In the context of machining, alongside machining equipment and cutting tools, cutting oil (coolant fluid) plays a crucial role. In this post, we will introduce the characteristics of various types of cutting oils, the effects of their usage, and points to be mindful of when using them.
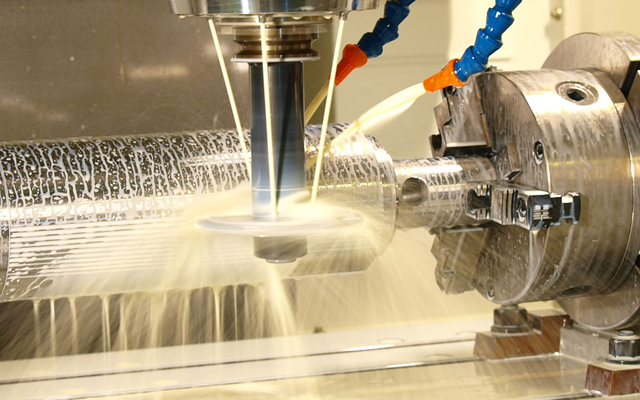
Types and Features of Cutting Oils
Cutting oils can be broadly categorized into two types: water-soluble and non-water-soluble, each with further subdivisions. Since the characteristics vary by type, it’s essential to choose the appropriate cutting oil based on the machining method and materials. Here, we will introduce the features of cutting oils based on their types.
・Water-Soluble Cutting Oil
Water-soluble cutting oil is used after dilution with water. It offers higher cooling capability compared to non-water-soluble types and is easier to use due to its lack of flammability. However, it requires careful management as it is prone to degradation over time.
Furthermore, water-soluble cutting oil is classified into three types based on its composition and appearance during use: Emulsion, Soluble, and Solution.
Emulsion (Type A1)
Emulsions are made from non-soluble components such as mineral oil and surfactants. As the name suggests, when mixed with water, it emulsifies and turns into a milky-white liquid. It has larger oil particles and boasts excellent lubrication among water-soluble oils. It can be used for heavy-duty cutting with high cutting resistance.
Soluble (Type A2)
Soluble oils are made from water-soluble components like surfactants alone or in combination with mineral oils. When mixed with water, it becomes semi-transparent or transparent. It maintains a good balance of lubrication, cleaning ability, and cooling, making it suitable for a wide range of applications including cutting and grinding.
Solution (Type A3)
Solution consists of components that dissolve in water without any oil content. It’s originally transparent, although it’s often colored green. It’s characterized by anti-foaming and high cooling properties, making it suitable for grinding operations.
・Non-Water-Soluble Cutting Oil
Non-water-soluble cutting oil, also known as straight oil, is used without dilution. It excels in lubrication, rust prevention, and penetration, making it suitable for high-precision machining. However, due to its flammability, it’s not suitable for unmanned operation.
Non-water-soluble cutting oil is divided into two types: active and inactive, based on the components such as oil additives, extreme-pressure additives, and rust inhibitors that enhance the oil film strength on friction surfaces.
Active types always contain extreme-pressure additives and are ideal for difficult-to-cut materials and gear machining. Inactive types come in both extreme-pressure additive-containing and non-containing variants, further divided into three types based on their corrosion characteristics with copper. They are primarily suitable for light cutting and softer workpieces.
Effects of Using Cutting Oil
What specific benefits can be obtained by using cutting oil during machining? Here, we will introduce the effects of using cutting oil during operations.
Reduction of Friction through Lubrication
The lubricating effect of cutting oil can reduce the frictional force between the workpiece and the cutting tool. This leads to extended tool life, reduced cutting resistance, prevention of tool edge wear, and improved finishing precision of the machined surface. Non-water-soluble cutting oils are considered superior to water-soluble ones in this regard.
Protection of Tools and Materials through Cooling
During cutting processes, temperatures as high as 600°C to 1,000°C can be generated due to friction between the tool and the workpiece. Cooling with cutting oil helps suppress this heat generation, preventing tool deformation, workpiece thermal distortion, enhancing machining precision, and increasing efficiency through shortened cutting times. Water-soluble cutting oil is effective when prioritizing cooling.
Prevention of Issues through Cleaning Action
Using cutting oil ensures constant flushing of chips from the machining area, which is advantageous. It prevents damage, blockages, and processing defects, while also offering protection to tools. Additionally, cutting oil helps prevent the scattering of chips by maintaining a wet cutting environment.
Preservation of Machines, Tools, and Products through Anti-Rust Action
Right after cutting, metal surfaces are exposed without any protective film, making them highly susceptible to oxidation, deterioration, and discoloration. Moreover, machines and tools, especially those with high rigidity, are prone to rust. Cutting oil often has strong anti-rust properties, which can assist in preserving machines, tools, and products. Generally, non-water-soluble cutting oils provide higher anti-rust effects.
Method of Applying Cutting Oil
There are two main methods for applying cutting oil: external lubrication and internal lubrication. Each method has its own advantages and disadvantages, so it’s important to choose the appropriate method based on the type of machining.
