Cast iron is a versatile metal used in various automotive components such as engine blocks, heads, flywheels, and brake rotors, as well as everyday items like household pots and road manhole covers. However, there are several types of cast iron, each with its own unique characteristics. This context talks about the types and characteristics of cast iron, as well as points to consider during CNC processing.
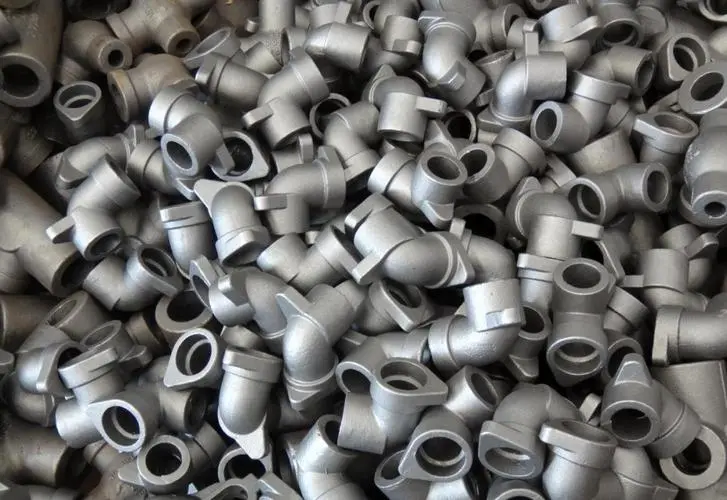
What is Cast Iron?
Cast iron is a general term for alloys of iron (Fe) containing a significant amount of carbon (C), ranging from 2.1% to 6.7% carbon content. As the carbon content increases, the melting temperature decreases, making it relatively easy to pour and shape cast iron into molds. This is due to the phenomenon of eutectic solidification, where the addition of another substance to a pure substance lowers the temperature at which it transitions from liquid to solid. Cast iron has a wide range of applications, from mechanical components and industrial products to everyday items like water pipes and manhole covers.
Differences Between Cast Iron, Steel, and Iron Lie in “Carbon Content”
Generally, “pure iron,” which has a high iron content and high purity, is too soft and prone to oxidation, making it impractical for many uses. Therefore, carbon and other elements are added to increase strength, resulting in the creation of cast iron and steel.
In essence, cast iron, iron, and steel are all metals composed of iron and carbon, with the major distinction being the amount of carbon present. Arranged in order of increasing carbon content, it goes cast iron, steel, and iron (pure iron). Furthermore, steel can be classified into carbon steel, consisting of iron and a specific proportion of five elements (carbon, silicon, manganese, sulfur, and phosphorus), and alloy steel, which includes other metals.
As the carbon content approaches that of low-carbon pure iron, hardness and wear resistance decrease while toughness and melting temperature increase. Conversely, higher carbon content enhances hardness and wear resistance but reduces toughness and melting temperature.
Difference Between Cast Iron and “Castings”
Similar to cast iron, the term “castings” refers to items created by pouring melted material into molds. The distinction between cast iron and castings is that cast iron refers to the material itself, while castings refer to the products made from the material.
Cast iron has a high production volume and is frequently used in castings, although not all castings are made of cast iron. Cast steel (chukou) can be heated up to 1500°C and poured into molds, and materials like aluminum, copper, and magnesium are also used for castings.
Types of Cast Iron
Cast iron is categorized into various types based on additives, carbon state, manufacturing methods, etc., each possessing different characteristics. The types of cast iron and their respective features are as follows:
・White Cast Iron:
When cast iron contains a low amount of carbon and silicon, carbon does not precipitate as graphite but forms cementite (Fe3C), a carbon compound. This cementite crystallization results in a white appearance on fracture surfaces, hence the name “white cast iron.” White cast iron is hard and exhibits excellent wear resistance but is difficult to machine, brittle, and prone to cracking.
・Gray Cast Iron (FC):
When cast iron has a moderate amount of carbon, carbon crystallizes mostly as graphite rather than cementite. The influence of graphite results in a gray appearance on fracture surfaces, leading to terms like “gray cast iron” or “ordinary cast iron.”
It is abbreviated as FC, representing the initials of “Ferrous” (Fe) and “Casting,” followed by a three-digit number denoting tensile strength. For instance, FC150 indicates gray cast iron with a minimum tensile strength of 150 or more. The type with a flake-like graphite structure is referred to as “lamellar graphite cast iron.” Instances where both gray and white cast iron coexist, creating a fracture surface with black and white spots, are known as “mottled cast iron.”
Gray cast iron possesses lower strength and toughness, but it is easy to cast and has high machinability. Alongside excellent wear and corrosion resistance, it has a unique property of vibration absorption, making it suitable for a wide range of applications such as machine bodies, parts, and engine cylinder blocks.
・Ductile Cast Iron (FCD):
“Ductile” in English refers to being “flexible” or “malleable.” By adding elements like magnesium (Mg) and cerium (Ce), graphite in the structure is transformed into spherical shapes, resulting in ductile cast iron (FCD). Due to the appearance of spherical graphite, it’s also referred to as “spheroidal graphite cast iron” or “nodular cast iron.”
