Face mills, shell mills, and end mills are all types of milling cutters, but they have different designs and are used for distinct machining operations. Understanding the differences between them will help you choose the right tool for your specific application.
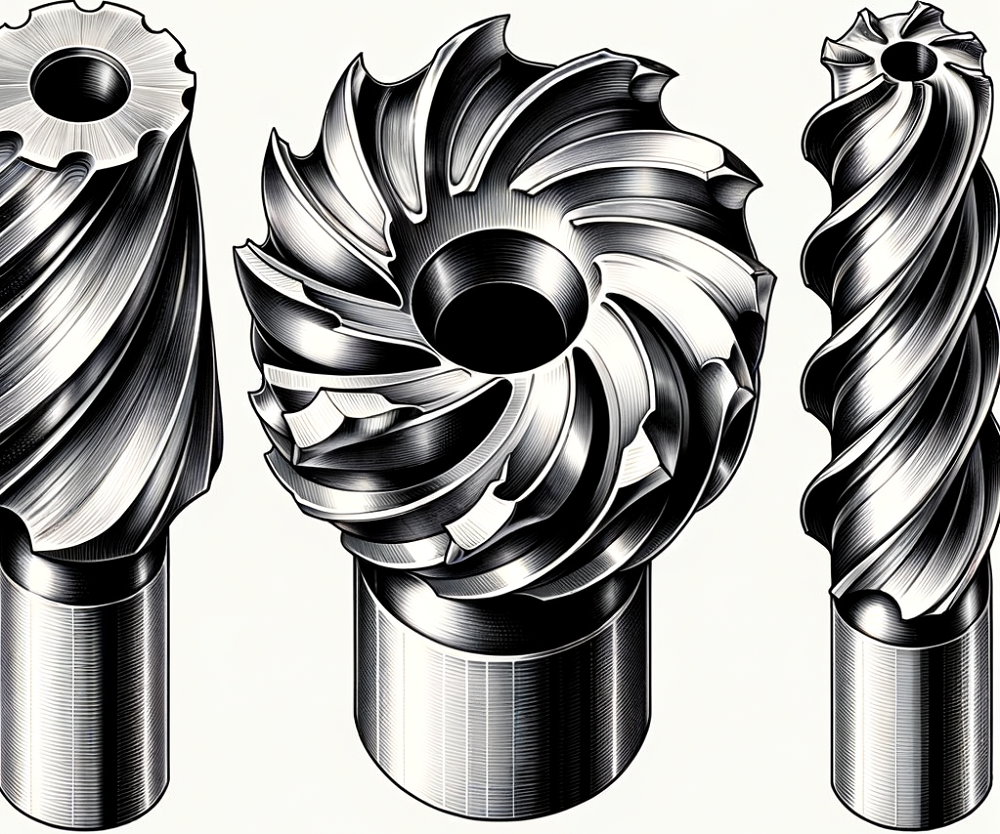
Face Mill Cutters – The Essential Milling Tool for Flat Surfaces
Face milling is one of the most common metal cutting operations and face mill cutters are the most essential tools for the job. Face mills are used to machine large flat surfaces with a single pass but require an understanding of their key features to get the best performance.
What is a Face Mill Cutter?
A face mill cutter consists of a round body that holds removable indexable inserts that do the cutting. The inserts are arranged radially around the cutter body and cut on their round periphery. This allows the entire diameter of the cutter to be used for milling, maximizing the cutting width in a single pass. Face mills come in a range of diameters from as small as 1″ cutters used for milling slots, up to huge 8-10″ diameter cutters used for surfacing large plates and flats. Axial rake angles can be positive, neutral, or slightly negative to optimize shearing action based on workpiece material.
When Use Face Mill?
A Face Mill is commonly used in the following situations:
Creating Flat Surfaces: Face mills are ideal when you need to create a large, flat surface on a workpiece.
High-Speed Machining: Face mills can handle high feed rates, improving productivity when a lot of material needs to be removed quickly.
Finishing Operations: They are often used for providing a smooth finish on the surface of the workpiece due to their design and the number of cutting edges.
Versatility: Face mills can be used on a variety of materials, including steel, aluminum, and other metals, as well as non-metallic materials.
How To Use Face Mill?
Here’s a brief guide on how to use a face mill:
Choose the Right Face Mill: Ensure that the face mill is suitable for the material you’re working with and is of the correct size for your milling machine and your workpiece.
Mount the Face Mill: Attach the face mill to the machine’s spindle. Make sure it’s secured tightly.
