There are various types of aluminum alloys, but A6063 and A6061 are alloys that excel in corrosion resistance. Both A6063 and A6061 are classified as 6000 series aluminum alloys, and it is important to use different materials according to the application. In this article, we will explain in detail the differences and applications of A6063 and A6061, so if you are looking to deepen your knowledge of materials and apply it to your work, please be sure to read to the end.
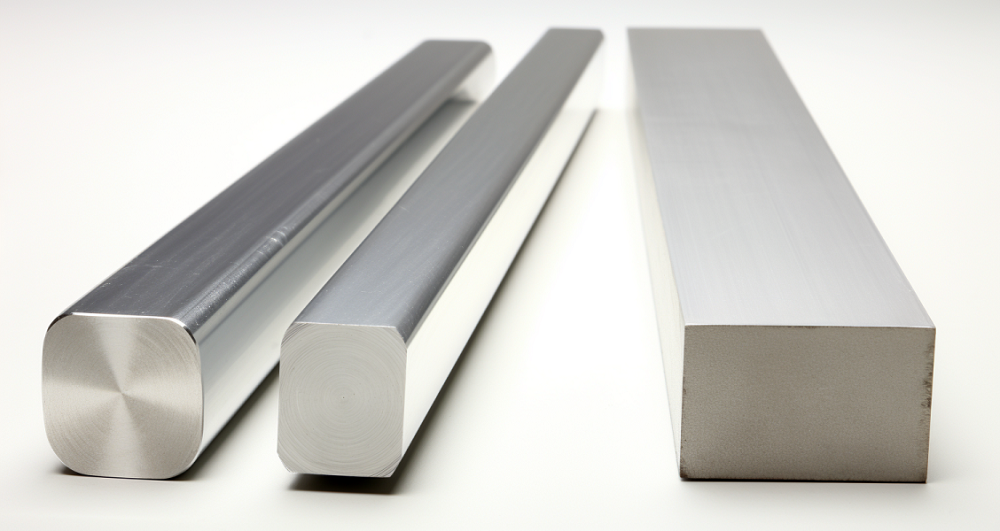
Both 6061 aluminum and 6063 are impressive aluminum alloys in their respective domains. They share nearly all the properties that the 6xxx aluminum series possesses. Both are grades of aluminum alloys used in extrusion. Before resolving the issue of “how to choose,” we will consider each series in turn.
What is 6061 Aluminum?
Aluminum 6061 is a member of the 6000 series of aluminum alloys. It contains a significant amount of both magnesium and silicon in its composition. This alloy is primarily formulated for forged products. For various regional benefits, 6061 aluminum is designated as ENAW-6061 in European standards. The AFNOR (French) designation for aluminum 6061 is A-G1SUC, although in older literature it is CSAGS11N.
Aluminum 6061 has been on the market since 1935 and received its standard designation in 1954. It is one of the most versatile heat-treatable alloys with a wide range of different alloy compositions. 6061 aluminum is common for multi-purpose applications due to its combination of strength and corrosion resistance, as well as its advanced weldability. It is used in a variety of applications, from the aviation industry and marine industry to the automotive industry.
What is 6063 Aluminum?
Aluminum 6063 is a member of the 6000 series of aluminum alloys. It is often called architectural aluminum because it is the best choice for building materials. Aluminum 6063 is designated in the British Standard (BS) as H9 and in European standards as ENAW-6063. The EN chemical designation for 6063 aluminum is AlMg0.7Si.
Aluminum 6061 has been on the market since 1944 and received its standard designation in 1954. Aluminum 6063 is widely used for drawing constant section shapes due to its excellent response to extrusion. Examples of such shapes include tubes, bars, and others. It is known for its high corrosion resistance and good surface finish. Its main elemental composition includes Al, Mg, and Si in descending order of quantity. Although aluminum 6063 is not different from aluminum 6061, it is well-suited for extrusion due to its higher corrosion resistance and lower strength.
What are the Differences Between Aluminum 6061 and Aluminum 6063?
Aluminum 6061 and Aluminum 6063 are popular aluminum alloys that offer a wide range of benefits in manufacturing. These six grades of aluminum alloy fall under the 6061xxxx series of aluminum alloys. Aluminum 6063 and 6 originate from the XNUMXxxxx series, hence, they share similar elemental composition and mechanical properties. For this reason, it can be very difficult for manufacturers to distinguish between the two alloys.
However, to differentiate each alloy for its intended use, one must employ their respective characteristics. This makes it much easier to use the best-suited alloy for one’s project. To help readers determine between the two alloys, we will use the following factors for comparison:
6061 vs 6063 Aluminum: Alloy Grade Series
6061 aluminum and 6063 aluminum exist in different forms. Although both alloys derive from the 6000 series alloy, they retain distinct characteristics. These individual properties can be used to make a comparison. In this section, we distinguish 6061 aluminum from 6063 aluminum by listing the variations of each alloy.
