Drop forging is a manufacturing process widely used to produce powerful and durable metal parts for a variety of industries. This guide will provide an in-depth look at drop forging, including its definition, process steps, types, die design considerations, advantages over other forming methods, common applications, and differences between drop forging and press forging!
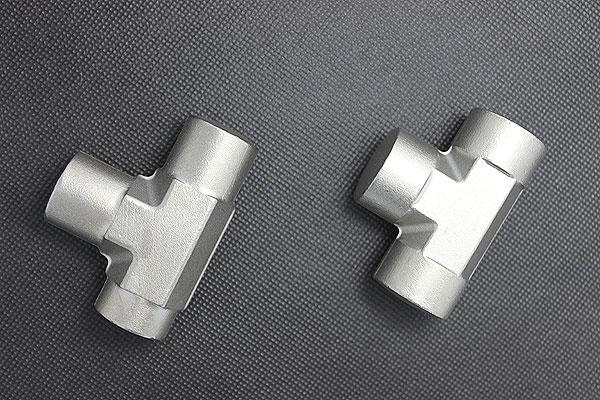
What is Drop Forging?
As defined by American Vanadium, drop forging is a “metal forming process where a hot or warm metal workpiece is placed on a die and then compressed by a powered hammer or press.” Compared to other forging methods like press forging, the drop hammer method allows higher production rates and closer tolerances.
What is the drop forging process?
Drop forging is a manufacturing process in which a heated metallic workpiece is compressed between two dies using a mechanical press or power hammer.
How does Drop Forging Work?
Here are the key steps involved in the drop forging process:
- Heating the workpiece metal – The workpiece is typically made of steel, aluminum or titanium alloy. It is first heated to its appropriate forging temperature range, usually around 1700-2000°F for steel. Heating softens the metal, making it easier to deform during forging.
- Placement in dies – The heated workpiece is then placed between the top and bottom dies of a drop forging press or hammer. The dies are precision-machined steel blocks with mirror-image cavities that will impart the desired shape.
- Forging impact – The upper die or ram rapidly descends under heavy force (500-5000 tons) and impacts the workpiece. This compresses the softened metal and squeezes it tightly into the die cavities.
- Trimming/parting – After forging, excess flashing around part lines is sheared off. Flash is the squeezed-out metal that forms where the dies meet.
- Sizing/finishing – Further operations may include sizing/trimming to final dimensions, shot peening, heat treatment and cleaning.
- Inspection and packaging – For quality control, forged parts undergo inspection checks before being packaged for shipment.
This mechanical metal flow process results in high-strength parts with complex and precise shapes. It allows dramatic thickness changes compared to other forming methods.
Drop Forging Diagram
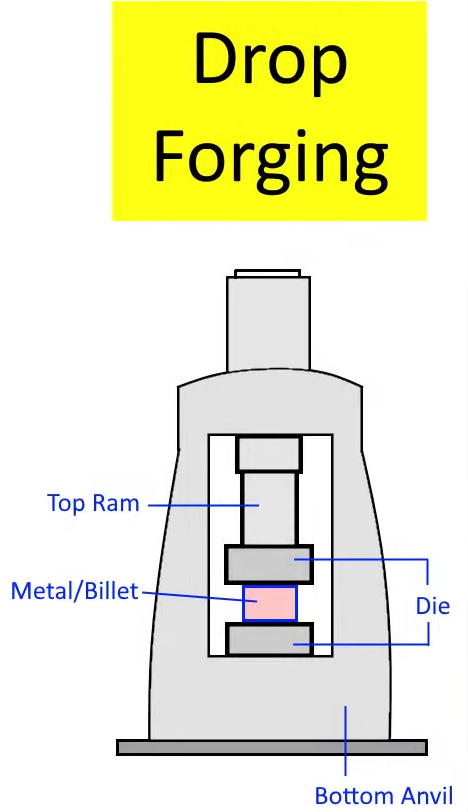
How Does Drop Forging Affect Grain Structure?
Drop forging has some important effects on the grain structure of the metal being forged:
- Refinement of grain size – The heavy compressive forces applied during forging cause the original casting grains to break up into much smaller, finer grains. This happens through a process called strain-induced grain refinement.
- Grain elongation – Under the directional strain of the forging process, the grains become elongated and aligned in the general flow pattern of the metal being formed in the dies.
- Uniform grain structure – Whereas casting can result in non-uniform grains, the multipass deformation in drop forging promotes a more consistent, uniform grain structure throughout the workpiece.
- Recovery and recrystallization – Above the metal’s recrystallization temperature, grain distortion and defects introduced during straining are recovered through atomic diffusion. New strain-free grains nucleate to form an optimized microstructure.
- Closed grain boundaries – The intense working of the metal results in tighter, better-defined grain boundaries that help improve mechanical properties like strength and ductility.
- Dislocation reduction – Plastic deformation stimulates the movement and annihilation of dislocations (crystal defects), enhancing material integrity.
- Improved properties – All these changes lead to better mechanical characteristics compared to pre-forging grain structures, such as higher yield strength, fatigue resistance, and toughness.
What Types of Drop Forging?
The main types of drop forging are:
1. Closed Die Forging:
– Uses a set of matching bottom and top dies that fully enclose the workpiece.
– Produces more accurately dimensioned parts with close tolerances.
– Allows for detailed impressions and finer surface finishes.
– More complex die manufacturing process which makes the dies expensive.
– Requires more forging steps for intricate shapes.
2. Open Die Forging:
– Top die is an open mechanical punch rather than a matching cavity.
– Bottom die acts as the primary impression surface.
– Cheaper die production than closed dies.
– Can produce basic shapes in fewer strokes compared to closed die.