Ductile cast iron is a type of “tough cast iron (premium cast iron)” with superior strength, possessing several times the strength of gray cast iron. This is attributed to the spherical graphite, which reduces stress concentration around the graphite when subjected to tension or bending.
It offers excellent mechanical strength, wear resistance, and heat resistance. Toughness and corrosion resistance can be enhanced through heat treatment, but caution is required due to the tendency for magnesium-induced shrinkage and pinholes. Additionally, its tendency to harden and elongate can make machining challenging.
Leveraging its high strength, it is widely used in parts requiring strength, such as automobile components, road manhole covers, water pipes, and gas pipes.
・Compacted Vermicular Cast Iron (CV):
CV cast iron possesses characteristics that lie between those of gray and ductile cast iron. CV stands for “Compacted Vermicular,” referring to its vermicular graphite structure, resembling the shape of caterpillars.
CV cast iron boasts strength similar to ductile cast iron while excelling in machinability, castability, high thermal conductivity, and vibration absorption. Utilizing these properties, it finds applications in hydraulic valves and cylinder blocks.
・Malleable Cast Iron:
Malleable cast iron (katan chutetsu) is created by heat treating white cast iron to enhance its ductility. Unlike gray and ductile cast iron, which form graphite during casting, malleable cast iron is created by annealing white cast iron and generating graphite from cementite. It compensates for cast iron’s brittleness and limited elongation by retaining castability similar to gray cast iron. It is less prone to fracture even when subjected to impact.
Malleable cast iron can be categorized into three types based on heat treatment methods: “white heart malleable cast iron,” “black heart malleable cast iron,” and “pearlitic malleable cast iron.”
White Heart Malleable Cast Iron – White heart malleable cast iron has had some carbon removed (decarburization) through heat treatment. Since it lacks graphite, it exhibits properties similar to steel. It combines good castability and toughness, allowing for welding and brazing.
Black Heart Malleable Cast Iron – Heat treatment decomposes the cementite in white cast iron, resulting in a structure consisting of ferrite and graphite. It possesses softness and good elongation.
Pearlitic Malleable Cast Iron – Pearlite is a layered structure composed of alternating layers of ferrite (α-iron crystal) and cementite. Through shorter heat treatment compared to black heart malleable cast iron, the iron portion becomes a pearlitic structure. It exhibits toughness and notably high tensile strength within malleable cast iron.
Features of Cast Iron:
As previously mentioned, cast iron is characterized by its higher carbon content compared to other forms of steel such as alloy steel or carbon steel. The presence of carbon leads to a lower melting point, allowing for operations like melting and casting to be carried out at relatively low temperatures.
Moreover, as evident from the various types, characteristics of cast iron are influenced by factors like the shape, size, and distribution of graphite. This allows material properties to be altered based on graphite distribution. Strength properties can be changed through heat treatment or the addition of alloying elements.
Machinability and Processing Considerations for Cast Iron:
Cast iron possesses generally good machinability, making it a metal that is easy to cut and machine. Compared to steel and stainless steel, cast iron has lower cutting resistance and generates less cutting heat, which is advantageous for chip removal. However, proper tool selection and machining techniques are still crucial. Here are some points to consider when selecting tools for machining cast iron and during the machining process:
・Suitable Cutting Tools for Cast Iron:
Due to the structure of graphite causing the chips to break into smaller pieces, cast iron has good chip evacuation characteristics. Graphite also provides lubrication, reducing cutting resistance. However, cast iron is generally hard, and tools with sharp edges and large rake angles are prone to chipping. To prevent chipping, it’s advisable to choose negative rake angle inserts with a smaller rake angle.
・Points to Consider When Machining Cast Iron:
For cutting operations on cast iron, dry machining without the use of cutting oil is common. Wet machining might be used to minimize the effects of dust, but caution is needed as wet chips might clog grooves and cutting surfaces. Different types of cast iron exhibit varying mechanical properties, so adjustments to cutting conditions are necessary. Generally, gray cast iron is easier to machine, while ductile cast iron is hard and tends to elongate, making edge chipping more likely. White cast iron, on the other hand, is particularly hard and wear-resistant, making machining more challenging.
Challenges in Welding Cast Iron:
While cast iron is often considered easy to machine, it is often regarded as difficult to weld. This is primarily due to the high carbon content in cast iron. Cast iron generally has lower tensile strength and lacks ductility compared to steel.
The challenges arise from factors such as the formation of brittle cementite phase upon rapid cooling from the molten state, leading to increased susceptibility to cracking. Additionally, the combustion of graphite during welding can result in blowholes (internal voids) and pits (surface depressions). To achieve successful welding results, careful consideration of welding methods and welding rods is necessary.
Understanding Cast Iron Characteristics for Processing:
While cast iron may be perceived as brittle and prone to cracking, it also boasts properties such as hardness, excellent wear resistance, and vibration absorption. Machinability is considered good, but mechanical properties differ between easy-to-machine gray cast iron and ductile cast iron. Different types of cast iron exhibit distinct characteristics, necessitating adjustments in cutting tools and cutting conditions.
Given its generally hard and brittle nature, it’s crucial to choose tools and set conditions to address edge chipping and material fragmentation. Moreover, preventing the deterioration of machine tools due to dust and maintaining a suitable work environment are essential considerations. When machining cast iron, understanding the characteristics of each type is key to selecting the right tools and achieving successful processing.