CNC lathes are transformed and evolved from conventional lathes with the Computer Numerical Control technology and have developed a variety of types. As a custom CNC turning manufacturer, CNClathing.com will introduce what a CNC lathe is, along with its history, uses, advantages over manual lathes, working principle, operations, components, types, and more.
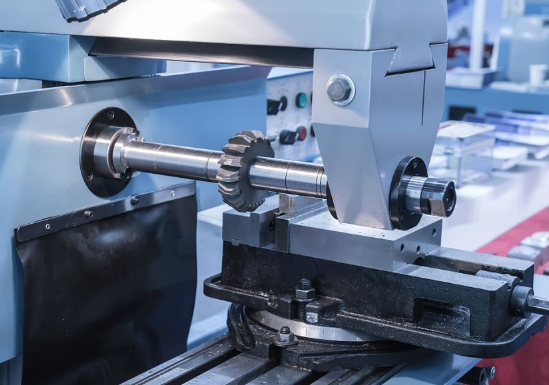
What Is a CNC Lathe (CNC Turning Machine)?
A CNC lathe is a computer-controlled machine mainly for CNC turning services and processes, including tapered turning, hard turning, spherical generation, facing, parting, knurling, drilling, grooving, etc. These operations can be carried out like a conventional lathe machine, while a CNC turning lathe is designed to utilize modern technology and tooling to improve the productivity and quality of CNC turning parts.
History of the CNC Lathe Machine
The CNC lathe evolved from the ancient manual lathe, which dates back to early Egypt, where it was used for woodworking. The key transformation occurred in the mid-20th century, when pioneers like John T. Parsons introduced computer numerical control to automate and improve precision in machining. Since then, CNC lathes have revolutionized manufacturing by combining traditional turning with computerized control, enabling highly accurate and repeatable production.
What Can You Make with a CNC Lathe?
You can manufacture cylindrical and symmetrical parts like shafts, rods, and fasteners. Complex components for aerospace and medical devices are also possible. Additionally, CNC lathe machines produce products like baseball bats, cue sticks, chair legs, and even detailed wooden musical instrument bodies.
What Are the Application Fields of a CNC Lathe Machine?
CNC lathes are widely used across industries such as automotive, aerospace, electronics, medical device manufacturing, firearms, sports equipment, and woodworking. They are widely applied for producing precision components, intricate shapes, and repeatable parts in mass production or custom manufacturing.
How Much Does a CNC Lathe Cost?
The price of a CNC lathe or CNC turning machine is affected by lots of factors, such as the type, size, configuration, brand, and more. Entry-level models for small businesses typically range from $20,000 to $60,000, mid-range machines cost between $60,000 and $250,000, while high-end industrial CNC lathes with advanced multi-axis capabilities can exceed $500,000. The manufacturing quality, machine size (determined by chuck size and distance between centers), design complexity, special functions, and shipping expenses may influence the final price.
CNC Lathe vs Manual Lathe: What Are the Differences & Advantages of CNC Lathes
- CNC lathes are controlled by computer programming, whereas manual lathes rely on direct human operation.
- CNC lathes achieve far higher precision and repeatability compared to manual lathes.
- CNC machines reduce human error, resulting in less wasted material and fewer defective parts.
- CNC lathe machines offer higher efficiency as one operator can oversee multiple machines simultaneously, unlike manual lathes.
- CNC lathes can perform complex, multi-step machining operations in one setup, while manual lathes often require multiple setups.
- CNC turning on a lathe speeds up production and reduces labor costs despite a higher initial investment.
- Manual lathes provide more tactile feedback for skilled craftsmen.
Main Operations Performed on a CNC Lathe
- Turning: Removes material from the outside to create cylindrical shapes. Multiple turning operations can be performed on lathes, including taper turning, step turning, contour turning, eccentric turning, and more.
- Facing: Cuts a flat surface on the end or along the length of the workpiece.
- Drilling: Creates holes with a drill bit.
- Boring: Enlarges existing holes to precise dimensions.
- Reaming: Finishes holes for accuracy and surface finish.
- Threading: Cuts internal or external threads.
- Knurling: Produces patterned surfaces for grip.
- Grooving: Cuts narrow grooves for function or aesthetics.
- Parting/Cutting Off: Separates the part from the stock material.
- Chamfering: Cuts bevels on edges.
- Tapping: Forms internal threads with a tap tool.
Main Components of CNC Lathes
Different types of lathe machines have different configurations, but a CNC turning lathe is basically composed of the following parts. Modern CNC lathe machines are often mounted with live tools that can work in multiple axes, like both X and Y axes, a second turret with different tools, and more.
