In machining processes, chamfer and bevel are two common edge treatment methods. They are both used to deburr and eliminate sharp edges. However, there are inherent differences between them in terms of definition, design purpose, application scenarios, machining techniques, etc. This article will comprehensively compare and analyze chamfer and bevel in machining to provide references for engineering design and manufacturing.
What is Chamfer?
A chamfer refers to the machining process of grinding, truncating or deburring the edges or corners of an object at a certain chamfer angle to form a sloped surface at a certain inclination in order to eliminate sharp edges and corners. The chamfer angle is usually 45°, but can also be 30° or 60°. The width of a chamfer is relatively narrow, generally controlled within 1-2mm.
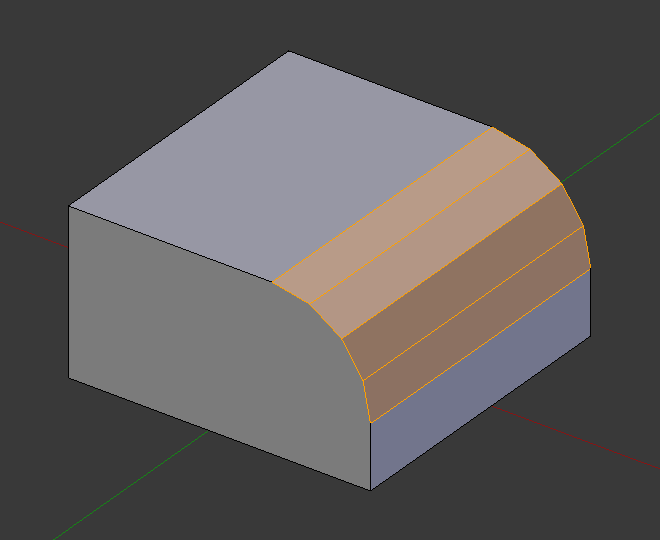
What is Bevel?
A bevel is a method of inclined machining on edges or corners at an angle greater than 45°, forming an inclined surface at a certain angle. In addition to eliminating sharp edges and corners, a bevel also has a decorative function. Bevel angles can be set to 60°, 75° etc., and the width is also significantly larger than a chamfer.
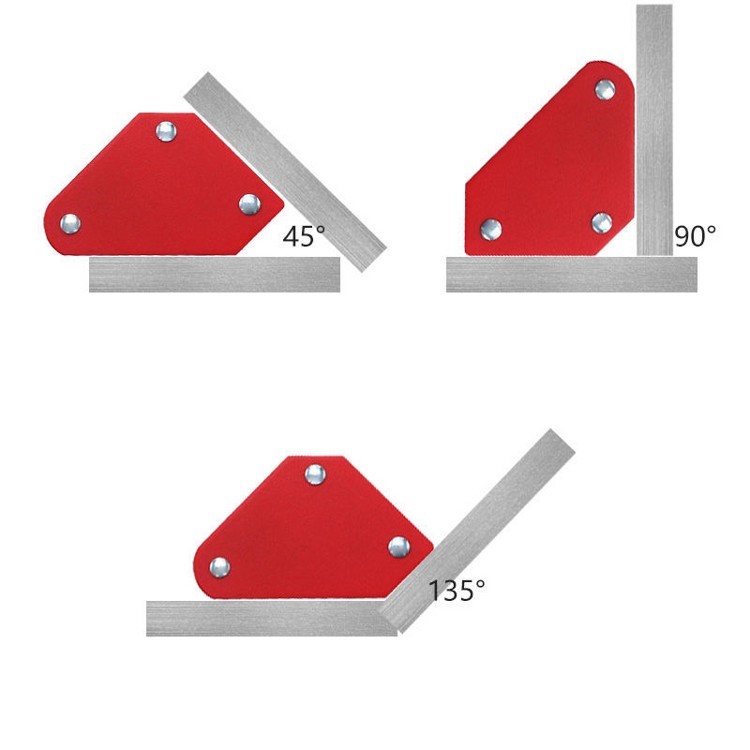
Length and Angle of Chamfer vs. Bevel
A chamfer or bevel can be defined using one of two methods: distance or angle. The current way to define a chamfer or bevel is to set it using the Method option.
