Wire EDM Machining Services – Wire EDM Parts & Electric Discharge Machining Company
Junying (CNCLATHING.COM) is a specialist that can fabricate industrial parts and custom machined parts using a wide variety of manufacturing techniques. With Wire EDM Machining Services at Junying, you can get your wire EDM parts in a much more accurate and fast way, compared to conventional machining. Our newest wire EDM machines can meet your needs of high volume while maintaining high repeatability, top quality and tight tolerance. Over the past years, we have earned a good reputation for producing custom parts with reasonable pricing and on-time delivery, and also capable of working with electrical discharge machining equipment to provide wire cut EDM parts and services for our customers. Our EDM services offer experience and excellence in all types of EDM machining, welcome to submit an inquiry online.
Why Choose Junying Wire EDM Machining Services
- Quantity flexibility. From prototypes to low/high volume production, we can meet your requirements with exact specifications.
- Quality Assurance. Our team of highly skilled workers and strict quality control and inspection will ensure the quality of the final parts.
- Strong Professionalism. Electric Discharge Machining services at Junying will maintain integrity, consistency, productivity, and economy.
- High Standard. Our purpose is to achieve perfection in wire cut EDM machining through continuous improvement and upgrading.
- Customer satisfaction. Fast turnaround, on-time delivery, high quality, competitive prices, and best service help us win high customer satisfaction.
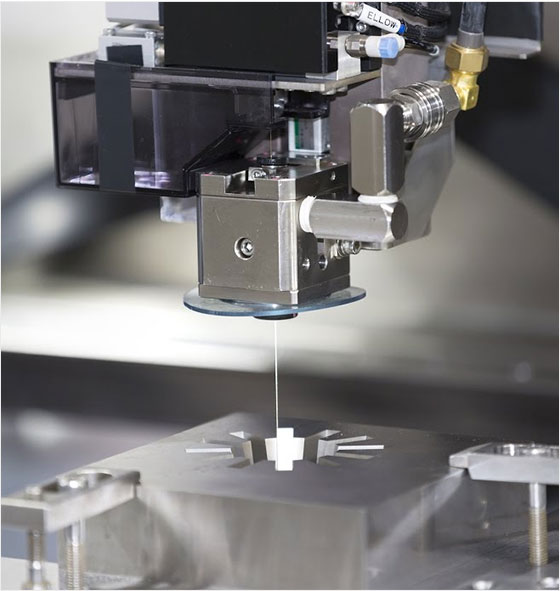
What is Wire EDM?
Electrical Discharge Machining (EDM), also known as spark machining, die sinking, and spark eroding, started with the observations of Joseph Priestley in 1770. Wire EDM process is developed based on electrical discharge machining and forming. Wire cut EDM, as the name suggests, is that the cutting tool is a thin line. The tool can turn 360 degrees at any time of cutting. As a result, it can cut machining workpieces of any shape. At present, wire EDM cutting mostly depends on the phenomenon of similar arc discharge to dissolve metal, so as to achieve the cutting effect. Therefore, wire cutting can only be used with metal or conductors. Wire EDM is used to accurately cut metal materials for high-precision machining. It is usually used to process block materials (such as molds and gears, precision fixtures) and post-treatment of hardened parts requiring high machining accuracy, rather than cutting sheet materials.
How Does Wire EDM Work?
An electrically charged wire is used in the EDM process, which is the most significant characteristic of wire cutting. Then how does it work?
- First, put the workpiece to be processed on the workbench. You can cut it from the end of the workpiece, but usually, at the beginning of wire cutting, the starting hole is usually connected to the material to avoid deformation due to the internal stress of the workpiece. When the worktable (or wire) moves in the XY direction (on the plane) according to the CNC data, machining is started.
- When the distance between the workpiece and the wire electrode in the insulating state in the working fluid is close to tens of microns, the insulation between them is damaged and spark discharge occurs, resulting in the instantaneous flow of pulse current. In a high-density discharge state called an arc tower, a local high temperature of thousands of degrees is generated and the metal melts.
- In addition, the temperature of the working fluid around the arc column immediately rises and vaporizes, causing rapid volume expansion, resulting in an explosion between the workpiece and the electrode surface. This blows out metal debris.
- Then, when the pulse current is cut off and flows into the surrounding clean water, the molten metal cools and becomes fine debris. The debris are washed away, and the insulation between the electrodes is restored again, waiting for the supply of the next pulse voltage.
- In this way, the metal is melted and removed at each voltage pulse and repeated hundreds of thousands of times per second to cut the workpiece by wire cutting EDM.
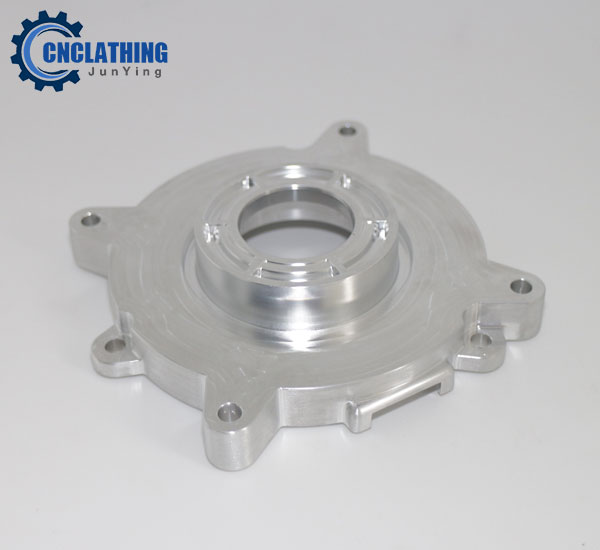
Benefits of Wire Cut EDM
- Avoid damage to small workpieces like conventional machining
- Ideal for processing delicate, hard, exotic or weak materials
- Suitable for situations requiring low levels of residual stress
- Eliminates the need for post-machining or heat treatment
- Reduces the possibility of surface distortion
- Achieve a burr-free surface and edge finish
- Minimizes unproductive downtime and fast turnaround
What Materials Can Wire EDM Cut?
The EDM wire cutting process has become a popular choice for a wide range of industries. The wire EDM can cut any conductive materials including aluminum, brass, steel, titanium, superalloys and other alloys to produce machine parts, components, logos and other metal parts easily. Typically, the electrodes for EDM cutting are made of copper or graphite.
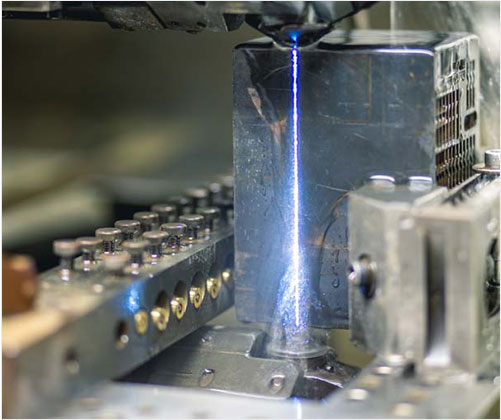