The rapid development of the automotive, motorcycle, and machine tool industries has provided the driving force for the development of cold forging as a traditional technique. The demand for forged parts in the automotive industry alone exceeds 10 million tons. The development of cold forging technology is mainly to develop high value-added products and reduce production costs, and at the same time, it is also infiltrating or replacing cutting, powder metallurgy, casting, hot forging, and sheet metal forming processes. It can also form composite processes by combining with these processes. Since cold forging is performed at near-room temperature, some materials are most suitable for cold forging, and some that cannot be processed. This article will introduce materials that have good compatibility with cold forging and case studies solving issues related to materials.
What is Cold Forging Technology?
Cold forging refers to a forming method that shapes metal materials (metals) by applying pressure without applying heat, keeping them at room temperature. Since it utilizes the plasticity of metals, it is also called “plastic forming”.
Cold forging technology shapes materials by deforming them, so almost no metal scrap (metal waste) is generated during manufacturing. Also, since materials are processed at room temperature without heating, dimensional accuracy is good, and even complex difficult shapes can be processed at a high speed of around 100 pieces per minute.
Cold forging technology has high material utilization efficiency and enables high precision and high-speed processing, so it is said to be an “environmentally friendly and rationalized” processing technology.
Advantages of Cold Forging:
- High material utilization efficiency – With cold forging technology, which shapes materials by deforming them, the processing is generally carried out using a material quantity equivalent to the finished product weight. This allows high material utilization efficiency and a major reduction in material costs.
- High-speed production possible – Cold forging technology enables high-speed production of around 100 pieces per minute. Since processing is done at room temperature without heating the metal, dimensional variations are small, and even complex, difficult shapes can be processed.
- Improved mechanical properties – Process design considering fiber flow lines enables the production of parts with superior strength and wear resistance.
- Effective for reducing part costs – When production conditions such as required accuracy and lot size match, cold forging technology which has high material efficiency and enables high-speed processing has the potential to greatly reduce part costs in mass production.
Disadvantages of Cold Forging:
- Dies are required (initial costs and die manufacturing lead times are required)
- A certain amount of time (costs) is required for setup work in the process → Not suitable for small lots
- Know-how is required for process and die design, and the degree of difficulty is high
- Some processing limitations on finishes such as corner radii
How Does Cold Forging Work?
Cold forging is a metal shaping process conducted at room temperature, significantly below the recrystallization temperature of the metal involved. Unlike hot forging, where the metal is heated to high temperatures, cold forging involves the plastic deformation of a metal at ambient conditions. This method often results in superior surface finish, increased strength due to work hardening, and higher dimensional accuracy.
Here’s an overview of how cold forging typically works:
1. Material Selection
The first step is to select a suitable material that can withstand the stresses of cold forging, typically metals like steel, aluminum, and copper.
2. Lubrication
Prior to forging, the workpiece is often lubricated to reduce friction and wear on the die and to facilitate the flow of material.
3. Dies and Tooling
Customized dies that shape the workpiece are created. These dies must be made from materials that are harder than the workpiece to withstand the pressures of cold forging.
4. Forging Process
The metal workpiece is placed between the dies.
A press, usually a mechanical or hydraulic press, applies a rapid and forceful strike to the workpiece, causing it to deform and assume the shape of the die cavities.
Multiple forging operations might be needed, depending on the complexity of the part. This can involve various stages of pressing with different sets of dies.
5. Trimming and Finishing
Any excess material, such as flash created during the forging process, is trimmed off.
Additional finishing processes like shot blasting, cleaning, or heat treatment (for stress relief) may be applied.
