In conventional slot milling, the milling cutter is engaged in the material with its complete diameter. This means that the arc of engagement is maximum. Conventional three-axis machines can be used and only basic programming is required. When using the high-feed side milling strategy is it important to keep the hex maximum chip thickness constant during the entire cutting process. With this strategy the radial engagement is low and the tool is programmed with a continuous spiral path, controlling the arc of engagement.
Traditional Slot Milling Vs High-Feed Side Milling
Let’s compare the two approaches in the case of a narrow slot of a soft ISO P material:
The slot dimension is the same in both cases. Both strategies are safe but some differences can be highlighted.
– The conventional roughing method can be very productive with high material removal rates under stable conditions. It may cause high heat generation on the tool and workpiece, which requires lower cutting speeds.
– Generally, the conventional method requires less machine time than the high-feed milling method. More power is required for conventional milling and higher radial cutting forces are generated. This can create deflection problems and a vibration sensitive approach. This approach is also limited in terms of axial engagement so repeated passes are required with deep slots.
Let’s consider a deep slot of a harder ISO P material:
In the example on the left side there is the conventional full slot milling, while on the right side is the high-feed side milling strategy. On the left, the slot cannot be created in just one pass and a lot of heat is generated. On the right, when the high-feed side milling technique is utilised, the whole cutting edge is used, ensuring that the heat and wear are uniform and spread out, allowing for longer tool life.
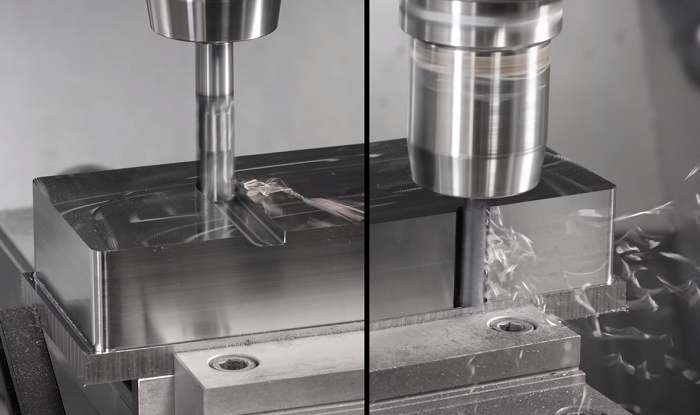
By using large Ap and low Ae along with a controlled maximum chip thickness, the cutting forces are controlled and provide a smooth cut. This keeps the cutting forces low and allows high axial depths of cut. Low Ae engagement improves stability and allows for higher feed rates, thus improving productivity and tool life. Additionally, low Ae and optimised tool paths enable increased feed rate and cutting speed. The overall result is a stable and reliable process which is much better for tool life. When rough milling in confined cavities, deep slots or hard materials and heat-resistant alloys, high-feed side milling is the preferred method. As the high-feed side milling method allows for the use of the complete cutting length of the end mill, a higher metal removal rate can be achieved with smaller diameters as compared to conventional milling strategies. This reduces tool costs, at the same time improves overall productivity, especially when using small machines.