Drills undergo changes in machining characteristics due to various elements such as tip angle, flute spacing, and more. This CNC guide introduces the overview of drill tip angles and helix angles, as well as drill components.
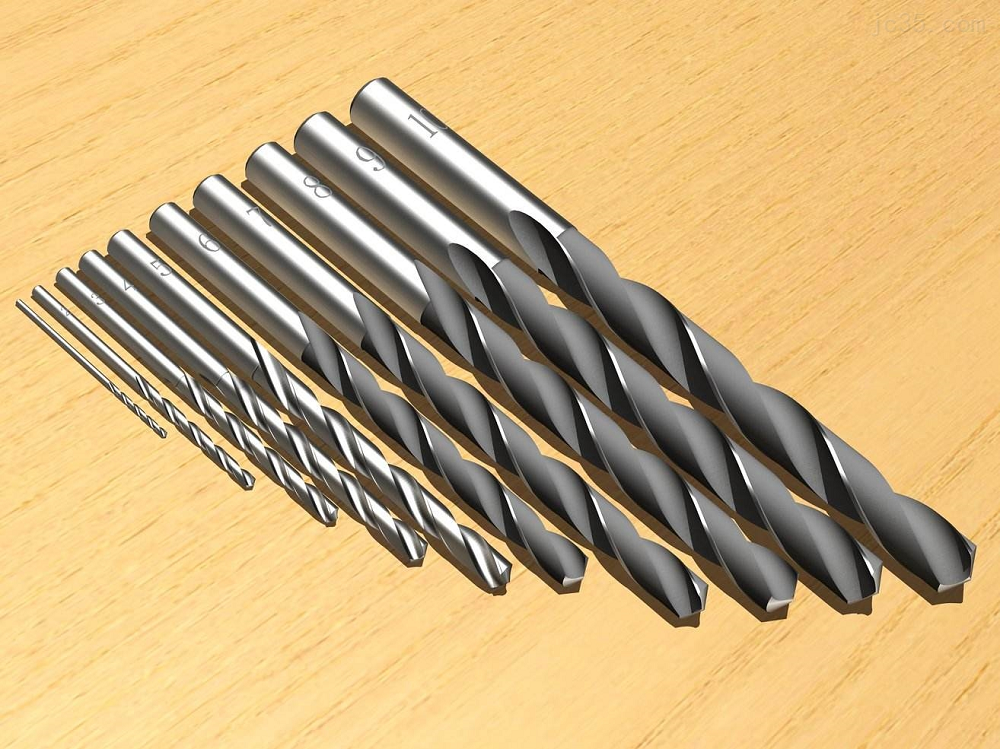
What is Drill Tip Angle?
As the name suggests, the angle at the tip of a drill is known as the tip angle. The most common is the 118-degree angle, but there are drills with various angles such as 90 degrees and 140 degrees, depending on the application.
So, what role does the drill’s tip angle play? We will introduce the functions of the drill’s tip angle and provide examples of common tip angles.
– Function of the Tip Angle
The tip angle is one of the factors that affect cutting resistance and cutting depth. A larger tip angle tends to result in shorter chips, leading to better chip evacuation. Conversely, a smaller tip angle creates thinner chips that are more likely to wrap around the drill, causing chip clogging.
Generally, a larger tip angle improves machining efficiency, tool life, and reduces burrs at the exit of the hole. However, it’s important to note that a larger tip angle isn’t always better.
For instance, as the tip angle increases, thrust resistance (cutting resistance in the opposite direction of movement) also increases. This means that drills with smaller tip angles have better bite into the work material. While a smaller tip angle enhances sharpness, it can make the cutting edge brittle, which is why it’s mostly used for softer materials.
As such, the optimal tip angle varies depending on the work material and drill material. It’s crucial to choose the right tip angle based on the application.
– Examples of Common Tip Angles
Standard drills typically have a tip angle set at 118 degrees. For center drills where the hole angle is important, sharper tip angles like 60 degrees or 90 degrees are also common. This is because a sharper tip angle enhances the drill’s bite into the work material.
On the other hand, drills made of carbide alloys have the drawback of low toughness and susceptibility to chipping. To enhance the cutting edge’s strength, there are many products with larger tip angles, such as 130 degrees or 140 degrees.
What is Drill Helix Angle?
The helix angle of a drill refers to the angle at which the cutting edge is tilted when the drill’s axis is considered as 0 degrees. The helix angle and the rake angle are equal at the outer periphery of the drill.
An angle of approximately 30 degrees is common for the helix angle, where angles smaller than 30 degrees are termed “weak helix,” and angles larger than 30 degrees are known as “strong helix.”
When the helix angle is small, chip evacuation improves, but cutting resistance increases. Conversely, with a larger helix angle, cutting resistance decreases, but the cutting edge becomes sharper, leading to a higher risk of chipping and damage.
Drill Components Beyond Helix and Tip Angles
Drills are composed of various elements aside from helix and tip angles. The following are some of the drill components:
– Rake Angle
The rake angle represents the inclination of the cutting edge with respect to the drill’s axis. It signifies the angle of the “rake face,” which has the role of ejecting the cut chips. At the outer periphery of the drill, the rake angle is the same as the helix angle.
– Relief Angle
Cutting tools have a “relief face” to prevent contact between the work material and the cutting edge. The relief angle refers to the angle between the work material and the relief face. It is designed to avoid friction between the work material and the drill and to ensure smooth feed motion. The typical range is around 7 to 15 degrees. Increasing the relief angle reduces cutting resistance but increases the risk of chipping and damage due to a sharper cutting edge.
– Lead
The lead refers to the length traveled by the drill along the flutes in one full rotation. A larger helix angle results in a smaller lead.
– Margin
The margin is the part that extends along the flutes of the drill’s outer periphery with a consistent width. The drill diameter is determined by the margin. During drilling, the margin acts as a guide along the periphery and also affects hole accuracy.
– Chisel Edge
This is the blunt angle formed at the drill’s tip. Since there is no cutting edge at this part, it cannot progress through the work material. To prevent it from crushing the work material and generating significant resistance during machining, a groove known as “thinning” is commonly added.