– Dimensional accuracy is less and surfaces rougher than closed die forging.
3. Precision Die Forging:
– A specialized form of closed die forging for extremely close tolerance work.
– Top and bottom dies are very precisely machined and matched.
– Used for Critical applications like aerospace components needing tight tolerances.
4. Upset Forging:
– Involves compressing a workpiece along its axis, thereby enlarging one dimension.
– Commonly used to form heads on bolts, studs or pins from rod stock.
– Simple version of closed die forging process.
5. Roll Forging:
– Workpiece is shaped as it passes through a series of rolling dies.
– Produces long cylindrical parts like bars or wires in a continuous process.
What are the advantages of Drop Forging?
Here are some key advantages of drop forging:
- Strength – Drop forged parts are strong due to the grain refining and deformation that occurs during the forging process. This makes forged parts suitable for high-stress applications.
- Durability – The process aligns and binds together grains, eliminating internal defects. Forged parts maintain their strength over time and have higher fatigue life than other metal forming methods.
- Dimensional accuracy – Close clearances in drop forging dies allow for precise control over dimensions and intricate detail in parts. Tighter tolerances than casting or machining from bar stock.
- Surface finish – Smooth final surfaces require little to no secondary machining, saving time and money in post-processing. Surfaces resist wear and corrosion better.
- Complex shapes – Thin or thick sections can be consolidated under pressure into nearly any feasible contoured shape, not possible with other techniques.
- Material economy – Dies are filled completely with no waste of material. Better yield rates than fabrication from solid billets or plate stock.
- Production efficiency – Automated forging lines provide high throughput of consistent, uniform parts better than individual machining of unique geometries.
- Versatility – A wide range of metals like steel, aluminum, nickel alloys can be drop forged for all industries.
- Mechanical integrity – Isotropic strength properties result with no weak points or grain defects often found in casting and welding methods.
- Recyclability – Scrap metal flash and trim can be remelted and reused as forging feedstock.
What is Drop Forging Used to Make?
Drop forged parts are widely used in automotive, aerospace, construction, hardware etc. Here are some common examples of parts that are made using drop forging:
- Automotive components: Connecting rods, Crankshafts, Gears, Camshafts, Pistons, Flywheels, Brake components
- Hardware: Bolts, Nuts, Studs, Rings, Links, Chains, Hinges
- Tools: Hammers, Wrenches, Pliers, Sockets, Screwdrivers, Vice jaws
- Industrial equipment: Sprockets, Pulleys, Shafts, Load binders, Jacks, Press plates
- Aerospace parts: Turbine disks, Landing gears, Engine components, Propeller blades, Mounting brackets
- Appliances: Washing machine parts, Stove components, Refrigerator doors/handles
- Plumbing fixtures: Flanges, Fittings, Valves, Pipe clamps
- Firearms: Gun frames, Barrels, Trigger parts
Drop forging is used to make robust metal parts for automotive, machinery, tools, construction and many other industrial sectors.
What to Consider for Die Design for Drop Forging?
Some important factors in die design highlighted by Forsberg Technologies include draft angles, surfaces, fillets, ribs, louvers, and venting to ensure easy parting and flow of displaced metal.
Drop forging is a versatile metal forming technique capable of producing strong, complex parts in high volumes for many industries.
Drop Forging vs Press Forging vs Upset Forging, What are the Differences?
Press forging and upset forging are two other mainstream forging methods. So what are the differences between them and press forging? Let’s take a look:
Movement of Dies
In drop forging, the lower die stays fixed while the upper die moves up and down, controlled by rollers attached to a ram or connecting shaft. Press forging also uses a fixed lower die and a movable upper die, but here, the upper die is moved by a hydraulic cylinder, which uses fluid power to push the ram with high force. In upset forging, a punch impacts a cylindrical bar that is held in a die. The punch strikes the protruding end of the bar to shape it.
Application of Force
Drop forging shapes metal by repeatedly impacting the heated raw material with the upper die. This process usually takes two to four steps to achieve the required product. In contrast, press forging applies a slow, steady, and continuous force in a single squeezing action. The entire shaping is done in one go, thanks to the hydraulic system. Upset forging uses a punch to hammer the raw material, deforming it to create specific features such as bolt or nut heads.
Deformation of Material
In drop forging, most of the deformation happens at the surface layers of the metal. Press forging achieves uniform, deep, and simultaneous deformation throughout the whole part, including its center. Upset forging focuses on increasing the diameter at one end of the cylindrical bar, such as creating the head of a bolt.
Structure of Final Product
The final product from drop forging tends to have a coarse and non-homogeneous structure because of the impact-based shaping. Press forging produces dense and homogeneous parts due to the steady and deep pressure applied. Upset forging yields parts with a well-defined head or enlarged feature at one end, while the rest of the bar remains cylindrical.
Number of Steps
Drop forging requires multiple blows, usually two to four, to complete the shaping of the product. Press forging completes the operation in a single stroke, which speeds up the process. Upset forging may need several hammering impacts to fully form the desired head or feature.
Production Rate
Drop forging has a moderate production rate due to the need for repeated blows. Press forging operates faster and allows for higher production rates because the process is finished in a single step. Upset forging is efficient for producing parts like bolts and nuts where specific features need to be formed quickly.
Initial Cost
The initial cost of setting up drop forging is lower than press forging. Press forging requires a larger investment due to the hydraulic system and its components. Upset forging has a moderate setup cost, mainly depending on the complexity of the dies and punches.
Typical Applications
Drop forging is used for general metal shaping where moderate accuracy and strength are needed. Press forging is favored for high-volume, precise, and high-quality parts due to its efficiency and the quality of the output. Upset forging is mainly used to form heads on bolts, nuts, and other rod-like features.