Distance: The angled line formed is based on two distance values. These two distance values are used to trim or extend the selected object to intersect the resulting angled line. The first distance value affects the first object selected, while the second distance value affects the second object selected.
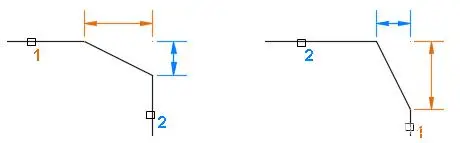
Angle: The angled line formed depends on the distance and angle values. The distance and angle values are used to trim or extend the selected objects to intersect the resulting angled line. The distance value directly affects the first object selected
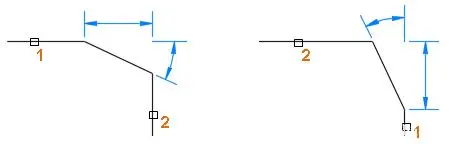
Note: If both the distance and angle values are set to 0, the selected objects will be trimmed or extended until they intersect without creating any angled lines
Differences Between Chamfer and Bevel in CNC Machining
Chamfering and beveling are common processing edges in CNC machining. They can both remove sharp angles, but the difference between the two in mechanical structure and appearance design is still obvious. Now we will compare chamfer and bevel from multiple perspectives such as definition, design considerations, processing methods, cost and time, etc., to explain the application options of the two in different scenarios.
Chamfer | Bevel | |
Shape | Flat, angled surface meeting at 45 degrees | Sloped or rounded edge usually at less than 45 degrees |
Effect | Takes off sharp edge but maintains corner | Softens and rounds over edge, can reduce corner |
Appearance | Straight lines meeting at angle, squared off | Curved transition, rounded appearance |
Common Uses | Industrial parts, furniture, woodworking | Decorative edges, rounded contours |
Angle | Usually 45 degrees | Variable angles less than 45 degrees |
Corners | Maintains original corner angle | Can reduce or eliminate corner angle |
Machining Method | Simple, high-speed tools for bulk parts | May require multiple tools or manual work |
Cost and Time | Generally lower due to simple machining | Higher cost/time for complex curves or manual work |
Post-machining | Flat edges easier for finishing/coating | Curved surfaces harder to finish/coat |
Stress Concentrations | Potential for minor stress risers | Curves help reduce stress concentrations |
Chamfer vs. Bevel: Difference in Design Purpose
The design purpose of a chamfer is to improve mechanical properties, increase strength, reduce stress concentration, and improve machining quality. Therefore, the angle and width of a chamfer are relatively fixed, usually 45° and 1-2mm. These parameters can optimize the balance between strength and ease of machining.
While eliminating sharp corners, a bevel also has a decorative function. The angle and width of a bevel can be flexibly designed according to the desired decorative effect, generally choosing an angle greater than 45° and a much larger width than a chamfer. The design of a bevel takes aesthetics and customization requirements into account.
Chamfer vs. Bevel: Difference in Shape
From a morphological point of view, chamfer refers to the plane formed by the intersection of two sides with an acute angle, and the angle is generally 45 degrees;
while the bevel uses an inclined arc surface to modify the edge, and the angle is usually less than 45 degrees;
Therefore, the chamfer retains the original angle and adopts a flat line; while the bevel reduces or eliminates the angle through the arc surface, making the edge appear in the form of an arc.
Chamfer vs. Bevel: Difference in Appearance
In terms of design, the chamfer highlights the squareness and fits the industrial style; at the same time, chamfering can well preserve the geometric shape of the component and facilitate subsequent assembly.
The bevel emphasizes streamlined shape and is suitable for products that require a beautiful glossy effect. Bevel angle will affect the combination relationship by changing the angle shape and needs to be considered in the early design stage.
Chamfer vs. Bevel: Difference in Application
Due to the different functional emphases, there are significant differences in the application scenarios of chamfers and bevels.
Chamfers are mainly used in engineering machinery, such as machine tool accessories, measuring tools, fixtures, etc., to improve overall strength, machining quality, reduce cutting resistance, prevent scratching operators, etc.
