The Nitronic 60 has become a popular choice in industries such as aerospace, automotive, petrochemical, medical devices, and other sectors due to its unique properties and performance under challenging conditions. This article will provide a comprehensive introduction to Nitronic 60 stainless steel material, including its chemical composition, properties (hardness, density, machinability, yield strength, etc.), equivalent, CNC machining, applications, and comparisons with 316 and other stainless steel materials.
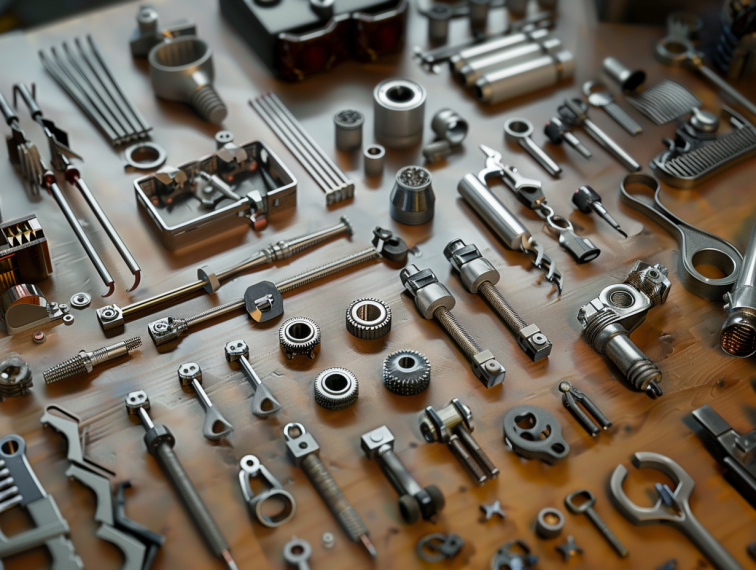
What is Nitronic 60 Material?
Nitronic 60, known by UNS S21800, is a nitrogen-alloyed austenitic stainless steel. Its official trade name is Nitronic 60, and it is sometimes also called 21CN-22Mn-5. It was developed by Allegheny Ludlum (now ATI Allegheny Ludlum) to provide better corrosion resistance than traditional 300 series stainless steels, while maintaining the good formability and weldability of austenitic stainless steels.
Nitronic 60 Chemical Composition
The chemical composition is key to Nitronic60’s properties. According to search results, the chemical composition of Nitronic60 typically includes:
- Carbon (C): ≤0.07%
- Chromium (Cr): 21.0-23.0%
- Nickel (Ni): 19.0-21.0%
- Molybdenum (Mo): 4.5-5.5%
- Nitrogen (N): 0.20-0.40%
- Manganese (Mn): ≤1.0%
- Silicon (Si): ≤0.50%
- Phosphorus (P): ≤0.04%
- Sulfur (S): ≤0.01%
The addition of nitrogen helps to increase strength and corrosion resistance, while reducing the tendency for intergranular corrosion.
Nitronic 60 Physical Properties
The physical properties of Nitronic60 are as follows
- Density: 7.62 g/cm3
- Melting point: Approximately 1390°C
- Thermal conductivity: Approximately 15.1 W/m·K at 100°C
- Coefficient of thermal expansion: Approximately 16.0 x 10^-6/°C within the range of 20-100°C
- Elastic modulus: Approximately 200 GPa
- Poisson’s ratio: Approximately 0.3
Nitronic 60 Mechanical Properties
The typical mechanical properties of Nitronic60 are as follows:
- Ultimate tensile strength (UTS): 724 MPa (105 ksi)
- Yield strength (0.2% PS): 379 MPa (55 ksi)
- Elongation: 35%
- Reduction in area: 55%
- Hardness: HBR 85
Nitronic 60 Key Advantages (Hardness, Yield Strength, Galling)
Nitronic 60 is called the hardest material mainly due to its outstanding properties: Yield strength, galling, corrosion resistance, etc. These traits make Nitronic 60 an excellent choice for specialized applications where regular stainless steel might falter. So we would like to discuss them in more detail here:
Hardness of Nitronic 60
The hardness of Nitronic 60 can vary based on the heat treatment and working conditions it undergoes. Typically, in the annealed condition, the hardness of Nitronic 60 is around:
– Rockwell B Hardness: Approximately 95 HRB
– Brinell Hardness: Approximately 170-200 HB
Hardness can be increased through cold working and strain hardening.
