With the continuous development of modern manufacturing technology, the demand for the lifespan and performance of mechanical components is increasing. In this context, High-Velocity Oxygen Fuel (HVOF) coating technology, as an advanced thermal spray method, successfully meets various performance requirements such as wear resistance, corrosion resistance, thermal conduction, insulation, and conductivity through flexible and adjustable flame velocity and temperature. HVOF coating, with its unique characteristics such as high flame velocity, low temperature, and high coating bond strength, provides an efficient and reliable surface protection and enhancement solution for various industries. If you are not familiar with HVOF, join us to delve into the preparation process, coating characteristics, and its extensive applications in metallurgy, paper printing, the petroleum industry, hydraulic pneumatic equipment, power systems, wire drawing equipment, and more.
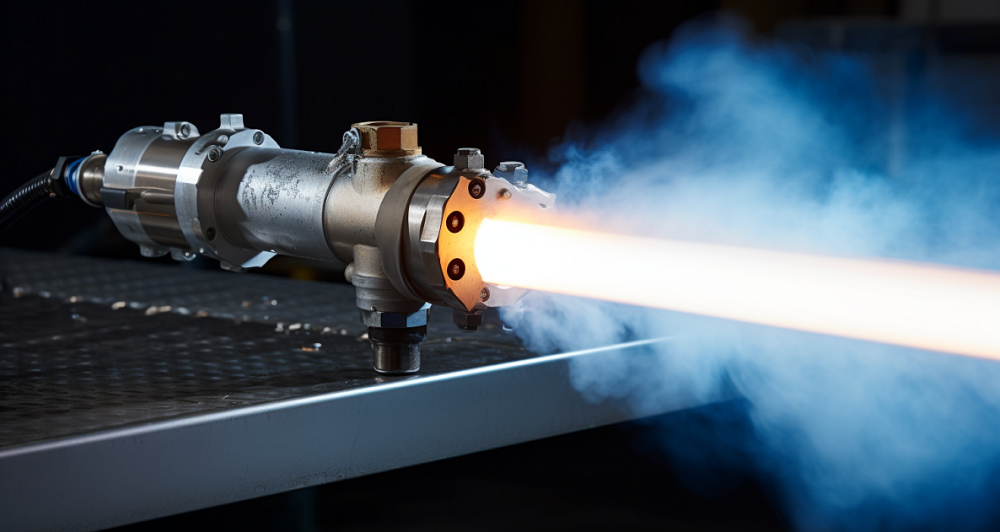
HVOF Coating Full Form – What is HVOF Coating?
HVOF coating full form – High-Velocity Oxygen Fuel coating, is an advanced thermal spray method that deposits molten or heated materials onto a surface, forming a uniform coating. Raw materials are heated through methods such as HVOF thermal spraying or combustion flames, enabling the formation of the coating. Thermal spraying can provide relatively thick coatings (ranging from 20 micrometers to several millimeters, depending on the process and materials) with a high deposition rate compared to other plating processes, making it suitable for large-area coatings. Coating materials for thermal spraying include metals, alloys, ceramics, plastics, and composite materials, supplied in the form of powder or wire. These materials, when heated to a molten or semi-solid state, are accelerated onto the substrate in the form of micrometer-sized particles. The energy source is typically combustion or electric arc discharge. The resulting coating is formed by the accumulation of a large number of ejected particles, and the surface may not significantly increase in temperature, allowing the coating of flammable materials. Coating quality is usually evaluated through parameters such as porosity, oxide content, hardness, bond strength, and surface roughness. Generally, coating quality increases with an increase in particle velocity.
What Does HVOF Stand For?
Key features of HVOF coating include extremely fast flame velocity, exceeding the speed of sound, reaching 2200 m/s, which is 5-10 times faster than typical thermal spray processes. Due to its high speed, powder particles have significant kinetic energy, forming a high-density coating with good bond strength on the substrate surface. The oxygen content in the flame of HVOF coating is lower, the temperature is moderate, and the flame velocity is extremely high, effectively preventing oxidation and decomposition of powder coating materials. Therefore, it is particularly suitable for spraying carbide coatings with excellent wear resistance. Due to fewer impurities in the spray, residual stresses designed in some cases can be achieved, allowing for thicker coatings and high spraying efficiency.
