Vacuum plating and water plating are two distinct surface treatment technologies used across various industries. They apply different principles and techniques to achieve metal deposition on substrates. This article goes over each method’s definitions, principles, processes, advantages, disadvantages, suitable materials, and applications. Finally, a comparative analysis is presented to highlight their differences, summarized in a table, followed by guidance on choosing the appropriate coating method based on specific needs.
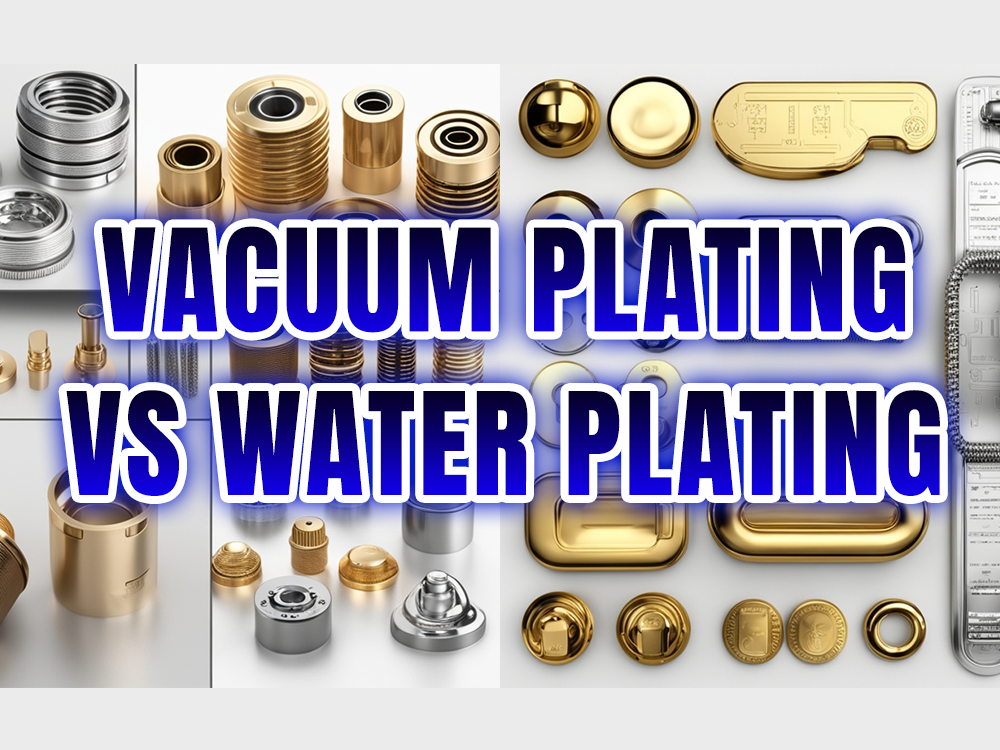
What is Vacuum Plating (Vacuum Metalizing Coating)?
Vacuum coating, also known as vacuum metalizing, involves heating materials for film formation, such as metals or metal oxides, in a vacuum to melt, evaporate, or sublime them, and then depositing the evaporated or sublimated particles (atoms or molecules) onto the surface of a substrate or base material to form a thin film.
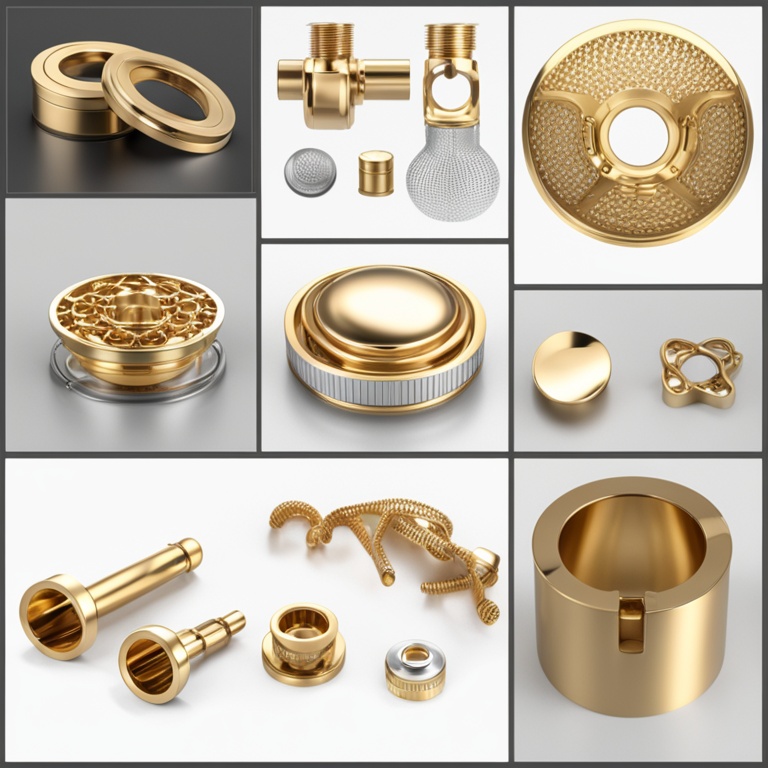
Materials for Vacuum Plating
- Metals: Al, Ag, Au, Ti, Ni, Cu, Cr, Sn, In, etc.