Yield Strength of Nitronic 60
The yield strength of Nitronic 60 is also dependent on the form and treatment of the steel. Generally, in the annealed condition, the yield strength is:
Yield Strength (0.2% offset): Approximately 50,000 – 60,000 psi (345 – 415 MPa)
This strength can be higher in cold-worked conditions, with yield strengths that can exceed these typical values.
Galling Resistance of Nitronic 60
One of the most significant properties of Nitronic 60 is its resistance to galling. Galling is a form of wear caused by adhesion between sliding surfaces. Nitronic 60 exhibits exceptional anti-galling properties, making it highly suitable for applications where metal-to-metal wear is a concern, such as:
- Shaft sleeves
- Valve stems
- Fasteners
- Bushings
This resistance is due to its unique chemical composition, particularly the higher silicon and manganese content, which enhances the material’s self-lubricity and hardness.
Corrosion Resistance of Nitronic 60
Another feature that makes Nitronic 60 stainless steel a high-performance material is its superior corrosion resistance. It can withstand erosion from corrosive media such as acids, bases and chlorides, making it highly useful in chemical, marine and pharmaceutical industries. This property extends the material’s lifespan, reducing maintenance and replacement needs and lowering costs.
High Temperature Stability of Nitronic 60
Nitronic 60 stainless steel performs excellently in high temperature environments, retaining its material properties. This makes it an ideal choice for high temperature applications such as heat exchangers, furnace fixtures and gas turbine components. Its high temperature stability means it can maintain strength and performance even at extreme temperatures, which is crucially important for many engineering applications.
Nitronic 60 Machinability
The machinability of Nitronic 60 is similar to that of conventional austenitic stainless steels, but due to its higher hardness, sharper tools or lower cutting speeds may be required.Anwayits machinability isstillexcellentin terms of the following parts:
- Good formability- Due to its austenitic structure, Nitronic60 has outstanding formability and is suitable for manufacturing complex parts.
- Excellent weldability- Nitronic60 maintains good corrosion resistance after welding and is less likely to develop heat-affected zone cracking.
- High strength- The nitrogen alloying effect enhances the strength of Nitronic60 while maintaining good ductility.
CNC Machining Nitronic 60
Machining Nitronic 60 can be challenging due to its hardness and work-hardening properties. Here are some insights from our experience with this material:
1. Preparing for Machining
Before machining, it’s crucial to set up the material correctly. For instance, if machining a part that is 2.356 inches long, extending the material to about 2.75 inches from the chuck allows ample space for the tooling without risk of collision.
2. Machining Parameters
Early experiences with Nitronic 60 required cautious speeds around 175-200 surface feet per minute (SFM). However, with advancements in tooling technology and technique adjustments, speeds can now reach 400-500 SFM, allowing for more efficient machining without compromising the integrity of the part.
3. Drilling and Finishing
Lowering the SFM during drilling (e.g., to about 350 SFM) helps in managing the heat and wear on the inserts. For finishing operations such as creating specific diameters or threadings, precise adjustments and checks are necessary to ensure the specifications are met. For example, a finishing pass might reduce by about 15 thousandths of an inch to achieve the desired diameter, ensuring tool pressure remains consistent for quality results.
4. Quality Control
After machining, it is crucial to inspect the part using appropriate tools, such as ring gauges for threads and micrometers for internal diameters. These inspections help confirm that the parts meet the tight geometric dimensioning and tolerancing (GD&T) requirements.
5. Second Operation (Op2)
For parts requiring tight tolerances, additional operations are often necessary. For instance, ensuring that the features machined in the first operation align perfectly with those in the second operation requires precise setup and real-time adjustments based on measurements.