Headstock
The headstock is located at the front of the CNC lathe and houses the main motor and spindle, which power and rotate the workpiece during machining. It contains the gear mechanisms that control spindle speed and torque, essential for handling different materials and cutting conditions.
Main Spindle
Known as the heart of the machine, the main spindle holds the chuck or collet and rotates the workpiece. It is powered by the headstock motor and can operate at various speeds with minimized vibration for precision turning.
Chuck and Collet
The chuck is a vice-like device attached to the spindle that securely grips the workpiece; it is removable to accommodate different sizes. Collets are similar but typically used for smaller parts (up to about 60 mm in diameter), offering a more precise grip for delicate or smaller components.
Tailstock
Positioned opposite the headstock on the bed, the tailstock provides support for longer workpieces during machining. It can apply hydraulic force to stabilize the workpiece but is usually retracted during face turning to avoid interference.
Lathe Bed
The bed is the solid foundation of the CNC lathe, supporting all other components. Made from high-quality cast iron to resist heat distortion and vibration, it ensures mechanical stability and precision throughout machining operations.
Carriage
The carriage moves along the lathe bed and carries the cutting tool, allowing it to slide smoothly along the workpiece. It enables precise tool positioning and controlled cutting motion essential for shaping the material.
Tool Turret
The tool turret is a rotating disk that holds multiple cutting tools, allowing quick tool changes during machining. It provides a strong clamping force to keep tools stable and supports fast indexing between tools to increase productivity.
Sub-Spindle (Second Spindle)
An optional component, the sub-spindle works alongside the main spindle to perform secondary operations on the workpiece without requiring removal, improving efficiency and cycle time in complex machining tasks.
Guideway
Guideways are precision rails that allow the carriage and tool turret to move accurately along the X, Y, and Z axes. They are designed for rigidity and durability, enabling smooth and precise cutting motions.
Control Panel (CNC Controller)
The control panel is the user interface where operators input coded instructions (G-code) to program and control the lathe’s movements and operations automatically.
Coolant System
This system delivers coolant fluid to the cutting area to reduce heat generated during machining. It helps prolong tool life, improve cutting performance, and maintain the dimensional accuracy of the workpiece.
Chip Pan/Conveyor
Some lathes will equip a chip pan or conveyor to automatically collect and remove chips generated during machining, in order to keep the working area clean and prevent damage or interference with the tooling.
Diagram of CNC Lathe Machine Parts
How Does a CNC Lathe Work?
CNC turning lathes are used to produce precise turned parts with round or cylindrical shapes. The finished product is complete and does not need a second operation on other CNC machining equipment. The CNC controller works with the drive motor and makes multiple components work together and move the shaft to complete the designed motion according to the CNC programming.
- Check out whether there are any faults and abnormal situations, and perform troubleshooting.
- Upload the G-Code computer file to the CNC lathe.
- Install a cylindrical material block and secure it in the chuck.
- Set the spindle at the required speed, then rotate the chuck and workpiece.
- Check the rotating workpiece and spindle speed; ensure there is no discrepancy.
- Move the tool turret and carriage to locate the cutting tool at a specific feed
- Move the carriage to perform the cutting operation, and remove all excess materials to get the final CNC lathe part.
Types of CNC Lathe Machines
Like the typical CNC turning machine, lathes can be classified according to different standards.
1. Based on the number of axes:
- 2-axis CNC Lathe: can perform outer/inner diameter machining, facing, drilling, and tapping.
- 3-axis CNC Lathe: X and Z-axis, C-axis and live tool system, allowing to perform milling, boring, etc.
- 4-axis CNC Lathe: add Y-axis based on 3-axis machine for off-center machining operations and complex parts.
- 5-axis CNC Lathe: add a second turret, allowing two tools to work at the same time
2. Based on the work requirements
- Speed Lathes: simple design, composed of headstock, tailstock, and tool post, can operate in three and four speeds.
- Engine Lathes: the most common lathe machine, can operate with diverse metals at a wide range of speeds, length up to 60 feet.
- Turret Lathes: many different types of tool holders can be mounted on it.
- Tool Room Lathes: produce parts with good accuracy and finish.
3. Based on the position of the lathe spindle
- Vertical CNC lathe: the lathe spindle is perpendicular to the horizontal, with a large diameter circular table used to clamp the workpiece.
- Horizontal CNC lathe: can be divided into flat guide rail CNC lathe and slant guide way CNC lathe, the slant guideway structure can make the lathe more rigid and easier to discharge chips.