- Oxides: Al2O3, SiO2, etc.
Process
- Pre-treatment: Substrates are cleaned and prepared for coating.
- Base Coating: Applied to enhance adhesion and surface smoothness.
- Metal Evaporation: Metals are heated until they vaporize in a vacuum chamber.
- Deposition: The vapor condenses on the substrate, forming a thin film.
- Top Coating: Applied to protect the metal layer and enhance its properties.
- Inspection and Packaging: Quality control checks followed by packaging.
Advantages
- Can coat a variety of materials, including non-metals.
- Produces high-quality, uniform, and pure coatings.
- Environmentally friendly with no emissions.
Disadvantages
- Higher cost due to complex equipment and process.
- Limited to materials that can withstand vacuum conditions.
Types
In vacuum plating, it is necessary to evaporate the desired metal components. There are three main methods used to heat and vaporize the metal:
- Resistance Heating – Suitable for low-melting-point film materials. This method involves passing an electric current through resistors such as W (tungsten), Mo (molybdenum), or B (boron) to generate heat, and then supplying the film material to the heated resistor to heat and evaporate it, forming a thin film.
- High-Frequency Induction Heating – Also suitable for low-melting-point film materials. This method involves placing the film material inside a crucible made of materials like carbon and heating and evaporating it via high-frequency induction heating to form a thin film.
- Electron Beam Heating – Capable of handling high-melting-point film materials. The film material, stored in a refractory crucible, is heated and evaporated by irradiating it with an electron beam to form a thin film.
In all cases, the desired metal components are obtained by heating and evaporating the sample to produce metallic gas. The distinguishing feature is that each method uses different amounts of energy and mechanisms, making them suitable for different applications.
Applications
- Liquid Crystal Displays: Enhances display clarity and functionality.
- Touch Panels for Smartphones: Provides durable, conductive coatings for touch sensitivity.
- Automotive Parts: Used in windows, interiors, headlights, and internal components for aesthetics and durability.
- Food Packaging: Offers barrier protection to extend shelf life and maintain freshness.
- Cosmetic Containers: Applies decorative and protective coatings.
- CDs and DVDs: Deposits reflective layers crucial for data storage.
- Cutting Tools: Improves hardness and wear resistance.
- Building Materials: Coats architectural glass to enhance energy efficiency and appearance.
What is Water Plating (Electroless Coating)?
Water plating, commonly known as Electroless Plating or water coating. Electroless plating is a process that involves immersing a material in a plating solution without the use of electricity, allowing for a uniform metal coating on materials of any type or shape. Therefore, it is possible to plate non-conductive materials such as plastics and ceramics. Currently, electroless plating is used in a wide range of products, including automotive parts that require lightness and wear resistance, brake components that require precision, and the circuit formation of printed circuit boards and electronic components. It is an important technology that supports modern society.
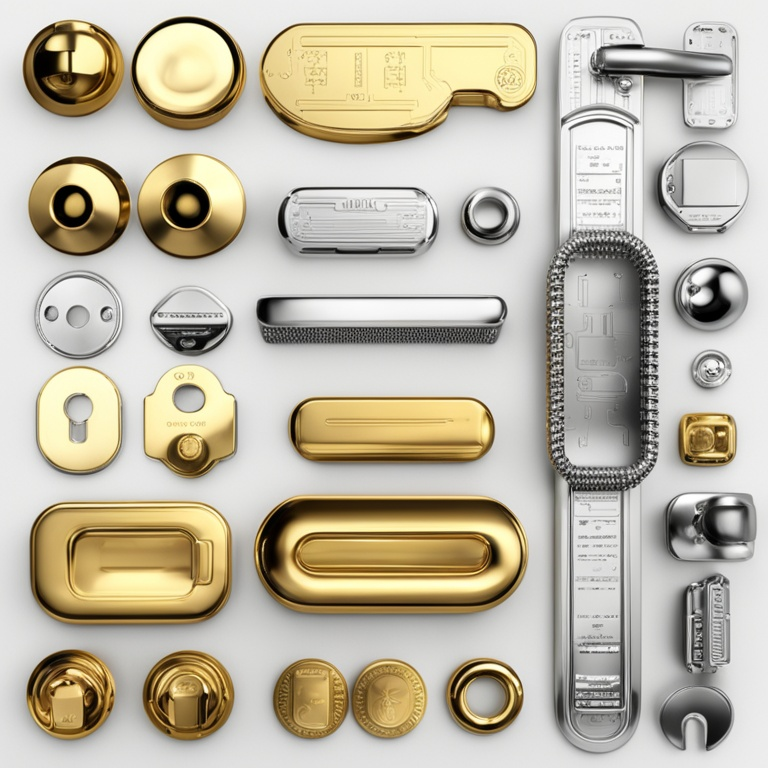
Metals for Electroless Plating
- Nickel: Often alloyed for hardness and corrosion resistance.
