Have you ever wondered how two materials can be joined together when you can only reach one side? That’s where a pop rivet comes in. Pop rivet is not just a simple fastener, it’s a well-engineered solution that makes it possible to join materials securely and efficiently, even when access is limited. So in this guide, let’s talk about this popular but unique fastener in detail by going over its work principle, types, applications, and metric/imperial standard pop rivet size chart in different materials and head styles!
What is a Pop Rivet?
A pop rivet, also known as a type of blind rivet or hollow rivet, is a strong permanent mechanical fastener with a mandrel through its center, designed for clamping two pieces of material together. They are generally used in applications where there is limited to no access on the rear side, or sometimes called the blind side. The reason they have the name pop rivet is because the name “Pop” was the original brand that invented this amazing invention. Pop rivets are commonly used to fasten sheet metal or plastic, but can also be used for things like wood or leather. Also, CNC machining manufacturers, including Junying, insert the blind pop rivets into drilled holes made in parts intended for joining.
Pop Rivet Structure & How To Make?
Pop Rivets consist of two parts, the shank (rivet body) and the mandrel. The rivet body is hollow and features a flared end, while the mandrel is a long, thin rod that runs through the center of the rivet body.
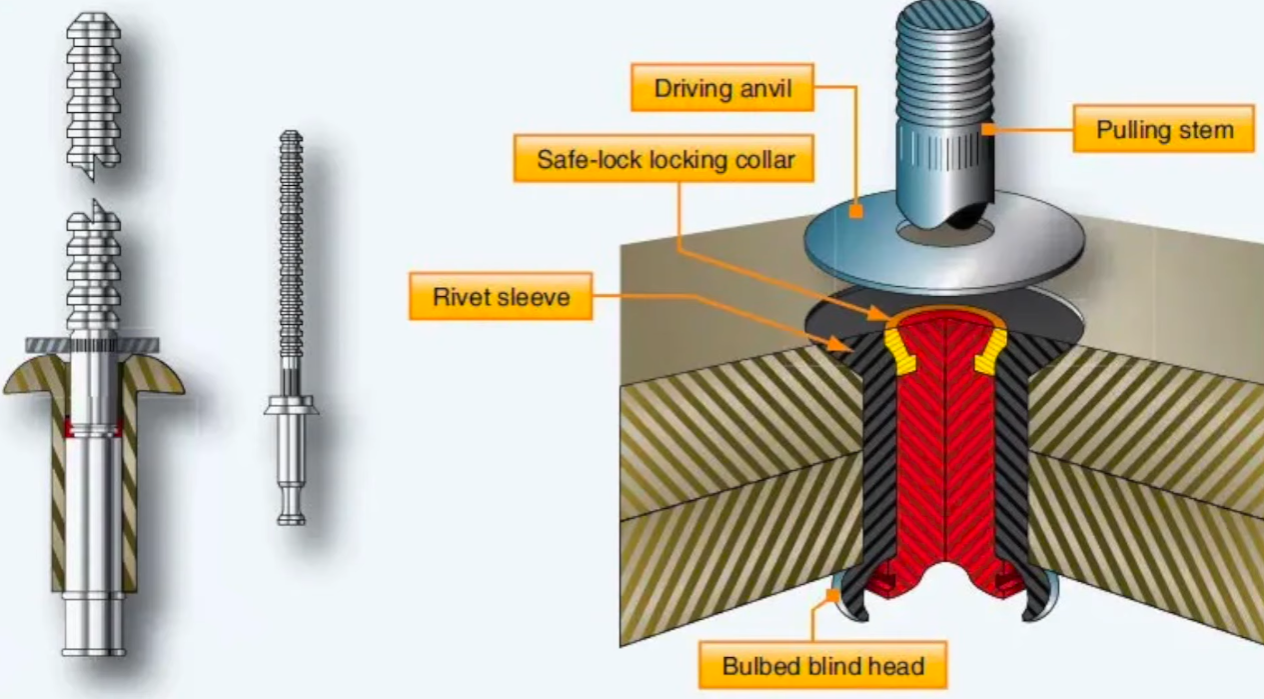
The manufacturing process of a pop rivet is quite interesting. It begins with a metal rod that is cut to the desired length. This rod is then shaped into the rivet body using a dye that forms the head of the rivet. This shaping is often done through a method called cold forming ,meaning the metal is shaped without any heat. After forming, the rivet body is hollowed out to fit the mandrel. The mandrel is also made from metal and is specifically designed to break off once the rivet is installed.