Research and evaluation of HVOF flame spray technology in the preparation of nano-tubes, oxide content, macro and micro hardness, bond strength, and surface roughness indicate that coating quality generally improves with an increase in particle velocity. This spraying method finds extensive applications in the field of wear-resistant coatings, providing high-performance surface protection and enhancement for various industrial sectors.
HVOF Coating Advantages (Features):
High-Velocity Oxygen Fuel (HVOF) is a thermal spray technology with numerous advantages. Here are the advantages of HVOF coating:
- High Flame Velocity: HVOF coating uses high-speed nozzles, and flame velocity can exceed the speed of sound, providing spray particles with high kinetic energy and impact force, contributing to the density and bond strength of the coating.
- Low Temperature: Compared to other thermal spray technologies, the flame temperature of HVOF coating is lower, reducing thermal deformation of the substrate and changes in material properties, suitable for temperature-sensitive applications.
- High Coating Bond Strength: The high-speed flame jet of HVOF coating imparts high kinetic energy to spray particles, allowing for a strong mechanical bond between the coating and the substrate, enhancing coating bond strength and durability.
- Controllable Coating Thickness: The thickness of the coating can be precisely controlled by adjusting spraying time and powder flow rate.
- Efficiency: HVOF coating can complete coatings in a shorter time than traditional methods, improving production efficiency and saving time.
- Durability: Coatings produced by HVOF spraying have high bond strength, providing a robust protective layer. The high bond strength between the coating and the substrate offers better wear, corrosion, and high-temperature resistance.
- Uniformity: HVOF technology can achieve uniform distribution of coatings, ensuring consistent thickness and quality across the entire surface. This helps improve coating performance and reliability.
- Good Coating Density: The high-speed flame jet of HVOF coating deforms and melts spray particles during the impact process, forming a dense coating structure, improving coating density and protective performance.
- Material Savings: HVOF spraying can effectively utilize coating materials, reducing waste. The high-speed ejection and melting of materials during the spraying process achieve higher material utilization.
- Handling High Melting Point Materials: HVOF spray technology can handle high melting point materials such as ceramics and metal alloys, making it widely applicable in components and equipment operating in high-temperature environments.
- Wide Material Adaptability: HVOF coating can be applied to various engineering materials, including metals, ceramics, composite materials, etc., suitable for coating requirements in different fields such as corrosion resistance, wear resistance, and repair.
HVOF Coating Disadvantages:
Despite the many advantages of HVOF thermal spraying equipment, there are some disadvantages:
- High Equipment Cost: The initial investment and maintenance costs of HVOF equipment are higher compared to other spraying technologies.
- Complex Operation: Experienced operators are required to adjust and control the spraying process.
- High Energy Consumption: Significant energy consumption occurs during the high-speed spraying process.
HVOF Coating Hardness
The High-Velocity Oxygen Fuel coatings usually range from HV1200 to 2400. The specific value is affected by the HVOF thermal spraying process and the high temperature residence time. For example, the hardness of the HVOF coating can reach HV2400+, close to the diamond level; the coating hardness under the ordinary plasma spraying process is about HV1200–1500.
HVOF Coating Process – How HVOF Thermal Spray Works?
HVOF thermal spraying is an efficient and fast coating process that can form a dense and uniform coating on the material surface in a short time. The following provides a detailed introduction to the HVOF coating process and its applications.
Step 1 – Preparation work
Before HVOF spraying, the surface of the material to be coated needs to be pretreated first. This aims to remove impurities and enhance adhesion between the coating and substrate. Commonly used surface treatment methods include grit blasting, bead blasting, and chemical treatment. In addition, preparation of the HVOF machine, nozzle, spray gun, and other equipment is needed.
Step 2 – Coating material preparation
The coating materials used for HVOF thermal spraying are usually powders mixed with a solvent. During the preparation of coating materials, the powders need to be ground, mixed, etc. to ensure uniform particle size and thorough blending with the solvent. Additives such as thickeners and leveling agents can also be added according to coating requirements and material properties.
Step 3 – HVOF spraying
Adjust spraying parameters: Adjust the parameters of the HVOF machine, such as spraying pressure, spraying distance, and spraying speed, according to the coating material properties and coating requirements to ensure uniform and stable spraying of coating materials onto the substrate surface.
Control spraying process: Pour the prepared coating materials into the spray gun of the HVOF machine and eject the coating materials at high speed onto the substrate surface through the nozzle. Stable spraying distance and speed should be maintained during the whole spraying process to ensure uniform and continuous spraying of coating materials on the substrate.