- Copper: Known for excellent conductivity, used in electronics.
- Silver: High conductivity and antimicrobial, used in electronics and medical devices.
- Gold: Exceptional corrosion resistance, used in high-reliability electronics.
- Palladium: Excellent corrosion resistance, used in telecommunications.
- Tin: Solderability and corrosion resistance, used in food packaging and electronics.
- Cobalt: Wear-resistant coatings, often alloyed.
Process:
- Cleaning: Removes dirt and grease from the substrate.
- Rinsing: Further cleaning to ensure no residues remain.
- Plating: Substrate is immersed in a plating bath where metal deposition occurs.
- Post-treatment: Washing and drying to finalize the coating.
- Quality Control: Ensures coating thickness and adhesion meet specifications.
Advantages:
- Cost-effective for large-scale production.
- Can produce thick coatings.
- Wide range of metals can be plated.
Disadvantages:
- Limited to conductive substrates.
- Generates waste products requiring environmental management.
Types:
If electroless plating is defined as a method of plating from an aqueous solution without the use of electricity, it can be divided into two types: displacement plating and chemical reduction plating. Within these, chemical reduction plating is further divided into non-catalytic (such as the silver mirror reaction) and autocatalytic types (such as electroless Ni-P plating):
- Displacement Plating – A representative example of a displacement reaction is the combination of copper sulfate solution and iron. When an iron plate is immersed in a dilute copper sulfate solution, a copper film forms without the use of electricity. This occurs because the iron substrate dissolves at the surface, releasing electrons that are captured by copper ions to form metallic copper. In displacement plating, the underlying iron acts as the reducing agent. The disadvantages of displacement plating include poor adhesion and limited plating thickness because the reaction stops once the substrate surface is covered with metal.
- Silver Mirror Reaction – As an example of a non-catalytic reaction, the silver mirror reaction is primarily used in glass manufacturing. In this case, since the substrate is glass, there is no release of electrons due to metal dissolution, unlike in displacement plating. Therefore, a chemical reducing agent is necessary. The silver mirror reaction involves adding sugars or formaldehyde to a silver-ammonia solution and immersing glass in the solution, where electron transfer occurs. The plating reaction is not limited to the surface of the glass being plated but occurs throughout the solution. Once the reaction in the entire solution ceases, the plating reaction also stops, thus limiting the thickness of the plating.
- Autocatalytic Type – In processes such as electroless copper plating and electroless nickel-phosphorus plating, the reaction occurs only on the surface of the parts within the plating bath. For electroless copper plating, formaldehyde in the bath acts as the reducing agent, and in electroless Ni-P plating, hypophosphite serves this role. Similar to the silver mirror reaction, these reactions are restricted to the product surface because the plated metal itself acts as a catalyst for the oxidation reaction of the reducing agent, making the plated metal itself a catalyst. This is referred to as an autocatalytic reaction. This reaction is sustainable, allowing for thicker plating over time.
Applications:
- Electronics: Enhances electrical conductivity in printed circuit boards.
- Automotive Parts: Improves wear resistance and reduces friction in engine components.
- Aerospace Components: Provides durability and corrosion resistance in hydraulic systems.
- Medical Devices: Offers biocompatibility and durability for surgical tools and implants.
- Oil and Gas: Protects machinery in corrosive environments.
- Consumer Goods: Adds durability and appearance enhancement to products like kitchen utensils and watches.
- Optical Devices: Improves reflection and abrasion resistance in lenses.
- Telecommunications: Ensures reliability and low resistance in connectors and switches.
Differences Between Vacuum Plating and Water Electroless Plating
Vacuum and Water Electroless coating methods differ significantly in their principles, material suitability, properties of the coatings, environmental impacts, applications, and costs. Here’s a detailed comparison:
- Difference in Principle
Vacuum Plating: This method involves evaporating or sublimating a coating material in a vacuum chamber, where the vapor then condenses onto the substrate. Vacuum plating primarily relies on physical processes (physical vapor deposition – PVD) without the need for chemical reactions between the substrate and the deposition material.
Water Electroless Plating: Also known as chemical deposition, this process does not require electricity. Instead, it involves immersing the substrate in a solution containing metal ions, which are chemically reduced and deposited onto the substrate’s surface uniformly, thanks to the presence of a chemical reducing agent.