Types of Cold Forging Processes
There are rotary and reciprocating types of cold forging processes, and the reciprocating type process performed by our company is introduced here. Common forging techniques include free forging, coining, extrusion, etc. Here we explain the contents and characteristics of each forging technique:
Coining forging:
A processing method that forms the material into a shape with a diameter larger than the original by crushing the material inside a die cavity that is open in the center. In coining forging, it is difficult to produce complex shapes as the outer circumference is not constrained, so it is used for simple cases such as rounding a rod into a disk shape. If the coining ratio is too large, problems such as the workpiece flying out can occur, requiring multiple steps. Generally, an 85% coining ratio or less is the guideline, and processes need to be divided if exceeded, requiring additional dies.
Backward extrusion:
A processing method that moves the material in the direction opposite to the punching direction. The material is extruded (processed) in the reverse (backward) direction relative to the punch shaping direction.
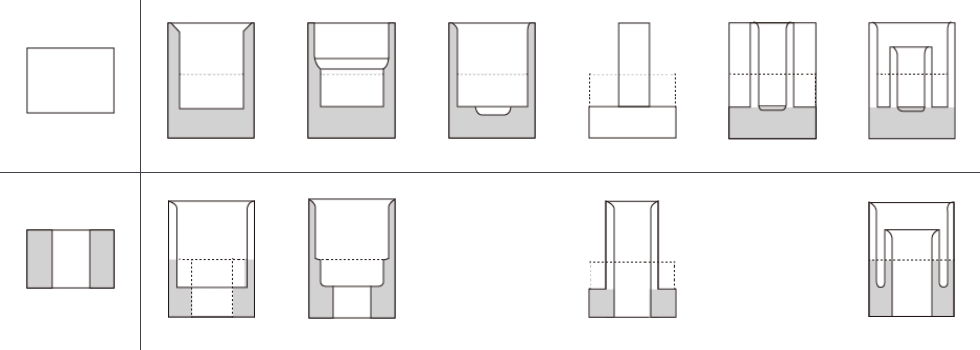
Forward extrusion:
A processing method that reduces the material diameter by pushing it into a smaller die, resulting in a reduction in cross-sectional area. Shaping high-hardness materials such as stainless steel can be difficult.
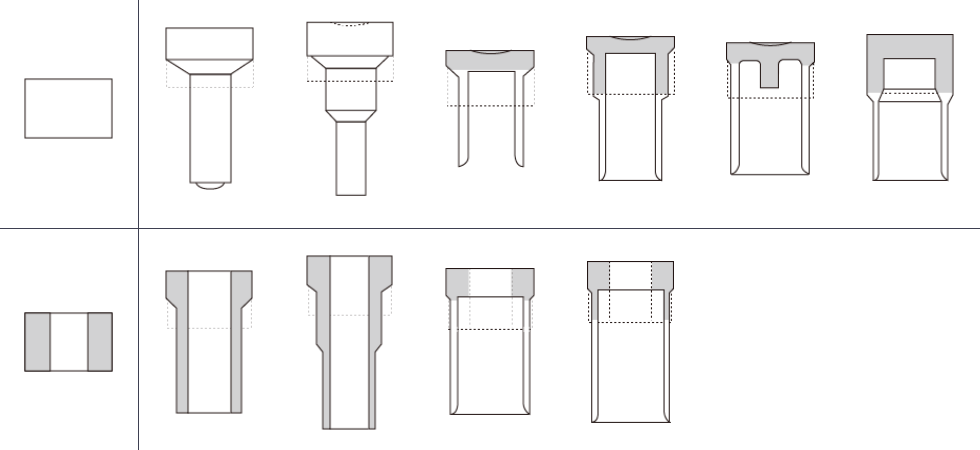
Die forging:
The desired shape is processed into the dies. Forming is done by placing the workpiece and forging it to take the die shape. The material volume is made slightly larger to fill the entire die cavity, and excess material called flash results on the outside of the finished shape, which is removed in subsequent processes. Closed die forging shapes without flash.
Closure forging:
The workpiece is set in the die cavity, which is then closed to take the die shape. The upper and lower punches further displace the material to completely form the finished shape.
What Materials are Most Suitable for Cold Forging?
