– Basic purpose: The positive angle displays the inclination of the tool rake face relative to the reference plane. Since the front corner is the surface of the chip flow, it also indicates the direction of chip flow. On the other hand, the back angle reflects the inclination of the cutting speed vector to the back face of the machining tool. This angle has no direct impact on chip flow. However, both angles can be measured on different planes to obtain a clear curve about the inclination of the corresponding surface.
– Values of these angles: The cutting tool has a positive angle, a negative angle, or a zero rake angle, each of which has a special significance and advantage for processing performance. For example, a negative angle provides a sharp edge, so cutting will proceed smoothly and require minimal effort. Another method is to provide a stronger tool tip at the back corner of the tool, so that the machine tool can resist higher cutting forces. However, the positive angle of the tool cannot be negative, or even zero, because in this case, the side of the machine tool will rub against the surface of the finished product.
– The mechanism of cutting and the role of rake angle: The positive angle directly or indirectly affects many factors, including shear strain, cutting force, machining torque or thrust, power consumption, chip type and color, etc. In fact, it is an important parameter in the entire mechanical processing mechanics.
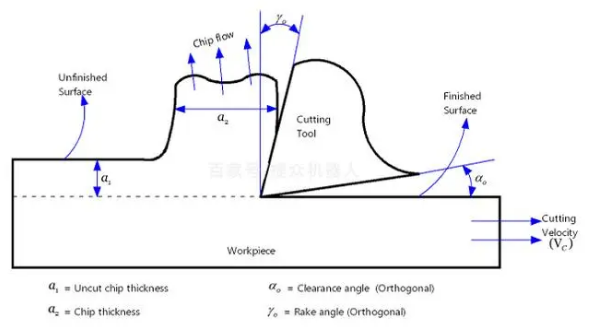
In addition to the positive angle and negative angles, other geometric shapes of the tool are also very important, such as the inclination angle, main deflection angle, main rear angle, main front angle, and so on. The size and shape of these angles can affect the performance of cutting forces, chip morphology, machining surface quality, tool life, and other aspects. Therefore, when selecting a tool, it is necessary to comprehensively consider these geometric parameters in order to achieve the best machining effect and quality.