Set Parameters: Set your machine’s speed, feed, and depth of cut according to the material you’re working with and the manufacturer’s recommendations.
Machining Process: Start the machine and slowly feed the workpiece into the face mill, ensuring you’re milling in the correct direction.
Monitor: Regularly check the milling process for any signs of excessive wear or other issues.
Maintenance: After use, inspect and clean the face mill. Replace any worn inserts as needed.
Face Mill Advantages
Full Cutting Width: The primary advantage of face mills is their ability to mill a full width surface in one pass. This maximizes productivity for surfacing operations.
Repeatable Accuracy: The radial inserts on a face mill are accurately located to prevent stepped surfaces. This results in a highly repeatable finish.
Easy Indexing: The replaceable inserts on face mills make it simple to index to fresh cutting edges once worn. This facilitates quick insert changes right on the machine.
Shearing Action: With proper selection of rake angles, face mills can induce shearing rather than rubbing/plowing of the material for lower cutting forces.
Elements of Face Mill Selection
Diameter: Larger diameters allow wider cutting in a single pass. Smaller cutters are used for milling slots.
Insert Style: Square inserts are the most common. Round inserts may offer more cutting edges.
Number of Teeth: More teeth spread the load for a better finish but lower feed rates.
Insert Grade: Harder grades like CBN handle high temps/hard materials. Coated carbides work for most applications.
Helix Angle: Lower helix angles offer stronger ramping but more vibration. Higher angles give a smoother cut.
Shell Mill Cutters – The Multi-Purpose Milling Tool
Shell mill cutters, also known as shell end mills or cup mills, are a versatile type of milling cutter used extensively in manufacturing. This multi-purpose tool is designed to perform a variety of milling operations including face milling, slotting, grooving, and shoulder milling.
What is a Shell Mill Cutter?
A shell mill cutter consists of a cylindrical body with cutting teeth arranged around the circumference of one end. The cutting edges are on the outside diameter of the cutter which allows it to cut on the sides as well as the bottom of the workpiece. The body of the shell mill is hollow inside, giving it the cup-like shape that provides it with the name “shell mill”.
Shell mill cutters come in a range of diameters from very small to extra large sizes over 10″ in diameter. The length of the cutter is typically 1-3 times the diameter. Flutes or grooves run the length of the cutter to allow chips to escape and permit cutting fluid to reach the cutting edges. Shell mills with more flutes generally provide a better finish on the workpiece.
When Use Shell Mill?
A Shell Mill is often used in the following situations:
Large Surface Milling: Shell mills have larger diameters, making them ideal for milling large surface areas quickly.
High Productivity: Their design allows for more inserts and higher feed rates, improving productivity.
Versatility: The tooling can be easily changed, making shell mills versatile for different materials and finishes.
Better Surface Finish: The increased number of cutting edges often leads to a smoother finished surface.
Cost-Effectiveness: Despite higher initial costs, the ability to replace individual inserts rather than the entire tool can save costs in the long run.
How To Use Shell Mill?
Here’s a brief guide on how to use a shell mill:
Choosing the Right Shell Mill: Ensure the shell mill is suitable for the material you’re working with and is of the right size for your milling machine and workpiece.
Mount the Shell Mill: Attach the shell mill to the machine’s arbor. Make sure it’s secured tightly.
Set Parameters: Set your machine’s speed, feed, and depth of cut according to your material and the manufacturer’s recommendations.
Machining Process: Start the machine and slowly feed the workpiece into the shell mill. Always ensure you’re milling in the correct direction.
Monitor: Regularly check the milling process for any signs of excessive wear or other issues.
Maintenance: After use, inspect and clean the shell mill. Replace any worn inserts as needed.
Shell Mill Advantages
Versatility – Shell mills can perform almost any type of peripheral or slot milling operations. Their flexibility allows one tool to mill flat surfaces, shoulders, slots, and profiles. This can reduce the number of tools required in the shop.
Material Removal Rate – The large cutting surface of shell mills means they can remove material faster than end mills. Their high metal removal rates make them well-suited for roughing cuts and heavy machining applications.
Stable Cutting – The broad cutting edges and rigidity of shell mill bodies provides stable cutting, even with deep axial depths of cut. Shell mills can take heavier cuts without deflection or chatter.
Chip Control – The flutes in shell mill cutters provide efficient chip evacuation even when milling deep cavities or pockets. This allows them to mill cleaner with less chance of chip recutting.
Disadvanatages of Shell Mill:
Limited Application: Like face mills, shell mills are primarily used for face milling and may not be suitable for detailed or complex milling operations.
