume at room temperature (mm³/g)
V0: Specific volume under molding conditions (mm³/g)
Furthermore, the state equation of molten plastic is known to be expressed by the following equation:
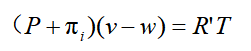
Where:
v: Specific volume of molten plastic (mm³/g)
π_i: Internal pressure (atm)
ω: Specific volume at absolute zero (mm³/g)
R: R/M (modified gas constant atm mm³/g·mol)
M: Molecular weight per unit of molecular activity
By substituting α_v = 1 – (v1/v0)^{1/3} into the above formula, we obtain:
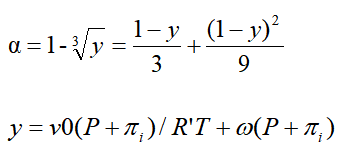
From this, it is demonstrated that the molding shrinkage rate α is significantly related to the pressure P and the temperature T of the molten plastic, as supported by the theoretical formula.
Plastics Molding Shrinkage Chart
Below, we present the molding shrinkage rates (guidelines) for major crystalline and amorphous resins (plastics). Compared to amorphous resins, crystalline resins have higher shrinkage rates, and the higher the degree of crystallinity, the higher the shrinkage rate. Additionally, changes in molding conditions can affect the shrinkage rate, leading to lower dimensional accuracy.
Note: The following values are reference values and can change due to improvements or additives. Even within the same type of resin, values may differ by manufacturer or product. For detailed values, such as MD (Machine Direction) & TD (Traverse Direction) shrinkage rates, please refer to the publicly available values from the material suppliers.
Shrinkage Rates for Crystalline Resins
Abbreviation | Resin Name | Shrinkage Rate (%) |
PP | Polypropylene | 10/1000 – 25/1000 |
EVA | Ethylene Vinyl Acetate | 7/1000 – 12/1000 |
HDPE | High-Density Polyethylene | 20/1000 – 60/1000 |
POM | Polyacetal | 20/1000 – 25/1000 |
PBT | Polybutylene Terephthalate | 15/1000 – 20/1000 |
PET | Polyethylene Terephthalate | 2/1000 – 4/1000 |
PPS | Polyphenylene Sulfide | 6/1000 – 8/1000 |
PA6 | Polyamide (Nylon 6) | 5/1000 – 15/1000 |
PA66 | Polyamide (Nylon 66) | 8/1000 – 15/1000 |
PEEK | Polyether Ether Ketone | 7/1000 – 19/1000 |
In the case of amorphous (non-crystalline) resins, although they shrink with temperature changes due to thermal expansion, crystalline resins are predominantly influenced by significant volume changes due to crystallization. Therefore, the molding shrinkage rates are high, often several percent. This crystallization is greatly influenced by the mold temperature; a high mold temperature that cools slowly increases the degree of crystallization, resulting in a greater shrinkage rate. Similarly, for thicker molded products, the shrinkage rate increases due to slower cooling. Examples of crystalline resins include PP, PE, nylon resin, POM, and PBT resin.
Shrinkage Rates for Amorphous Resins
Abbreviation | Resin Name | Shrinkage Rate (%) |
ABS | Acrylonitrile Butadiene Styrene Resin | 4/1000 – 9/1000 |
PS | Polystyrene | 4/1000 – 7/1000 |
AS | Acrylonitrile Styrene | 2/1000 – 7/1000 |
PC | Polycarbonate | 5/1000 – 7/1000 |
PVC | Polyvinyl Chloride (Rigid) | 1/1000 – 5/1000 |
PMMA | Polymethyl Methacrylate (Acrylic) | 1/1000 – 4/1000 |
The main factors are the temperature of the melted state and the temperature change up to the solidified state multiplied by the thermal expansion coefficient. Therefore, the molding shrinkage rate is relatively small, often less than 1%. Of course, mold temperature and filling conditions also have an effect, but these are smaller compared to crystalline resins. For this reason, they are suitable for molding optical lenses and precision molded products. Specific types of amorphous resins include ABS resin, polystyrene, polycarbonate, acrylic resin, vinyl chloride resin, modified PPO/PPE resin, etc.
Factors Influencing Molding Shrinkage Rate
The injection molding shrinkage rate is affected by the following factors:
Type of Molding Material
The basic shrinkage rate is determined by the type of plastic used. However, there are subtle differences between material manufacturers and material grades.
Cavity Surface Temperature
The shrinkage rate is influenced by the cavity surface temperature during molding. Generally, the higher the temperature, the greater the tendency for higher shrinkage rates.
Holding Pressure × Holding Time
The product of the height of the holding pressure after resin filling and the holding time also affects the shrinkage rate. Generally, higher holding pressures and longer holding times tend to reduce the shrinkage rate.
Thickness of the Molded Product
The shrinkage rate is also influenced by the thickness of the molded product. Thicker sections tend to shrink more.
Gate Shape
The shape and size of the gate also affect the shrinkage rate. Generally, a larger gate cross-sectional area tends to result in less shrinkage. Side gates tend to have smaller shrinkage rates compared to pinpoint gates or submarine gates.
Presence of Additives in Molding Materials
There is typically a significant difference in shrinkage rates between natural materials and those containing additives like glass fibers. Materials with glass fibers tend to have smaller shrinkage rates. The actual molding shrinkage rate for mold design is determined by comprehensively considering the above situations.
Measures Against Molding Shrinkage
The dimensions of the mold need to be larger than those of the molded product, taking into account the shrinkage rate of the resin used. The guideline for mold dimensions can be determined from the molding shrinkage rate and the dimensions of the molded product.
Method for Determining Mold Dimensions (lc)
However, in actual resin molding, the resin may shrink more or less than expected. Also, the resin injected into the mold does not necessarily shrink uniformly in the MD (Machine Direction), TD (Traverse Direction), or between the surface and the interior of the molded product. Unexpected short shots, sink marks, voids, or uneven thickness may occur due to molding conditions or mold design.
Appropriate molding conditions and mold dimensions need to be finely adjusted through repeated prototyping and dimensional measurements.
Molding Conditions
Adjustments to shrinkage rates and molding dimensions can be made by changing pressure, temperature, and cooling time to some extent, but these changes must be made within a range that does not affect the properties of the resin.
Molding Dimensions
If the solidified and shrunk molded product does not achieve the desired dimensions, the mold dimensions are modified. While it is possible to shave off metal molds to make corrections, adding material to make corrections is difficult. It is crucial to apply smaller shrinkage rates to the cavity (female mold) and larger rates to the core (male mold) of injection molding molds and adjust the dimensions by shaving the mold.