How Does a Pop Rivet Work?
The pop rivet (the thicker and bulkier side) is inserted into a hole drilled through two materials, and then, without having any access to the other side of the materials, a rivet gun is used to pull the top of the mandrel, expanding the shank. As the shank expands, pull on the mandrel to trap the two materials together. The force from the gun then slaps off the mandrel hand at the pre-made break point. It’s called a pop rivet also because of the sound the hand tool makes when it snaps off the mandrel. It is a great invention if you do need to tie two bits of mats together where you can’t access the other side of the material, the workspace you’re working on.
Pop Rivet Types & Uses
When it comes to pop rivets, they are also made in lots of different materials and structures:
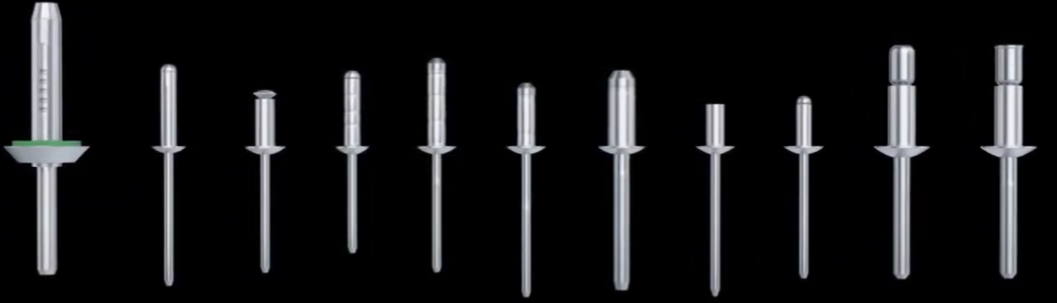
Pop Rivet Types in Materials
The use of materials determines the performance of a standard pop rivet, and then determines the application requirements and environmental conditions it meets. Therefore, we first classify pop rivets based on commonly used materials:
- Aluminum Pop Rivet: Lightweight and corrosion-resistant, these are typical blind rivets suitable for common applications.
- Steel & Stainless Steel Pop Rivet: Offers greater strength. Stainless variants are used when corrosion resistance is important.
- Copper/Brass Pop Rivet: Often used in roofing, soffits, and downspouts. These rivets are visually appealing and durable.
- Zinc Plated Pop Rivet: Provides a layer of protection against rust and is used where a finish is needed.
- Plastic Pop Rivet: Particularly suitable for joining soft materials such as other plastics, urethane, and rubber.
Pop Rivet Types in Head & Body Structure Styles
POP rivets are usually made of aluminum alloy and are widely used because of their lightness, corrosion resistance and easy processing. However, different materials can also be selected, such as steel, stainless steel, etc., to adapt to different environments and requirements. To ensure the most reliable fastening, the material of the rivet is only the basis for selection, and the head, body mandrel, and specific structure must be taken into consideration. Therefore, a variety of special pop rivets are designed and produced based on this to meet the needs of various industries. Here we explain the differences between each type of pop rivet and their applications:
Dome Pop Rivets (Standard)
Dome Pop Rivets are the most popular and widely used standard pop rivets. The domed head style offers an excellent bearing surface and is ideal for a number of different applications. The dome pop rivet has one-sided installation capability and is generally produced to the international DIN standard. This type of blind rivet is widely used in assembly applications, including the heating and air conditioning, containers, metal cladding and isolation, the furniture industry, and domestic appliances.