Cost: Shell mills can also have a higher initial cost due to their size and complexity.
Requires Arbor: Shell mills require an arbor for mounting, which adds to the overall cost and setup time.
Shell Mill Cutter Applications
Face Milling – The primary application of shell mills. The cutting edges on the outside diameter allow full face width milling in one pass.
Shoulder and Slot Milling – The side cutting edges make shell mills effective at milling shoulders and slots.
Contouring – Shell mills can be used to mill convex and concave contours using the outside diameter of the cutter.
Pocketing – When programmed with an appropriate tool path, shell mills are excellent for pocket milling square or irregular shaped pockets.
Elements of Shell Mill Tool Selection
Cutter Material – Carbide shell mills offer the best wear resistance for most materials. High speed steel can also be used but is limited to lower hardness materials.
Number of Teeth – More teeth will provide a finer finish but lower feed rates. 4-6 teeth is common for roughing while 7+ teeth are used for semi-finishing/finishing.
Helix Angle – A lower helix angle (15-30 degrees) is recommended for difficult to machine materials and interrupted cuts. Higher helix angles (35-45 degrees) perform better in general milling of steel and aluminum.
Flute Count – Shell mills with more flutes allow higher feed rates but sacrifice space for chip evacuation. 4-5 flutes is most common.
Inserts vs Solid Carbide – Inserted tooth cutters allow indexing of the replaceable cutting inserts. Solid carbide tools require grinding/sharpening when worn.
End Mill Cutters – The Original Milling Tool
Long before complex CNC machining centers existed, the end mill enabled the milling of slots, pockets, and contours in manual machines. Today, it remains one of the most common milling cutters used in a machine shop. Let’s examine the key elements of this essential cutting tool.
What is an End Mill Cutter?
End mills have cutting teeth on the end as well as the periphery of the cutter. The end cutting edges allow end mills to mill axially while the peripheral edges mill the sides. End mills are designed to cut in the direction of rotation, so feeding laterally creates a shearing action.
End mills come in a range of lengths, diameters, helix angles, number of flutes, coatings, and geometries optimized for specific applications. They may be center cutting or non-center cutting, allowing plunging axially into a workpiece.
When Use End Mill?
An End Mill is commonly used in the following situations:
Making Detailed Cuts: End mills are ideal for making detailed cuts, slots, and complex shapes in a workpiece.
Drilling and Bore Making: End mills are often used for drilling and creating bores in a workpiece.
Profiling: They are used in creating the profile of a workpiece, including contours and other complex shapes.
Finishing Operations: End mills can also be used for finishing operations, providing a final shape and smooth finish to a workpiece.
Versatility: End mills can be used on a variety of materials, including metal, wood, and plastic, making them highly versatile tools.
How To Use End Mill?
Here’s a brief guide on how to use an end mill:
Choose the Right End Mill: Select the appropriate end mill for your material and the type of cut you want to make. Consider factors like the number of flutes, the material of the end mill, and the shape of its tip.
Mount the End Mill: Insert the end mill into the spindle of your milling machine and ensure it’s secured tightly.
Set Parameters: Set the speed, feed, and depth of cut on your machine, based on the material you’re working with and the manufacturer’s recommendations.
Machining Process: Start the machine and slowly feed the workpiece into the end mill or move the end mill into the workpiece, depending on your machine setup.
Monitor the Process: Regularly check the milling process for signs of excessive wear, heat, or other issues.
Maintenance: After use, inspect the end mill for wear or damage, and clean it properly.
End Mill Advantages
Versatility: End mills can perform almost any milling operation: slots, shoulders, profiles, grooves, pockets, drilling, and chamfering. Their flexibility minimizes tool changes.
Shearing Action: The peripheral teeth cut with a true shearing action for clean, chatter-free cuts, especially in aluminum. Axial forces are minimized.
Speed/Feed Capability: The rigidity of most end mills allows relatively high feed rates, especially in smaller diameters. This boosts material removal rates.
Available Options: With carbide, high-speed steel (HSS), variable helix, variable pitch, and coated styles, there is an end mill for every application.
End Mill Applications
Slot/Pocket Milling: The most common application is milling square or rectangular slots and pockets with a full 180 degree shoulder.
Contouring Profiles: Programming end mills along irregular profiles creates clean contours with no hand-blending required.
Plunging: Center cutting end mills can axially plunge into parts like drills for slots, holes, and profiles.
Chamfering: An angled end mill is used to add a 45 degree chamfer to part edges in a single pass.