Coating formation: The sprayed coating materials instantly evaporate and cool upon contact with the substrate, forming a dense and uniform coating. Due to the high spraying velocity of HVOF thermal spraying, the coating particles have sufficient kinetic energy to effectively improve the density and adhesion of the coating.
Step 4 – Post-treatment of coating
After HVOF spraying is completed, post-treatment work is needed to further improve the performance of the coating. Common post-treatment methods include sintering, heat treatment and CNC machining to make the coating more dense and robust, improving its wear resistance, corrosion resistance and other properties.
Step 5 – Testing and Evaluation
Quality Control: Implement testing and evaluation processes to ensure the quality of the HVOF coating. Common testing methods include hardness testing, adhesion testing, porosity testing, and thickness measurement.
Quality Assurance: HVOF coating quality assurance involves confirming that the coating meets the specified requirements and standards for the intended application. This step is crucial for ensuring the reliability and performance of the coated component or surface.
HVOF Coating Types
HVOF Thermal Spray technology can produce a variety of coatings. The following are some common types of High-Velocity Oxygen Fuel catings:
- 1. WC-Co coating: WC-Co coating has excellent wear resistance and corrosion resistance, and can be used to prepare surface coatings for tools and mechanical parts.
- 2. Al2O3 coating: Al2O3 coating has excellent wear resistance, high temperature resistance and corrosion resistance, and can be used to prepare high temperature thermal insulation coatings and anti-corrosion coatings.
- 3. NiCr coating: NiCr coating has excellent heat resistance and corrosion resistance, and can be used to prepare surface coatings for components in high temperature working environments.
- 4. TiO2 coating: TiO2 coating has excellent optical properties and anti-corrosion properties and can be used to prepare surface coatings for solar panels.
HVOF Coating Machine (Parts & Price)
HVOF spraying typically requires a specialized spraying machine. This HOVF coating machine includes HVOF flame spray guns or plasma spray equipment to generate high-speed gas streams.
Key Components of HVOF Spraying Machine:
- Spray Gun: The spray gun is a crucial component that propels the coating material onto the substrate. HVOF spray guns are designed to achieve high flame velocities and precise control over the spraying process.
- Powder Feeder: The powder feeder is responsible for delivering the coating powder to the spray gun. It must ensure a consistent and controlled flow of powder to achieve uniform coatings.
- Control System: The control system monitors and adjusts various parameters of the HVOF spraying process, including pressure, temperature, and spraying distance. This ensures the desired coating thickness and quality.
- Cooling System: A cooling system is essential to prevent overheating of both the substrate and the HVOF coating equipment. It may involve water or other cooling methods.
- Gas Supply System: The gas supply system provides the necessary gases, such as oxygen and fuel, for the combustion process that generates the high-velocity flame used in the HVOF coating process.
- Automation and Robotics: In advanced HVOF coating systems, automation and robotics may be integrated to enhance precision and repeatability, especially in large-scale production environments.
HVOF Coating Machine Price:
The price of High Velocity Oxygen Fuel (HVOF) coating machines can vary widely based on several factors such as the machine’s capabilities, size, manufacturer, and the specific technology it uses. As of my last update in September 2021, prices could range from tens of thousands to several hundred thousand US dollars. For a general idea:
- Small-scale equipment suitable for laboratory use or low-volume production might cost anywhere from $30,000 to $100,000.
- Mid-range systems designed for higher volumes or more extensive industrial applications could be in the range of $100,000 to $500,000.
- High-end systems with advanced features, automation, and capacity for high-volume production might exceed $500,000.
However, prices can change over time due to advancements in technology, changes in market demand, and the economic environment. For accurate and up-to-date pricing, you would need to contact suppliers or manufacturers directly for quotations. Keep in mind that the cost of the machine is only part of the total investment; you will also need to consider installation costs, training, maintenance, and the cost of consumables and spare parts.
HVOF Coating Materials
HVOF thermal spraying can be used for coating various materials, including metals, ceramics, polymers, composite materials, etc. Coating materials are usually supplied in powder, particle, or wire form. HVOF (High Velocity Oxygen Fuel) technology can use various spraying materials to create wear-resistant, corrosion-resistant, or high-temperature coatings depending on the required coating performance and application environment of the components. The selection of these materials depends on factors such as the desired coating properties, temperatures, pressures, chemical exposures, and physical abrasion that the component will be subjected to.