In addition to engineering applications, bevels are more often used in areas that require aesthetic appearance, such as high-end furniture, handicrafts, architectural decoration, etc., to enhance individuality and decorativeness.
Chamfer vs. Bevel: Difference in Machining Techniques
The machining techniques for chamfers and bevels also differ:
Chamfer machining is relatively simple, usually using an angled planer or specialized chamfering wheel, and consistent chamfer effects can be achieved in one machining pass. The operation difficulty is low and suitable for mass production.
Bevel machining is more complex, requiring multiple machining passes on CNC machines to achieve larger bevels. Even small bevels are difficult to achieve with a single tool. Therefore, bevel machining requires better tool coordination and higher operation difficulty.
Chamfer vs. Bevel: Difference in Machining Efficiency
Due to the difference in machining techniques, there is also a significant gap in machining efficiency between chamfers and bevels.
Chamfers use standard tools and parameters, and can be completed in one machining pass, hence higher efficiency. Bevels require careful tool path planning and machining strategies, often needing multiple steps to meet quality requirements, hence lower efficiency.
For the same machining length, the machining time for chamfers is significantly shorter than that for bevels, which matches their difference in difficulty.
Chamfer vs. Bevel: Difference in Machining Tools
Chamfering mainly uses general tools such as grinding discs and planers.
Depending on the material and accuracy requirements, the bevel can be made using a planer or ball nose planer, or it can be done on a CNC machine tool. Tool selection needs to consider the width and angle of the bevel.
Chamfer vs. Bevel: Factors Affecting Machining Quality
The main factors affecting the machining quality of chamfer and bevel include:
- 1. Sharpness and precision of tools
- 2. Rigidity and stability of machine tools
- 3. Reliability of locating and clamping
- 4. Reasonable selection of machining parameters
- 5. Reasonable planning of tool paths
These factors have greater impact on bevels, because bevel machining has higher process requirements, and any unreasonable aspects will lead to quality reduction. Chamfer machining is simpler and more controllable with lower quality risks.
Chamfer vs. Bevel: Difference in Ease of Processing
The processing difficulty of chamfering is relatively low, and it can usually be achieved by using a general chamfering grinding disc or planer.
Depending on the angle, some bevels are difficult to complete by hand, and a CNC machine tool is required to ensure processing quality.
Chamfer vs. Bevel: Difference in Machining Costs
Considering factors like time and tool wear, the machining cost of bevels is higher than that of chamfers. Main reasons:
- 1. Bevel machining is more complex, requiring more fixtures and tools.
- 2. Bevels typically need multiple steps with higher labor intensity.
- 3. Machining errors have greater impact on bevels with higher scrap rates.
- 4. Bevel machining requires higher operator skills.
In comparison, chamfer machining is simple and efficient with higher material utilization, hence lower costs.
Chamfer vs. Bevel: Difference in Surface Finish
To improve surface properties, mechanical parts usually require surface treatment. There are also some differences in coating adhesion between chamfer and bevel:
Chamfer Surface Finish: The short transition of a chamfer leads to poor coating adhesion. The coating is prone to cracking and peeling, reducing surface performance. The gradual transition of a bevel allows better adhesion and longer service life.
Bevel Surface Finish: Therefore, bevels should be preferentially considered where high coating adhesion is required. Chamfers can also meet temporary coating needs.
Chamfer vs. Bevel: Which One To Choose For Your CNC Parts
Based on the differences above, the following principles can be summarized for selecting chamfers and bevels:
- 1. Chamfers are preferred when high mechanical strength and machining quality are required.
- 2. Bevels are prioritized when high aesthetic and customization requirements are needed.
- 3. Chamfers are more suitable for cost-sensitive high volume production.
- 4. Bevels are recommended when coating adhesion and corrosion resistance are important.
- 5. Their pros and cons can also be balanced based on actual situations.
Chamfer and bevel are both important edge treatment methods, but with distinct application ranges and scenarios. Chamfers pursue functionality while bevels consider both decoration and function. In engineering design and machining, the functional positioning and performance requirements of a product should be the primary considerations when choosing between chamfers and bevels. Only by distinguishing their suitable applications can the advantages of each be leveraged to achieve optimal designs and machining solutions.