Open-End Pop Rivets
Open End Pop Rivets are hollow body rivets that achieve tight connections at low cost, making them the most popular and cheapest pop rivet. However, the hollow body means that this rivet cannot withstand excessive loads, so it is often used in light devices such as decorative metal, plastic, and wood mats. However, a variety of head styles, such as large flange, dome head, and countersunk head, can be adopted by open-end pop rivets, increasing their applications in machinery, automobiles, furniture, and construction industries.
Countersunk Pop Rivets (Flush Pop Rivets)
Countersunk rivets feature a conical head that allows them to sit flush with the surface of the material. This type is often used in applications where a smooth finish is required, such as in automotive and aerospace industries.
Closed End Pop Rivets (Sealed Pop Rivets)
Closed end rivets, commonly called sealed rivets, have a blind hole, one-sided installation capability and a unique cup-shaped end configuration. They seal tightly, preventing passage of vapor or liquid around or through the set rivet. Closed end rivets offer 23% greater tensile strength than equivalent open-end rivets. Closed end pop rivets offer the benefits of enhanced tensile and shear strength over corresponding open end rivets. Sealed rivets provide 100% mandrel retention, deliver vibration resistant joints and excellent hole fill characteristics. Their solid end prevents water from entering the rivet, providing a secure and leak-proof joint, so own widely assembly applications include white goods, electronic enclosures, signs, outdoor cases, scoreboards, LED signs, and recreational vehicles.
Large Flange Pop Rivets
Large flange rivets have a wider head, distributing the pressure load over a much larger area, that makes them ideal for situations where additional strength is needed, such as in structural applications or when fastening thin materials. The large flange pop rivet is allowed to design flexibility, reduced inventory, and resultant cost savings; tolerant of oversized holes, the rivet body expands radially when setting. They can be used for attaching soft or brittle material to a rigid backing, also good for joining material with pre-punched or drilled holes. Larg flange with mult grip ususally offer three times the grip range of standard rivets, used when different thicknesses of materials need to be joined!
Multi Grip Pop Rivets
Multi grip rivets are versatile and can accommodate a range of material thicknesses. They are designed to work effectively in situations where the thickness of the materials being joined varies, providing a secure hold. Multi-grip pop rivets come with a wide grip range and accommodate oversized holes, so they are ideal in applications where hold diameters are not exact, and you’re lookming for a reivet that provides for a wide grip range.
Interlock Grooved Pop Rivets (Heavy Duty Blind Rivet)
Grooved pop rivets have a special interlock structure, provide a strong connection into dense materials, are engineered for high-strength assembly applications, include flight cases, wood and industries that utilise plastic. Their exceptional mechanical interlocking is suitable for heavy-duty construction and industrial uses, materials including wood, concrete and plasyic can easily bne fastened with a grooved rivets.
Peel Pop Rivets
Peel rivets work on the basis of the blind sied of the peel rivet breaks into four petals pulling the substrate layers tight together as the rivet peels and clamps. This type of rivets has a special mandrel constrauction that spreads load over a wide area, for application into soft materials such as wood, insulation, plastics, and plasterboard.
Tri-Fold Exploding Pop Rivets
Tri-fold reivets expand into three legs on the blind side, creating a strong grip, especially in oversized holes or soft materials. These types of pop rivets are often used with backup washers for added strength. These slotted or open rivets create a propeller-shaped anchor on the blind side of a material without damaging it, and they are designed to assemble lightweight materials such as fiberglass, plastics, and composites.
