A tool setter is a sensor used to measure the length of tools on CNC machine tools. By automatically measuring the tool length with micron accuracy and feeding it back to the Numerical Control (NC), it compensates for tool wear and thermal displacement of the tool caused by heat. This allows CNC machine tools to demonstrate their original high processing accuracy. Tool setters also detect chipping or breaking of the cutting edge and automatically stop the machine to prevent the occurrence of defective products. The need for trial cuts by skilled operators during tool change and manual input to the NC is eliminated, realizing automation of the machine.
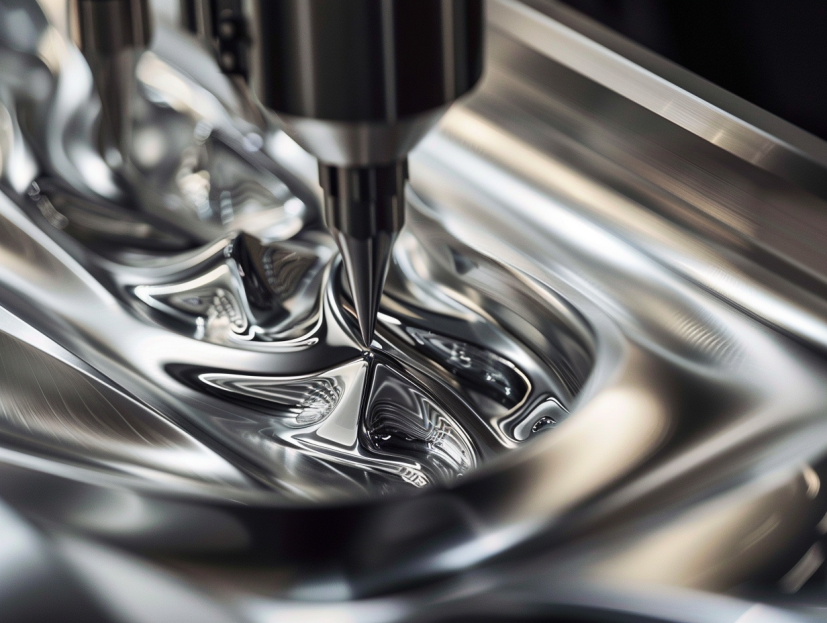
What is the CNC Tool Setter?
The tool setter is used when setting the shape correction value, which refers to the position information of the cutting edge of the tool being used. In machines equipped with a tool setter option, simply touching the cutting edge of the tool to the sensor in the X-axis and Z-axis directions of the tool setter inputs the position coordinates of the cutting edge, making it very quick, accurate, and easy to set.
Functions of Tool Setters:
- Measure and correct tool deviations in five directions: ±X, ±Z, and Y axis
- Automatic monitoring, alarming, and correction of tool wear or breakage during machining
- Correction of tool deviation fluctuations due to thermal deformation of the machine tool
Tool Setter Work Principle – How Does a Tool Setter Work in CNC Machining?
Tool setters for machining centers are mounted at the edge of the processing table and are used to measure the length of tools such as drills, mills, and end mills. The tool tip is pressed into the tool setter to emit a high-precision touch signal. The position of that signal point is read by the digital scale on the side of the machine tool and fed back to the NC to measure the tool length. By measuring all the tool lengths before processing and remeasuring after processing, the difference in length is corrected as “tool wear.” If the wear amount exceeds a specified value, it can also be detected as chipping or breaking of the tool.
The role of a Tool Setter:
In cutting machining on CNC machine tools, tools like CNC machining center tool length setters and CNC lathe cutting edge sensors use touch switches to automatically correct the cutting tool’s cutting edge position in the machine’s CNC system, enabling high-precision processing. Recently, micron-level accuracy has been required.
For “contact type,” the tool tip is pressed into the tool setter to emit a high-precision touch signal.
The position of that signal point is read by the “digital scale on the side of the machine tool” and fed back to the NC to measure the tool length.
By measuring all the tool lengths before processing and remeasuring after processing, the difference in length is corrected as “tool wear.”
If the wear amount exceeds a specified value, it can also be detected as chipping (breakage) or breaking of the tool.
For micron-level precision machining with an end mill, the tool length is measured and corrected after intermediate finishing, and then finish machining is performed for high-precision processing.
Tool Setter Setting Up – How To Use Tool Setter in CNC Machining?
The tool setter inputs tool position coordinates when the cutting edge touches the sensor in X and Z axes. Values are based on predefined machine origin and sensor position parameters. After inputting all tool offsets, a work origin point is set using a reference tool.
Input Values
When the cutting edge touches the sensor, the cutting edge position coordinates are input to the same number as the allocated tool post number. The X-axis inputs the distance from the cutting edge to the center of the spindle as a diameter value. The Z-axis inputs the distance from the end face of the turret to the cutting edge.
Method for Calculating Shape Correction Values
The values input for shape correction on the X and Z axes are based on values set in advance by parameters. The machine origin position is set with specific values for each machine on both the X and Z axes, and the sensor position is specified by parameters.
Setting the Work Coordinate System
After touching all the tools used in machining to the tool setter and inputting the X and Z-axis shape corrections, the machining origin must be set last. To set the position of the machining origin G54, a face and outer diameter finishing tool are allocated, and the shape correction is read.