Key Elements of End Mill Selection
Diameter: Larger diameters offer higher material removal rates but may deflect in slim parts. Smaller tools resist deflection.
Length: Longer end mills allow you to reach deep pockets in a single pass while minimizing runout.
Helix Angle: High helix angles (45-60 degrees) are good for aluminum while lower helix angles (30 degrees) work better for steels.
Coating: TiCN, AlCrN, diamond coatings all enhance tool life and heat resistance. Uncoated carbide is sufficient for non-ferrous materials.
Differences Between Face Mill vs Shell Mill vs End Mill
Each milling cutter has its own specific design, paramater, and application. Here is a table comparing face mill, shell mill, and end mill:
Cutter Type | Face Mill | Shell Mill | End Mill |
Construction | Flat insert pockets around circumference for cutting inserts | Hollow shape (like a cup) with interior cutting inserts | Solid cylindrical shape with cutting edges on end face and periphery |
Cutting Action | Cuts entire face/end of workpiece simultaneously | Cuts interior cavities and contours | Plunges to cut perpendicular surfaces and contours work |
Applications | Facing, squaring ends, flat surfaces | Int. contours, cavities, slots, gears, dies | Profiling, slotting, pocketing, drilling, tapping, contouring |
Size Range | Varies widely, common 1-24″ | Varies, common under 1-12″ | Varies widely, common 1/16-4″ |
Cutting Area | Full face | Interior cavities | End face and sides |
Benefits | Fast stock removal for facing | Can machine complex interiors | Versatile for 2D and 3D work |
Limitations | Only faces one side at a time | Requires specific tool access | Less material removal vs face/shell mills |
Tool Paths | Conventional/climb for face cut | May need climb/peck for chip ejection | Conventional/climb for profiling |
Description | Circular cutter with inserts on face | Cylindrical cutter with inserts on periphery and face | Cutter with cutting edges on end and periphery |
Insert Types | Square, round, triangular inserts | Primarily square inserts | No inserts, solid carbide |
Typical Operations | Facing, surface milling | Peripheral milling, facing, slotting | Slotting, side & face milling |
Chip Flow | Chips curl over top of cutter | Radial chip flow off sides | Chips flow up flutes |
Number of Teeth | 4 – 10 inserts | 2 – 20 inserts | 2 – 12 flutes |
Rigidity | Medium | High | Low |
Typical Diameters | 3″ – 8″ | 0.5″ – 4″ | 0.5″ – 2″ |
Coolant | Requires flood coolant | Requires flood coolant | Can run dry or minimal coolant |
Insert Placement | Evenly spaced | Arranged in patterns | At cutting edges |
Surface Finish | Very smooth | Good, may have witness | Depends on parameters |
Chip Ejection | Uniform flow | May need pecking | Efficient flute flow |
Tool Rigidity | Stiff body needed | Stiff body needed | More flexibility OK |
Material Removal | Highest | High | Varies, often less |
Machining Envelope | Planar only | Cavities/pockets | Any 3D shape |
Face Mill vs Shell Mill vs End Mill, Which One To Choose?
The choice between a face mill, shell mill, or end mill depends on the specific machining requirements and the type of operation you need to perform. Here are some general guidelines to consider:
Face Mill: Choose a face mill when you need to perform facing operations on large flat surfaces. Face mills are designed for high-speed material removal and are efficient for squaring up workpieces and creating smooth finishes. They are commonly used for tasks such as facing milling machine tables, squaring blocks, or creating large flat surfaces.
Shell Mill: Opt for a shell mill when you require versatility for both face milling and peripheral milling operations. Shell mills have cutting edges on the periphery and the end face, allowing them to perform a range of tasks, including facing, slotting, and contouring. They are suitable for machining large surfaces, slots, and contours. Shell mills are available in various sizes and can be used with different types of inserts or solid carbide cutters.
End Mill: Select an end mill when you need a versatile cutter for various milling operations. End mills are small, solid cutters with cutting edges on the periphery and end face. They are suitable for tasks such as slotting, profiling, contouring, and plunging. End mills come in different shapes (square, ball nose, corner radius) and coatings to suit different machining needs. They are commonly used in both roughing and finishing operations.
Which one to choose:
The choice between these tools depends on your specific needs and the type of machining operation:
If you need to make a large flat surface or finish a surface, a face mill or shell mill would be a good choice. The choice between these two depends on the size of the surface (go for shell mill for larger surfaces) and the flexibility you need with tooling (shell mill offers more flexibility).
If you need to make detailed cuts, pockets, shoulders, complex contours or shapes, an end mill would be the better choice.