Pop Rivet Sizes (Diameters, Grip Range & Length, Drill Hole, Strength)
Once you know which pop rivet to choose for your linking and fastening, then what you’re going to do is determine what size rivet you want to use for your project. It’s a couple of different ways to look at rivets, not only the diameter, the thickness of the shaft, but also the length of the rivet itself. So, depending on how thick the two pieces of material you’re joining together are, you must look at the diameter and thickness of the rivet you’re going to use.
Here are the main dimensions of pop rivets:
- Rivet Diameter – Is the roundness of the rivet body, it can also be designated by it’s rivet size number.
- Predrill Hole Size – The size that will need to be predrilled to make sure rivet will be properly seated when fastening materials.
- Grip Range – Thickness range of materials the rivet can fasten (in inches)
- Grip Length (Rivet Body Length) – The thinckness of material(s) a rivet can effectively fasten. Example: you are attaching two 1/4″ pieces of metal together, they will require a pop rivet with a minimum grip of at least a 1/2″.
In order to help you quickly get the sizes of common blind pop rivets on the market, we have summarized the following two tables covering the most commonly used head styles and materials:
Metric Standard Pop Rivet Size Chart in MM (Aluminium/Stainless Steel/Steel)
Includes: Head Type, Rivet Size, Rivet Diameter, Grip Range, Body Length, Drill/Hole Size, Tensile, Shear, Material Options
Head Type | Rivet Size | Rivet Diameter | Grip Range (mm) | Body Length (mm) | Hole Size (mm) | Material Options |
---|---|---|---|---|---|---|
Dome Head | 2.4 mm | 2.4 mm | 0.5 – 3.2 | 6.4 | 2.5 | Al/Al, St/St, SS/St, SS/SS |
3.2 – 6.4 | 9.5 | |||||
6.4 – 9.5 | 12.7 | |||||
Dome Head | 3.2 mm | 3.2 mm | 0.5 – 1.6 | 5.4 | 3.3 | Al/Al, St/St, Al/St, SS/St, SS/SS, Cu/St, Cu/Br |
1.6 – 3.2 | 6.9 – 7.0 | |||||
3.2 – 4.8 | 8.6 | |||||
4.8 – 6.4 | 10.2 | |||||
6.4 – 7.9 | 13.3 | |||||
7.9 – 9.5 | 16.5 | |||||
9.5 – 12.7 | 19.1 | |||||
12.7 – 15.9 | 20.3 | |||||
Dome Head | 4.0 mm | 4.0 mm | 1.6 – 3.2 | 7.6 | 4.1 | Al/Al, St/St, Al/St, SS/St, SS/SS |
3.2 – 4.8 | 9.2 | |||||
4.8 – 6.4 | 10.8 | |||||
6.4 – 9.5 | 13.3 | |||||
9.5 – 12.7 | 16.5 | |||||
12.7 – 15.9 | 19.1 | |||||
Dome Head | 4.8 mm | 4.8 mm | 0.5 – 3.2 | 12.7 | 4.9 | Al/Al, St/St, Al/St, SS/St, SS/SS |
3.2 – 6.4 | 16.0 | |||||
6.4 – 9.5 | 19.1 | |||||
9.5 – 12.7 | 22.2 | |||||
12.7 – 15.9 | 25.4 | |||||
15.9 – 19.1 | 28.6 | |||||
19.1 – 22.2 | 31.8 | |||||
22.2 – 25.4 | 31.8 | |||||
Dome Head | 6.4 mm | 6.4 mm | 3.2 – 6.4 | 12.7 | 6.5 | SS/SS |
6.4 – 9.5 | 16.0 | |||||
9.5 – 12.7 | 19.1 | |||||
12.7 – 15.9 | 22.2 | |||||
15.9 – 19.1 | 25.4 | |||||
19.1 – 22.2 | 28.6 | |||||
22.2 – 25.4 | 31.8 | |||||