General Types of Tool Setters
There are various types of tool setters depending on the operation they perform and the type of CNC machine they are used with. Here are some common types:
1. Presetter
A presetter is an independent device located outside the CNC machine that precisely measures the geometry of the tool. It provides the operator with the tool’s exact dimensions, which can then be input into the CNC machine’s control system to ensure accurate tool positioning.
2. Contact Tool Setter
Also known as a touch setter or a tool-setting probe, it is mounted on the CNC machine’s table or spindle. It works by physically touching the tool and sending a signal when contact is made, thus measuring the tool’s length and diameter.
3. Non-contact Tool Setter
These setters use laser or optical systems to measure tool dimensions without physical contact. They are often faster and can measure tools while they are spinning, which helps in detecting issues such as tool run-out.
4. In-process Tool Setter
This type of tool setter is used during the machining process to check and adjust tool dimensions on-the-fly. It helps to compensate for tool wear or breakage, ensuring continuous precision without stopping the machine.
5. Tool Breakage Detection
Some CNC machines are equipped with sensors that detect if a tool is broken or missing. This is a safety feature that prevents damage to the workpiece or the machine by stopping operation immediately upon detection of a problem.
6. Wireless or Wired Tool Setters
Tool setters may be wired or wireless. Wireless tool setters can be moved around easily and do not have cables that could interfere with machine operation.
Types of Tool Setters for Machining Centers (CNC Milling)
Tool setters for machining centers are divided into “contact type” and “laser type” based on the measurement method.
- Contact Type Tool Setter
This is a mechanical contact type tool setter. Since it directly touches the tool, it can reliably measure the tool length even under adverse conditions where coolant and chips scatter. They are easy to handle and cost-effective, widely used in various machines from small machining centers to large 5-axis machines.
- Laser Type Tool Setter
This is a non-contact type tool setter using a laser. Since it does not touch the tool, there is no need to stop the tool’s rotation, and even thin drills can be measured without applying load. There is no concern for tool damage due to collisions during measurement since there are no physical contact parts.
Types of Tool Setters for CNC Lathe
Tool setters used in NC lathes are attached to a dedicated arm for detecting the cutting edge of the tool. They are usually stored in a dedicated space next to the chuck and swing out during measurement. Due to space constraints inside the machine, contact type tool setters are mainstream.
- Manual Setters
Z-Setter or Height Setters: These are gauge blocks or specialized devices that are placed on the machine’s chuck or on the workpiece. The tool is manually brought into contact with the setter to establish the Z-axis (length) offset.
- Contact Tool Setters
Tool Setting Probes: These are probes that are mounted on the turret or the tool post. The cutting tool is brought into contact with the probe, and the machine control records the position to determine the tool’s offset.
Tool Setting Gauges: Handheld or mounted gauges can be brought into contact with the tool. When the tool touches the gauge, a setting is established.
- Automatic Tool Probing
In-turret Tool Probing Systems: These systems are mounted on the turret and include a touch-trigger probe. The lathe automatically jogs the tool to make contact with the probe, and the position is recorded for tool offset purposes.
- Non-contact Tool Setters
Laser Tool Detection Systems: A laser beam is projected, and when the tool passes through the beam, the machine detects the interruption and records the tool’s position. This system is fast and does not involve any physical contact with the tool, minimizing the risk of tool damage.
Types of Manual Tool Setters
There are also manual tool setters, which are not suitable for machine automation but can be easily used for general-purpose machine tools and as assistance for operators.
- Tool Presetter
The tool presetter is a manual tool setter used outside of NC machine tools. Tool lengths are measured in advance outside the machine, and the values are manually inputted into the NC. They are used for measuring tool lengths during external setup and for overall tool management in the factory.
- Simple Tool Setter
The simple tool setter is a manual tool setter used inside the machine tool. During measurement, it is magnetically fixed to the table to measure the tool length. It is used for measuring tool lengths on general-purpose machine tools and as assistance for operators during tool changes.
CNC Tool Setter Cost – How Much Cost for Tool Setting?
The cost of a CNC tool setter can vary based on several factors, including the brand, precision, features, and whether it’s manual or automated. As of my last training data in April 2023, here’s a general overview of the price ranges you might expect:
- Manual Tool Setter: A simple, manual tool setter or tool setting gauge for a CNC machine can range from around $50 to $500. These are typically used for setting tool lengths and may not have any digital readouts.
- Touch Off Probes: More advanced touch probes that integrate with the CNC control system for automated tool length measurement can range from $500 to a few thousand dollars depending on the level of precision and features.
- Wireless Tool Setters: Mid-range wireless or infrared tool setters that communicate with the CNC controller for semi-automated tool setting can cost between $1,000 and $5,000.
- Automatic Tool Presetters: High-end automatic tool presetters that can measure tool geometry and provide detailed information for CNC machining can cost from $5,000 to over $20,000. These systems are often standalone units that can be used independently of the CNC machine to prepare tools for use.
- Integrated Tool Setting Systems: Some CNC machines come with integrated tool setting systems as part of a package when purchasing the machine. These systems can be proprietary and specifically designed to work seamlessly with the machine’s control system.
By using a tool setter, you can greatly reduce setup time, reduce the need for in-machine measurement work, and improve safety during trial processing. If it is a type that can move forward and backward automatically, it can also be used to check wear and detect damage. It is often used as an option to shorten setup time and improve productivity.