In addition to the material properties, the powder particle size, flowability, and purity will also affect the spraying process and coating quality. Therefore, in practical applications, the material and coating design are usually selected according to specific requirements. Some commonly used HVOF spraying materials include:
Metal Alloys
- Cobalt alloys: Often used for wear and corrosion-resistant coatings. Cobalt-chrome alloys and cobalt-chrome-tungsten alloys are two widely used cobalt-based alloys.
- Nickel alloys: Have good corrosion and high temperature resistance, and are suitable for aerospace and energy industries.
- Iron-based alloys: Provide wear resistance at a lower cost and are suitable for some industrial applications.
Ceramic Materials
- Aluminum oxide (Al2O3): Has good wear resistance and electrical insulation properties and is often used for electrical insulation and wear-resistant coatings.
- Zirconium oxide (ZrO2): Excellent in wear and high temperature resistance, and suitable for high temperature applications.
- Tungsten carbide (WC): Usually combined with cobalt, nickel, or chromium, and has extremely high hardness and wear resistance, making it an ideal material for tooling and wear parts.
- Chromium carbide (Cr3C2): Provides wear and high temperature oxidation resistance when combined with nickel-chromium alloys.
Composite Materials
- Metal-ceramic composites: Examples include WC-Co and Cr3C2-NiCr, which are common composites that provide good wear and corrosion resistance. Metal-metal composites: Prepared by mixing two or more metal powders and used for specific wear and corrosion requirements.
Functionally Graded Materials (FGM)
- Gradient coatings: Using different materials in coatings to gradually transition properties through composition changes to achieve better combinations of performance.
Other Special Materials
- Alloying elements: Adding rare earth elements or other alloying elements can improve coating properties.
- Solid lubricating materials: Such as composites containing solid lubricants used to enhance the wear resistance of coatings.
Choosing the right spray material is critical to ensuring the performance of your coating. Engineers must consider factors such as the working environment, temperature, pressure, chemical exposure and physical wear that the workpiece will be subjected to. In addition, the particle size, flowability and purity of the powder will also affect the spraying process and the quality of the coating. Therefore, in practical applications, material selection and coating design are usually based on specific needs.
HVOF Coating Applications
HVOF thermal spray coating technology has found widespread applications in various fields, including aerospace, aviation engines, energy industry, automotive manufacturing, electronics, medical devices, and protective coatings. This technology provides crucial surface engineering solutions by preparing coatings with properties such as wear resistance, high-temperature resistance, corrosion resistance, and insulation.
Here’s a table summarizing the application of HVOF Coating in various industries:
Industry | Component | Coating Material | Benefits |
Metallurgical | Bottom rolls of continuous annealing furnaces | NiCr-Cr3C2 | High-temp oxidation resistance, thermal shock resistance, wear resistance |
Conveyor rollers | Co-based WC | Excellent wear resistance and mechanical properties | |
Paper and Printing | Calender rolls | WC | Superior wear resistance, fatigue strength |
Coating rolls | Ceramic | Improved hydrophilicity, prevents glue adhesion, longer lifespan than fluoroplastic coatings | |
Petroleum | Pump piston rods | WC | Significantly improved wear resistance and lifespan |
Valve seats and shaft components | Co-based WC | Excellent adhesion, adaptability under harsh conditions | |
Hydraulic and Pneumatic | Pump shafts, piston rods, valve cores | Various | High precision, low surface roughness, extended lifespan |
Spools of ball valves | Metal ceramic | Enhanced sealing performance and lifespan | |
Power Systems | Fans, impellers, boilers, steam turbine parts | Various | Improved wear and corrosion resistance, safety, and economic benefits |
Wire Drawing Equipment | Tower pulleys | WC | Extended lifespan through surface reinforcement |
Environmental Perspective | General application | Various | Reduction in use of hazardous materials like hexavalent chromium, aligns with environmental regulations |
Economic Perspective | General application | Various | Long-term cost savings through reduced maintenance, downtime, and replacement compared to other coatings |
As technology advances, HVOF coating equipment has seen improvements in performance and efficiency, allowing it to better serve the demands of high-performance coatings. When selecting and using HVOF coating equipment, it is essential to choose the appropriate equipment model and configuration, and optimize the thermal spray coating process parameters based on the specific application requirements to ensure the coating’s performance meets the expected results.