6061 Aluminum Alloy Grade Types
The 6061 aluminum alloy exists in pre-tempered and tempered grades. They include:
- 6061-O aluminum
- 6061-T1 aluminum
- 6061-T4 aluminum
- 6061-T42 aluminum
- 6061-T451 aluminum
- 6061-T4510 aluminum
- 6061-T4511 aluminum
- 6061-T51 aluminum
- 6061-T6 aluminum
- 6061-T62 aluminum
- 6061-T651 aluminum
- 6061-T6510 aluminum
- 6061-T6511 aluminum
- 6061-T652 aluminum
- 6061-T89 aluminum
- 6061-T94 aluminum
6063 Aluminum Alloy Grade Types
Aluminum 6063 exists in about 13 alloy variations. They include:
- 6063-0 aluminum
- 6063-T1
- 6063-T4
- 6063-T42
- 6063-T5
- 6063-T52
- 6063-T6
- 6063-T62
- 6063-T66
- 6063-T8
- 6063-T83
- 6063-T831
- 6063-T832
6061 vs 6063 Aluminum: Chemical Composition
You can perform a comparison using the chemical composition of both alloys. While these chemical compositions may be the same, the percentage compositions differ.
The table below provides an overview of the alloy compositions for 6061 aluminum and 6063 aluminum.
Element | 6061 Aluminum | 6063 Aluminum |
Aluminum | 95.85 – 97.70% | 97.50 – 99.40% |
Silicon | 0.40 – 0.80% | 0.20 – 0.60% |
Zinc | 0.00 – 0.25% | 0.00 – 0.10% |
Magnesium | 0.80 – 1.20% | 0.45 – 0.90% |
Manganese (Mn) | 0.00 – 0.15% | 0.00 – 0.10% |
Chromium | 0.04 – 0.35% | 0.00 – 0.10% |
Copper | 0.15 – 0.40% | 0.00 – 0.10% |
Iron (Fe) | 0.00 – 0.70% | 0.00 – 0.35% |
Titanium (Ti) | 0.00 – 0.15% | 0.00 – 0.10% |
Residuals | 0.00 – 0.15% | 0.00 – 0.15% |
6061 vs 6063 Aluminum: Mechanical Properties
The mechanical properties include the physical attributes that a material possesses. In this case, both alloys belong to the same series (Aluminum 6000 series). By examining physical properties, it becomes much easier to differentiate each alloy. The following properties are used to draw a comparison between the two alloys.
Machinability
This is a measure of how a material performs when subjected to machining operations such as milling, turning, die casting, etc. A qualitative measurement has been used to get an overall reaction to machining. The measure of machinability for each is in the form of a Likert scale, which includes poor, fair, good, and excellent. Our findings suggest that 6061 aluminum has superior machinability compared to 6063. If the primary concern for the proposed project is machinability, then 6061 aluminum is preferred over 6063 aluminum. 6063 aluminum is machinable as well, but it is better known as an extrusion alloy.
Density
The density of these aluminum alloys typically falls within the range of approximately 2.68 to 2.70 grams per cubic centimeter (g/cm³) at room temperature. While there might be slight differences in density due to the different alloying elements and the amounts present, these differences are generally minimal and often considered negligible for most practical applications. Both 6061 and 6063 aluminum alloys are known for their good strength-to-weight ratio, which is a key characteristic of aluminum and its alloys.
Yield Strength
The yield strength of 6061 aluminum is significantly higher than that of 6063 aluminum. For this reason, for projects that require strength, such as the manufacture of firearm parts or bicycle frames, most people choose 6061 aluminum over 6063 aluminum.
Tensile Strength
6061 and 6063 aluminum alloys are two of the most commonly used aluminum grades, and they have different mechanical properties that make them suitable for various applications. One key property where they differ is tensile strength: 6061 Aluminum typically has a higher tensile strength compared to 6063. 6061 aluminum can have a tensile strength ranging from 20,000 to 42,000 psi (pound-force per square inch), depending on the temper (heat treatment condition). For example, 6061-T6, one of the most commonly used tempers, has a tensile strength of about 42,000 psi. 6063 Aluminum generally has lower tensile strength than 6061. The tensile strength for 6063 aluminum also varies depending on the temper, but it’s usually around 8,000 to 30,000 psi. For instance, 6063-T6 temper might have a tensile strength around 30,000 psi.
Fatigue Resistance
Fatigue resistance reflects how a material can endure repeated stress over time without failing. When it comes to enduring the stresses of fluctuating loads, 6061 aluminum outperforms 6063 aluminum. This property is particularly valuable for components in the aerospace and maritime industries, where materials are regularly subjected to varying stress cycles. Therefore, 6061 aluminum becomes the preferred choice for parts in aircraft and vessels that experience these conditions.