6. Final Steps
After completing the machining processes, including drilling, threading, and boring, final inspections are crucial. These might include using a Coordinate Measuring Machine (CMM) to verify dimensions and ensure that the part meets all specified tolerances.
Nitronic 60 Applications
Given its mechanical properties and resistance to galling, Nitronic 60 is used in a variety of industrial products and applications including:
- Aerospace Industry
High Temperature Resistance: Nitronic 60 exhibits good performance in high-temperature environments, making it suitable for critical components in aviation engines and spacecraft.
Wear Resistance: In high-wear areas of aircraft, such as landing gear and bearings, Nitronic 60 is the preferred material due to its excellent wear resistance.
- Oil and Natural Gas Industry
Corrosion Resistance: The corrosion resistance of Nitronic 60 is particularly important when handling corrosive substances such as hydrogen sulfide.
Applications: Used in the manufacture of valves, pumps, and pipelines during oil and gas extraction and processing, especially in offshore platforms and high-sulfur environments.
- Medical Devices
Biocompatibility: The biocompatibility of Nitronic 60 makes it suitable for manufacturing medical devices, such as surgical tools and implants.
Wear Resistance: Its wear resistance plays an important role in manufacturing medical equipment that needs to maintain precision and functionality over time.
- Automotive Manufacturing
High-Strength Components: Nitronic 60 is used to manufacture high-stress automotive parts, such as gears and shafts.
Wear and Corrosion Resistance: These properties make Nitronic 60 an ideal material choice in automotive engines and exhaust systems.
- Food and Beverage Industry
Corrosion Resistance and Hygiene: When processing acidic and alkaline foods, the corrosion resistance of Nitronic 60 ensures long-term stability and hygiene safety of the equipment.
- Advances in Materials Science
Research and Innovation: Scientists are researching how to further enhance the performance of Nitronic 60 through fine-tuning of alloy compositions and advanced heat treatment processes.
New Application Areas: As technology advances, Nitronic 60 may find applications in more emerging fields, such as in renewable energy technologies and high-tech industries.
Nitronic 60 Products (Parts)
Here are some of the main products and forms in which Nitronic 60 is typically available:
- Helicoils (threaded inserts) – This is a type of threaded insert used to create stronger threads in metal and other materials, particularly useful in materials that are not inherently strong enough to hold a thread, or in applications where threads are subject to heavy wear. So Nitronic 60 Helicoils are widely used in Aerospace, Automotive, Oil & Gas, Marine and Medical Devices.
- Fasteners(Bolts, Nuts, and Screws) – These fasteners benefit from Nitronic 60’s resistance to galling and stress corrosion cracking, making them ideal for use in harsh environments.
- Fasteners(Studs and Threaded Rods) -Used extensively in petrochemical, aerospace, and marine environments where superior performance is required.
- Sheet and Plate – Employed in applications requiring flat surfaces with high corrosion resistance.Useful in the production of automotive valves, industrial processing equipment, and outdoor electrical enclosures.
- Valve Stems and Seats – The galling resistance of Nitronic 60 is particularly valuable for valve components, which require smooth operation without lubrication in corrosive environments.
- Ball Valves – Particularly in applications where they are subject to aggressive media.
- Wire – Used for welding Nitronic 60 materials and for producing mesh or filters. Also used in springs and other components requiring high strength and corrosion resistance.
- Pump Shafts – Used in pump shafts where strength and corrosion resistance are needed to handle both physical stresses and corrosive fluids.
- Wear Rings and Bushings – These pump components benefit from the high wear resistance of Nitronic 60, extending the lifespan of pump systems.
- Marine Chain and Fittings – For anchoring systems and deck hardware, its corrosion resistance ensures longevity and reliability.
- Seamless and Welded Pipe and Tubing – Applications include chemical and petrochemical processing equipment. Often used in pulp and paper industry components.
- Forgings – Custom shapes for specialized components. Used in industrial machinery and high-strength applications.
