When selecting CNC tools in CNC machining, the size of CNC tools should be compatible with the machining size of die blank. For example, if the size of the die blank is 80 × 80, then you need to choose D25R5 or D16R0.8 and other CNC tools for roughening. If the size of the mold blank is greater than 100 × 100, then you should choose D30R5, D32R5 or D35R5 for roughening. If the size of the mold blank is greater than 300×30, then you need to choose larger than D35R5 for roughening, such as D50R5 or D63R6.
Small power CNC milling machine or machining center, can be installed larger than d5or5 CNC tools. In NC machining, the end mill is selected to process the periphery of the plane part contour, the high speed steel end mill is selected to process the concave and bar groove, the corn milling cutter with cemented carbide blade is selected to process the rough surface, and the ball head blunderbuss cutter, ring ratio cutter, batch milling cutter and disk milling cutter are selected to process some three-dimensional surface and variable angle contour.
In addition to choosing the right CNC tool, it is also very important to set the tool parameters correctly. The following figures list the parameter settings of white steel knife, flying knife and alloy knife.
Figure 1. White Steel Cutter Parameters
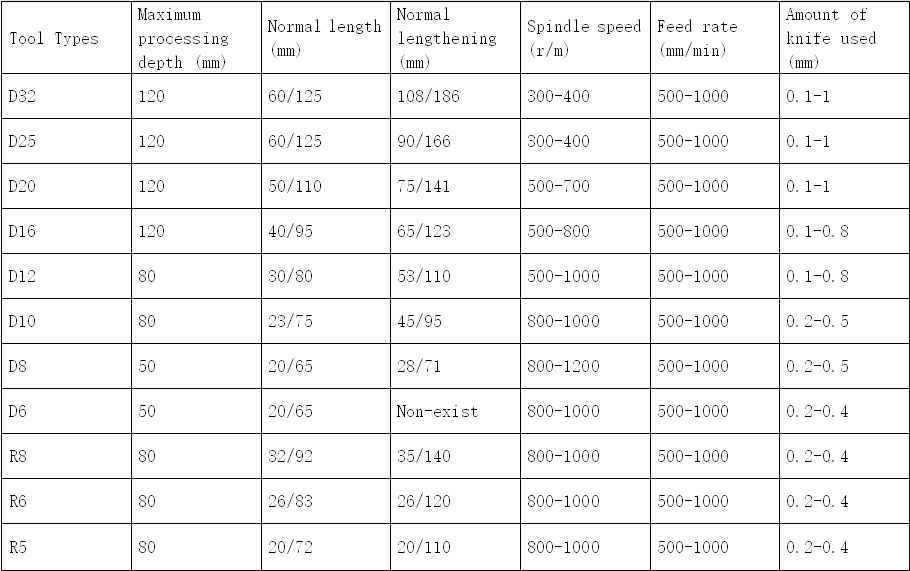
Here we need to pay attention to:
(1) The larger the diameter of CNC tool is, the slower the rotation speed is. For the same type of CNC tool, the longer the arbor is, the less the cutting amount is. Otherwise, it is easy to cause over cutting of the elastic tool.
(2) The rotation speed of white steel cutter should not be too fast and the feed speed should not be too large. The feed rate of 700mm / min is the most suitable when the plane is smooth.
(3) White steel knife is easy to wear, so use less white steel knife when cutting rough.
Figure 2. Fly Cutter Parameters
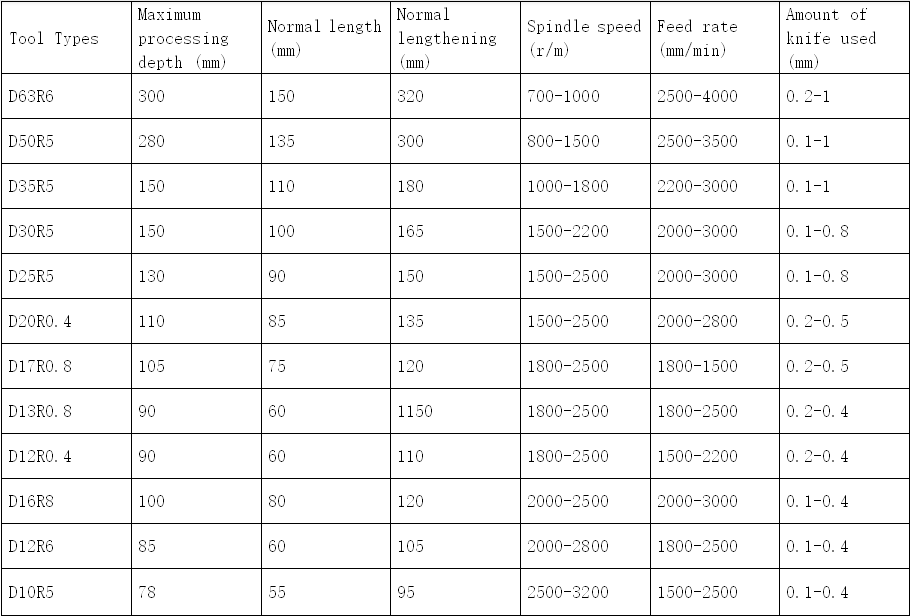
Here we need to pay attention to:
(1) In CNC machining, the above parameters can only be used as a reference. Different material parameters of flying tool are not the same, and the length of flying tool produced by different CNC tool factories is also different. In addition, the performance of CNC milling machine or machining center and different processing materials will also lead to the change of CNC tool parameters, so the tool parameters should be set according to the actual situation of the factory.
(2) The rigidity of the flying knife is delicious and the amount of the knife is large, which is most suitable for the roughening of the mold. In addition, the quality of the steep surface is also very good.
(3) The flying knife is mainly inlaid with knife grain and has no side edge.
Figure 3. Alloy Cutter Parameters

Here we need to pay attention to:
(1) In CNC machining, the rigidity of alloy tool is good, it is not easy to produce spring tool, and the effect of finishing die is the best.
(2) CNC alloy cutter and white steel cutter have the same side edge, which will be used when finishing milling copper straight wall.