Large Flange | 3.2 mm | 3.2 mm | 0.5 – 3.2 | 7.0 | 3.3 | Al/Al, St/St, Al/St, SS/St |
3.2 – 6.4 | 10.2 | |||||
6.4 – 9.5 | 13.3 | |||||
Large Flange | 4.0 mm | 4.0 mm | 4.8 – 6.4 | 9.6 | 4.1 | Al/Al, St/St, Al/St, SS/St |
6.4 – 9.5 | 12.8 | |||||
Large Flange | 4.8 mm | 4.8 mm | 3.2 – 6.4 | 11.4 | 4.9 | Al/Al, St/St, Al/St, SS/St |
6.4 – 9.5 | 14.6 | |||||
9.5 – 12.7 | 17.8 | |||||
12.7 – 15.9 | 20.3 | |||||
15.9 – 19.1 | 24.0 | |||||
19.1 – 22.2 | 27.3 | |||||
22.2 – 25.4 | 32.4 | |||||
Large Flange | 6.4 mm | 6.4 mm | 3.2 – 6.4 | 11.4 | 6.5 | SS/SS |
6.4 – 9.5 | 14.6 | |||||
12.7 – 15.9 | 20.3 | |||||
15.9 – 19.1 | 24.1 | |||||
Countersunk | 2.4 mm | 2.4 mm | 0.8 – 3.2 | 7.0 | 2.5 | Al/Al, St/St |
3.2 – 4.8 | 8.6 | |||||
Countersunk | 3.2 mm | 3.2 mm | 1.6 – 3.2 | 7.0 | 3.3 | Al/Al, St/St, Al/St, SS/St, SS/SS |
3.2 – 4.8 | 8.6 | |||||
4.8 – 6.4 | 10.2 | |||||
6.4 – 7.9 | 11.7 | |||||
Countersunk | 4.0 mm | 4.0 mm | 3.8 – 6.4 | 11.4 | 4.1 | Al/Al, St/St, SS/St |
Countersunk | 6.4 mm | 6.4 mm | 4.8 – 6.4 | 11.4 | 6.5 | SS/St |
Imperial Standard Pop Rivet Size Chart in Inches (Aluminium/Stainless Steel/Steel)
Includes: Head Type, Rivet Size, Rivet Diameter, Grip Range, Body Length, Drill/Hole Size, Tensile, Shear, Material Options
Head Type | Rivet Size | Rivet Diameter | Grip Range (in) | Body Length (in) | Drill/Hole Size | Tensile (lbs) | Shear (lbs) | Material Options |
---|---|---|---|---|---|---|---|---|
Dome | 3/32 | 0.094 | .020–.125 | .250 | #41 (.097–.100) | 135–170 | 85–130 | Al/Al, St/St, Al/St, SS/St, SS/SS |
.126–.250 | .375 | |||||||
.251–.375 | .500 | |||||||
Dome | 1/8 | 0.125 | .020–.062 | .212 | #30 (.129–.133) | 220–310 | 170–260 | Al/Al, St/St, Al/St, SS/St, SS/SS, Cu/St, Cu/Br |
.063–.125 | .275 | |||||||
.126–.187 | .337 | |||||||
.188–.250 | .400 | |||||||
.251–.312 | .462 | |||||||
.313–.375 | .525 | |||||||
.376–.500 | .650 | |||||||
.501–.625 | .736–.775 | |||||||
Dome | 5/32 | 0.156 | .063–.125 | .300 | #20 (.160–.164) | 350–470 | 225–370 | Al/Al, St/St, Al/St, SS/St, SS/SS |
.126–.187 | .362 | |||||||
.188–.250 | .425 | |||||||
.251–.375 | .550 | |||||||
.376–.500 | .675 | |||||||
.501–.625 | .800 | |||||||
Dome | 3/16 | 0.188 | .020–.125 | .325 | #11 (.192–.196) | 500–1300 | 315–1150 | Al/Al, St/St, Al/St, SS/St, SS/SS |
.126–.250 | .450 | |||||||
.251–.375 | .575 | |||||||
.376–.500 | .700 | |||||||
.501–.625 | .825 | |||||||
.626–.750 | .950 | |||||||
.751–.875 | 1.075 | |||||||
.876–1.000 | 1.200 | |||||||
Dome | 1/4 | 0.250 | .125–.250 | .500 | F (.257–.261) | 750–2100 | 600–1700 | Al/Al, St/St, Al/St, SS/SS |
.251–.375 | .625 | |||||||
.376–.500 | .750 | |||||||
.501–.625 | .875 | |||||||
.626–.750 | 1.000 | |||||||
.751–.875 | 1.125 | |||||||
.876–1.000 | 1.250 | |||||||
Large Flange | 1/8 | 0.125 | .020–.125 | .275 | #30 | 220–310 | 170–260 | Al/Al, St/St, Al/St, SS/St |
.126–.250 | .400 | |||||||