Since cold forging utilizes plasticity at room or near room temperature, the material needs to have a low work hardening characteristic and some degree of deformability. Therefore, non-plastic materials such as glass are not used for cold forging.
Considering the above, materials suitable for cold forging include:
Iron: Can be processed by forging, drawing, rolling at high and room temperatures, and further diversified by heat treatments such as hardening and tempering. Also used in alloys such as stainless steel and offers high versatility. Iron is processed into various parts. The reasons iron is bent processed are not only because its hardness and elasticity have optimal values for bending processing, but also because of its low price, it is suitable for large-scale orders. Surface treatments after processing can also be done in many ways, so it can be utilized in a wide range of fields, and iron is also adopted as a material processed in cold forging.
Stainless steel: Alloy steel containing over 10.5% chromium and below 1.2% carbon. Chromium forms a passive film that protects the body surface. Therefore, products made of stainless steel have long lifetimes as corrosion is prevented.
Copper and brass: Copper has excellent thermal conductivity and is used in cookware, heat pipes, and as a conductor in electronic devices. It also forms a protective surface film when exposed to air. However, its greatest strength is excellent processability. Copper is soft and ductile. It is widely used in copper wires, tubes, and pots because processing is easy. This is one of the reasons it is suitable for bending and drawing processes through cold forging presses.
Aluminum: Though aluminum has lower tensile strength in its pure form, its strength can be increased by adding alloys like magnesium, manganese, copper, silicon, zinc, etc. or through processes like rolling or heat treatment. It is considered suitable for cold forging due to its plasticity and ability to be formed into various shapes easily.
Cold forged parts also have the characteristic of higher dimensional accuracy during forming compared to other forged parts. Furthermore, the surface condition is better than hot or warm forging, so finishing work may not be needed in some cases. Large products or high strength materials can be precisely cold forged through intermediate annealing or lubrication treatments.
What Products Does Cold Forging Used For?
Cold forging is used to produce a wide array of products across various industries. The process is particularly well-suited for high-volume production of parts that require high precision and strength. Here are some common products made through cold forging:
Automotive Components
Fasteners and Screws: These are widely used in the automotive industry and can be precisely made through cold forging.
Gears: High-precision gears for transmissions and drivetrains benefit from the improved strength due to work hardening.
Shafts: Cold forging can create strong, precise shafts for use in various automotive applications.
Wheel Hubs: Cold forged wheel hubs have the required strength and precision for the automotive industry.
Bearing Races: High precision and smooth surface finish are critical for bearing races, which can be achieved via cold forging.
Electrical and Electronics
Connectors: Electrical connectors benefit from the good conductivity and precise dimensions that cold forging can provide.
Terminals: Terminals require precise shapes and good material properties, which cold forging can achieve without additional machining.
Construction and Building Hardware
Nails and Rivets: These are simple parts that are often produced in massive quantities via cold forging.
Bolts and Nuts: The threads can be cold formed to create a stronger thread profile with better fatigue resistance.
Tools and Hardware
Wrenches and Spanners: Tools that require a specific shape and high durability are commonly made through cold forging.
Hand Tool Components: Various components of hand tools, like sockets, can be made with cold forging.
Aerospace Components
Fasteners and Pins: Aerospace-grade fasteners that must withstand high loads are often made using cold forging to ensure strength and precision.
Landing Gear Components: Some parts of the landing gear system can be cold forged to achieve the required strength and tolerances.
Consumer Goods
Watch Components: Small, precise components in watches can be made using cold forging.
Kitchenware: Items like knives or utensil handles that require a certain strength and finish can be produced through cold forging.
Medical Devices
Implants: Some medical implants can be cold forged to benefit from the material properties and precision the process offers.
Surgical Tools: Tools used in surgery that require precision and strength can be made through cold forging.
The choice of cold forging as a manufacturing process depends on the material properties required, the part geometry, and the economics of production. Due to the high strength, good surface finish, and dimensional accuracy it provides, cold forging is an attractive process for manufacturing a variety of durable and critical components across many industries.