- Mixers, Blades, and Cutters – The corrosion resistance of Nitric 60 ensures that it does not contaminate food products and can withstand cleaning chemicals.
- Specialty Components – Designed for specific applications where the unique properties of Nitronic 60, such as resistance to wear, galling, and corrosion, are necessary.
Nitronic 60 Equivalent Materials
While there are no exact equivalents to Nitronic 60 due to its unique composition and properties, there are several other materials with similar characteristics that might be considered depending on the specific requirements of the application:
- AISI 316 Stainless Steel: While not as wear-resistant as Nitronic 60, AISI 316 offers good corrosion resistance and is widely used in the chemical and marine industries. It is more readily available and could be considered for less demanding applications.
- 17-4 PH Stainless Steel: This is a martensitic precipitation-hardening stainless steel that provides an excellent combination of high strength, good corrosion resistance, and good mechanical properties at temperatures up to 600°F (316°C).
- AISI 304 Stainless Steel: Similar to AISI 316 but generally less resistant to corrosion. It is another commonly used austenitic stainless steel.
- Duplex Stainless Steel (e.g., 2205): This offers higher strength and better corrosion resistance than most standard austenitic grades like 304 and 316. It could be a viable alternative in environments where strength and corrosion resistance are paramount.
- Custom 450 and Custom 455: These are martensitic stainless steels that have been age-hardened. They offer good corrosion resistance and high strength with excellent toughness.
Nitronic 60 vs 304/360 Stainless Steel, Differences Between Them
Nitronic 60 is an austenitic stainless steel known for its superior strength and excellent resistance to wear and galling, compared to other stainless steels like 304 and 316. Here’s a detailed comparison of Nitronic 60 with these and other commonly used stainless steels:
Nitronic 60 vs. 304 Stainless Steel
- Corrosion Resistance: Both Nitronic 60 and 304 have good corrosion resistance, but 304 is generally more vulnerable to pitting and corrosion in chloride environments. Nitronic 60 offers better overall resistance in various corrosive environments.
- Strength and Hardness: Nitronic 60 has a significantly higher yield strength, nearly twice that of 304, which makes it more suitable for applications requiring durability and resistance to wear and fatigue.
- Galling Resistance: Nitronic 60 is highly resistant to galling, even with minimal lubrication, which is a significant advantage over 304 stainless steel. This makes it ideal for applications involving repeated assembly and disassembly.
- Cost: 304 stainless steel is generally less expensive and more widely available than Nitronic 60.
Nitronic 60 vs. 316 Stainless Steel
- Corrosion Resistance: Both 316 and Nitronic 60 offer excellent corrosion resistance, with 316 being preferable in severely corrosive environments such as marine conditions due to its addition of molybdenum. However, Nitronic 60 is better suited for environments where both strength and corrosion resistance are required.
- Strength and Hardness: Similar to the comparison with 304, Nitronic 60 has a higher strength and hardness than 316, making it more suitable for high-stress applications.
- Galling Resistance: Nitronic 60 exceeds 316 in terms of resistance to galling, which is critical in applications like threaded components.
- Cost: 316 is generally more expensive than 304 but typically less costly than Nitronic 60, depending on the form and quantity purchased.
General Comparison with Other Stainless Steels
- Durability: Nitronic 60 stands out for its blend of strength, ductility, and durability compared to other stainless steels, which often excel in one area but fall short in others.
- Application Specificity: While 304 and 316 stainless steels are versatile and used across a wide range of applications, Nitronic 60 is often chosen for specific applications where high strength and excellent wear resistance are crucial.
- Magnetic Properties: Like most austenitic stainless steels, Nitronic 60 is non-magnetic, which is advantageous in applications where magnetic interference must be avoided.
Overall, Nitronic 60 offers benefits that standard stainless steels cannot match. This makes it particularly valuable in industries such as aerospace, naval, automotive, and any sector requiring reliable performance in harsh conditions. If you are looking for high quaity Nitronic 60 Machined Parts, contact us now!