.251–.375 | .525 | |||||||
Large Flange | 5/32 | 0.156 | .188–.250 | .379 | #20 | 350–470 | 225–370 | Al/Al, St/St, Al/St, SS/St |
.251–.375 | .504 | |||||||
Large Flange | 3/16 | 0.188 | .020–.250 | .450 | #11 | 500–1300 | 315–1150 | Al/Al, St/St, Al/St, SS/St |
… up to 1.125 | up to 1.277 | |||||||
Large Flange | 1/4 | 0.250 | .251–.375 | .635 | F | 750–1240 | 600–1000 | Al/Al, St/St, Al/St |
.376–.500 | .760 | |||||||
Countersunk | 3/32 | 0.094 | .032–.125 | .275 | #41 | 130–170 | 85–130 | Al/Al, St/St |
Countersunk | 1/8 | 0.125 | .063–.125 | .275 | #30 | 220–310 | 170–260 | Al/Al, St/St, Al/St, SS/St, SS/SS |
.126–.187 | .337 | |||||||
.188–.250 | .400 | |||||||
.251–.312 | .462 | |||||||
Countersunk | 5/32 | 0.156 | .188–.250 | .425 | #20 | 350–470 | 225–370 | Al/Al, St/St, Al/St |
Countersunk | 3/16 | 0.188 | .126–.250 | .450 | #11 | 500–1300 | 315–1150 | Al/Al, St/St, SS/St, SS/SS |
Countersunk | 5/16 | 0.313 | .151–.250 | .450 | #11 | 1300 | 1150 | SS/St |
How To Choose the Right Pop Rivet Size for Your Project?
To select the correct rivet size for your project, the first important things is choose the right length. Now that length of the pop rivet you need is going to be determined by the two pieces of material. And the easiest way to know which one to choose is when you put the two pieces of material together, the rivet should extend past both of those pieces of material then you know you have the right length. As a rule of thumb, the rivet length should be about 1.5 times the thickness of the material being fastened, ensuring adequate expansion on the blind side.
You also need to look into “grip range”, as there is a minimum and maximum range that is dependent upon the rivet diameter and length, make sure the total material thickness is within the rivet’s grip range. For example: A rivet with a grip range of 0.020″ to 0.125″ is suitable for materials with a combined thickness in this range.
After that you need to drill a corresponding hole for the size of the rivet you’re using. For example, for an 8 inch diameter rivet, we are going to use the appropriate one to go into the two pieces of material, and then use the rivet gun to squeeze it together one more time and it snaps off the shaft and you’ve just riveted two pieces of material together using the correct rivet.
If you are purchasing pop rivets to fit material that has already been drilled, focus on the diameter when selecting the size. The rivet’s body (or shell) diameter must fit snugly into the drilled hole. A hole that is too large can lead to a loose connection, while a hole that is too small may prevent the rivet from fitting. Generally, the drilled hole should be slightly larger than the rivet’s body diameter. for example: A 1/8″ (3.2 mm) diameter rivet fits a drilled hole of about 0.129″ to 0.133″.