Bearing Yield Strength
Bearing yield strength is essentially how well a material can handle stress in scenarios where components are joined, such as when two plates are fastened together. It represents the peak stress that a material can absorb without cracking at the joints under pressure. This attribute is especially relevant for construction applications like scaffolding. Given its superior bearing yield strength, 6061 aluminum alloy is more suitable than 6063 for applications requiring robust joint performance.
Material Hardness
This is a measure of ductility, general material strength, and surface quality. Here we have used the Brinell hardness, a common measurement system for metals. Based on metrics, the Brinell hardness values for 6061 aluminum and 6063 aluminum are respectively 95 and 73. It is important to know that the 6061 alloy is strong with enough ductility to be formed. However, if hardness is the main concern for the project, 6061 aluminum is recommended.
Overall Material Strength
The overall strength of a material is a combination of many factors. These factors include yield strength, ultimate strength, shear strength, and fatigue strength, among others. For reference, we have come up with empirical indexes that show the exact strengths of both alloys for comparison. Overall, 6061 aluminum has higher metrics and may be preferred over 6063 aluminum. For more details, please refer to the summary table of mechanical properties.
6061 vs 6063 Aluminum Mechanical Properties Compare Table
Property | 6061 Aluminum | 6063 Aluminum |
Units | Metric | Metric |
Shear Modulus | 25.9 GPa | 26.0 GPa |
Elastic Modulus | 70.3 GPa | 68.0 GPa |
Fatigue Strength | 58–110 MPa | 39–95 MPa |
Shear Strength | 84–210 MPa | 70–190 MPa |
Tensile Yield Strength | 76–370 MPa | 49–270 MPa |
Ultimate Strength | 310 MPa | 241 MPa |
Thermal Conductivity | 167 W/mK | 190–220 W/mK |
Hardness | 95 | 73 |
Machinability | Good | Fair |
Surface Quality | Fair | Good |
Extrudability | Good | Excellent |
Workability | Fair | Good |
Weldability | Good | Good |
6061 and 6063 Aluminum: Applications
Understanding the key properties of 6061 and 6063 aluminum is invaluable in understanding how each alloy fits in the diverse world of aluminum applications.
6061 Aluminum Applications
Aluminum 6061 is widely used in the industry for general purposes due to its weldability and formability. In fact, because of its corrosion resistance and high strength, 6061 aluminum is applied in fields such as construction, structure, and the automotive industry. The applications of 6061 aluminum are comprehensive, but its main uses include:
- Aircraft and truck frames
- Chemical equipment
- Electronic components
- Fasteners
- Furniture
- Heat exchangers
- Electrical appliances
- Heat sinks
- Marine frames
- Welding assemblies
6063 Aluminum Applications
Aluminum 6063 is commonly used in extrusion projects due to its weldability, excellent workability, and moderate strength. Therefore, aluminum 6063 is considered ‘architectural aluminum’ due to its combination of strength, weldability, and machinability. 6063 aluminum has a variety of applications, such as:
- Architectural products
- Extrusions for construction and building
- Furniture
- General extrusions for medical, automotive, parts profiling, etc.
- Piping
- Recreational equipment
- Tubing
6061 vs 6063 Aluminum: Price Per Pound
The price of aluminum alloys such as 6061 and 6063 can fluctuate based on a variety of factors such as market demand, the cost of raw materials, processing fees, supply chain conditions, and economic events. Generally, the prices for these metals are not fixed and can vary daily.
However, as a rough generalization:
6061 Aluminum is often more expensive than 6063 due to its higher strength and its versatility in a wider range of applications. Its greater strength and machinability can add to its cost, making it typically the more costly option between the two.
6063 Aluminum is usually less expensive than 6061 because it is easier to extrude and has a lower strength, which may make it cheaper to produce. It is often used in applications where high strength is not required but a good surface finish is important.
Please note that these are general tendencies and actual prices can only be determined by current market conditions and supplier pricing. For the most accurate and up-to-date pricing, you would need to check with metal suppliers, commodity price listings, or manufacturers who can provide quotes based on current market rates. Keep in mind that prices are also affected by the quantity being purchased, the form of the aluminum (e.g., sheet, plate, bar, tube), and any additional processing or services required.
Aluminum Alloy 6061 or 6063: Which is Superior, Which To Choose?
Finally, in this blog post, we were able to compare and contrast 6061 aluminum with 6063 aluminum. However, it is important to note that each of these aluminum alloy grades is best suited for specific projects. As a result, it cannot be definitively stated that one alloy is superior to another. Moreover, the optimal alloy largely depends on the requirements of the project. That is, one may excel in certain projects while the other may excel in different ones. If you have any questions or require CNC machining services for 6061 or 6063 aluminum, please call us now. Test samples are also available.