1. External Lubrication Method
The external lubrication method involves using an external device called a coolant hose to supply cutting oil to the machining area. This method may involve manually adjusting the position of the nozzle or adjusting the angle using numerical control (NC).
2. Internal Lubrication Method
The internal lubrication method involves supplying cutting oil through ports located on the machine tool’s spindle or tool. Compared to external lubrication, this method allows for higher-pressure and more precise application of cutting oil. It is particularly effective for machining processes that involve deep holes or grooves where it’s challenging for cutting oil to reach. This method can be further divided into two types: injecting cutting oil from the tool’s tip and injecting it from holes located around the spindle.
Points to Consider When Selecting Cutting Oil
When selecting cutting oil, it’s efficient to prioritize the aspects that are crucial for your specific operation. The following points should be considered when choosing cutting oil:
– Selection based on Workpiece Material
For cutting steel where lubrication is important, water-soluble cutting oils with emulsions are suitable, while non-water-soluble ones with active forms are preferred. For cast iron, anti-rust properties are vital, making non-water-soluble cutting oils appropriate. Aluminum alloys call for cutting oils that prevent discoloration. Copper alloys require non-water-soluble options, but active forms should be avoided due to copper corrosion.
– Selection based on Machining Process
Choosing cutting oil based on the machining process is also possible. Lathe operations, which demand high-speed machining, benefit from water-soluble cutting oils with good cooling properties. Milling processes require non-water-soluble cutting oils for their lubricating properties to prevent chipping. Hole drilling processes focus on cooling, often employing water-soluble emulsions.
Grinding processes require cutting oils with both lubricating properties to reduce frictional heat and cooling properties to remove generated heat. Soluble oils are well-suited for grinding processes.
– Consideration for Environmental Impact
From an environmental perspective, there’s been a rise in chlorine-free cutting oils to avoid generating dioxins when incinerating waste oil. Cutting oils that do not contain substances designated by the PRTR law are also available.
Additionally, dry machining and mist machining, which aim to reduce waste by using minimal or no cutting oil, have been developed. However, it’s challenging to apply these methods to all machining processes. To prolong the use of cutting oil, select cutting oils with good resistance to degradation and practice appropriate management.
Points to Note When Using Cutting Oil
When using cutting oil, it’s important to prevent its effects on the body and oil degradation. Here are some points to note:
– Effects of Oil Mist Dispersal
Cutting oil operations can result in the dispersal of oil mist (“oil mist”) during work, leading to dirty and slippery walls and floors. Since oil mist can also impact human health, measures to reduce dispersal, such as reconsidering the type and volume of cutting oil used or installing ducts, are crucial.
– Skin Contact Caution
Cutting oil on the skin can cause irritation and rashes. It’s important to wear protective clothing with minimal skin exposure and gloves to prevent oil contact.
– Protection of Eyes and Nose
Contact with cutting oil can cause inflammation in the eyes and potential danger from chips contained in dispersed oil mist. Inhaling the smell of cutting oil and oil mist can lead to discomfort, headaches, and other symptoms. Therefore, when using cutting oil, wearing protective goggles and masks to shield the eyes and nose is essential.
– Attention to Dilution Methods for Water-Soluble Cutting Oil
When using water-soluble cutting oil for machining, attention must be paid to the dilution process. Emulsions of water-soluble cutting oils containing components that do not dissolve in water may not emulsify properly if the dilution process is incorrect.
When diluting water-soluble cutting oil, it’s important to first add water to a tank and then add the cutting oil concentrate. Adding the concentrate before water can lead to uneven mixing. Immediate stirring after adding the concentrate is also important.
– Regular Maintenance
Routine management and inspection are essential to maintain cutting oil performance. Water-soluble cutting oils, in particular, can develop an unpleasant odor after long periods of machine inactivity. This odor results from the growth of bacteria due to the presence of mineral oil, surfactants, and contaminating lubricants in the cutting oil, causing it to degrade.
To prevent this odor, corrosion must be prevented through the use and proper concentration of anti-corrosion agents, and sludge and floating oil must be removed to prevent degradation. Monitoring the pH level, indicating the acidity or alkalinity of the cutting oil, can also be effective. pH is represented on a scale of 0 to 14, with 7 being neutral. As cutting oil degrades, it can shift from weakly alkaline (pH 8-10) to acidic, making pH a useful indicator of degradation.
For non-water-soluble cutting oils, be cautious about the introduction of chips, foreign matter, moisture, and other oils, as well as preventing a decrease in viscosity.
Importance of Cutting Oil for Enhancing Machining Precision
Cutting oils come in various types, each suitable for specific materials and processes. To maintain high machining precision, selecting the appropriate cutting oil and using it correctly is crucial. Incorrect usage or management can lead to a decrease in precision and problems like foul odors in the cutting oil. Select cutting oil that suits your work and material, follow precautionary measures, and carry out safe and accurate cutting operations.