Cutting fluid for CNC machine often used in aluminum processing, to reduce cutting temperature and ensure smooth operation. What is cutting fluid and what types of metal cutting fluid used in CNC machining? Here we’ll introduce its definition, function, purpose and how to choose a best cutting fluid.
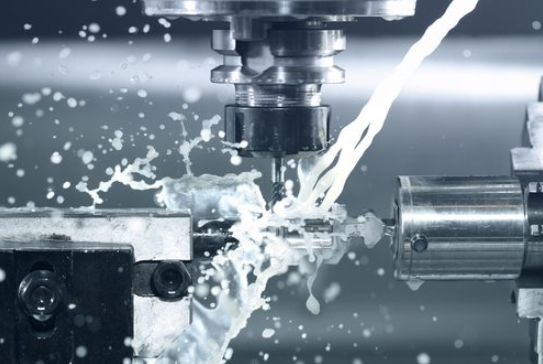
What is Cutting Fluid & What is Cutting Fluid Made of?
Cutting fluid, also known as coolant, cutting oil, cutting compound, or lubricant, is a kind of industrial liquid used in process of metal cutting like CNC machining to cool and lubricate cutting tools and work pieces. Cutting fluid is composed of a variety of super functional auxiliaries through scientific compound coordination, often made from petroleum distillates, animal fats, plant oils, water and air, or other raw ingredients. Without the shortcomings of traditional soap based emulsion, such as easy to stink in summer, difficult to dilute in winter and poor rust proof effect, cutting fluid has better cooling characteristics than saponified oil, suitable for cutting and grinding of ferrous metals, non-toxic, tasteless, non corrosive to human body, non-corrosive to equipment, no pollution to environment, and no adverse effect on lathe paint as well.
Types of Cutting Fluid
1. Water soluble cutting fluid
Its main component is water. Because the thermal conductivity of water is three times that of oil, its cooling performance is good. Adding a certain amount of anti-rust agent can also to lubricate and resist rust.
2. Emulsions:
(1) Ordinary emulsion: made up of anti-rust agent, emulsifier and mineral oil. It has good cooling, cleaning and lubrication performance, as well as rust prevention.
(2) Antirust Emulsion: add a large amount of anti-rust agent in the ordinary emulsion, used for strict anti-rust process and humid climate areas.
(3) Extreme pressure emulsion: add sulfur, phosphorus, chlorine extreme pressure additives, can form adsorption film under high temperature and pressure during cutting, for lubrication.
3. Cutting oil:
(1) Mineral oil: mechanical oil, diesel oil, kerosene, etc., suitable for general lubrication.
(2) Animal, plant and compound oils: soybean oil, rapeseed oil, cottonseed oil, castor oil, lard, etc. (3) Extreme pressure cutting oil: it is based on mineral oil, adding oil, extreme pressure additives and rust inhibitors.
Other metal cutting fluids including pastes, gels, aerosols (mists), and air or other gases.
What is Cutting Fluid Used for in CNC Machining? – Purpose or Function of Cutting Fluid
(1)Cooling: lower the cutting temperature, improve the tool durability and reduce the thermal deformation of workpiece, ensure the quality of CNC machining parts and process.
(2) Lubrication: reduce the friction between the chip and the tool front, back, workpiece, decrease the cutting force, heat and prevent the generation of chip lumps and scale thorns.
(3) Cleaning: wash the chip powder adhered to the workpiece, cutter and machine tool.
(4) Anti-rust: prevent the CNC machine, workpiece and cutting tool from being corroded by surrounding moisture, air, sweat.
How to Choose Right Cutting Fluid? – Recommended Coolant for Different Applications
1. According to the materials of workpiece or parts
(1) Cast iron and brass: generally no cutting fluid used. When finishing, use kerosene.
(2) Aluminum cutting fluid: kerosene.
(3) Non-ferrous metals: sulfur-containing cutting fluid should not be used.
(4) Magnesium alloy: mineral oil.
(5) General steel: emulsion.
(6) Difficult cutting materials: extreme pressure cutting fluid shall be used.
2. According to process requirements and cutting characteristics
(1) Rough machining: the cutting fluid with good cooling effect.
(2) Finishing: the cutting fluid with good lubrication effect.
(3) When machining holes: emulsion or extreme pressure cutting fluid with large concentration.
(4) Deep hole machining: cutting fluid with low EP additive concentration.
(5) Grinding: the cutting fluid with good cleaning effect.
(6) When cutting with cemented carbide, ceramics, PCD and PCBN tools: generally no cutting fluid used.