- Difference in Material Suitability
Vacuum Plating: Suitable for a wide range of materials including metals, glass, ceramics, and some plastics. Its versatility stems from its ability not to require electrical conductivity of the substrate.
Water Electroless Plating: It can be applied to both conductive and non-conductive surfaces, which makes it ideal for plating on a variety of substrates including plastics, glass, and metals. This gives it an advantage in treating objects with complex shapes and sizes.
- Difference in Property of Coatings
Vacuum Plating: Produces very thin, uniform, dense, and highly adherent coatings. These coatings are generally more resistant to wear and corrosion because of their high density and purity.
Water Electroless Plating: The coatings are uniform and can cover complex geometries uniformly. However, they may not be as dense as vacuum-plated coatings. The properties of the coating (such as hardness and corrosion resistance) can vary significantly depending on the specific chemicals and process conditions used.
- Difference in Environmental Impact
Vacuum Plating: Generally considered more environmentally friendly, as it does not typically involve hazardous chemicals and produces minimal waste. The process is contained, reducing the risk of environmental contamination.
Water Electroless Plating: Involves chemicals that can be hazardous if not managed properly, requiring careful handling and disposal. The process generates waste that must be treated, posing a potential environmental hazard.
- Difference in Application
Vacuum Plating: Often used in applications requiring high precision and quality of the coating, such as electronics (e.g., semiconductor devices, display panels), automotive parts, and decorative finishes.
Water Electroless Plating: Commonly used for engineering applications where uniform coating thickness and excellent adhesion are required. It is ideal for plating non-conductive materials used in electronics, such as circuit boards, or for applications like aerospace components and medical devices.
- Difference in Cost
Vacuum Plating: Tends to be more expensive due to the high cost of the equipment and the energy required to maintain a vacuum. The initial setup and maintenance costs are significant, making it less cost-effective for small-scale applications.
Water Electroless Plating: Generally more cost-effective, especially for large batches and complex parts. The chemicals used can be expensive, but the overall process cost is usually lower than that of vacuum plating.
Feature | Vacuum Coating | Water Electroless Coating |
Basic Principle | Uses vacuum conditions to deposit thin films of material onto substrates. | Relies on an autocatalytic chemical reaction in an aqueous solution to deposit a coating. |
Process Environment | Operates in a vacuum chamber at low pressures. | Operates at atmospheric pressure in a water-based solution. |
Energy Requirements | High energy consumption due to the need for vacuum pumps and sometimes high temperatures. | Relatively low energy consumption as it usually occurs at room or slightly elevated temperatures. |
Material Types | Metals, alloys, ceramics, and some polymers can be deposited. | Primarily metals and alloys; limited to materials that can catalyze the chemical reaction. |
Thickness Control | High precision in thickness control. | Less precise, thickness depends on duration of immersion and solution stability. |
Application Examples | Microelectronics, optical coatings, barrier films, and reflective coatings. | Corrosion resistance, electronics (PCB plating), automotive parts. |
Cost | Generally higher due to complex machinery and maintenance of vacuum systems. | Generally lower, simpler setup and operation. |
Uniformity | Excellent uniformity across complex shapes and sizes. | Good uniformity, but can be challenging over complex geometries. |
Adhesion | Good adhesion, but surface preparation is crucial. | Excellent adhesion due to chemical bonding at the surface. |
Environmental Impact | Potentially high due to energy use and materials used in vacuum generation. | Lower impact, uses water-based solutions but chemical disposal must be managed. |
Vacuum Coating vs Water Electroplating Coating, Which One Is Better To Choose?
Choosing between vacuum coating and water plating depends on several factors:
- Material Requirements: Vacuum coating is versatile across various materials, while water plating is restricted to conductive substrates.
- Production Scale: Water plating is more cost-effective for large volumes.
- Environmental Concerns: Vacuum coating is preferable for stricter environmental regulations.
- Quality Needs: Vacuum coating generally provides superior quality and uniformity.
- Application scope: Vacuum plating has a wider application scope and can process various substrates, while water plating is mainly applicable to metal substrates.
- Cost: Water plating has a relatively lower cost and is suitable for mass production, while vacuum plating is more costly and suitable for small batch and high-end products.
- Environmental protection: Vacuum plating is relatively more eco-friendly without wastewater and gas emissions, while water plating requires wastewater treatment.
Choosing between vacuum plating and water electroless plating depends on the specific requirements of the application, including the type of substrate, desired properties of the coating, environmental considerations, and cost constraints. Vacuum plating offers superior quality and environmental benefits but at a higher cost, making it suitable for high-value, precision applications. Water electroless plating, on the other hand, provides excellent coverage and adhesion on a variety of materials, including non-conductives, making it ideal for complex industrial components and mass production.